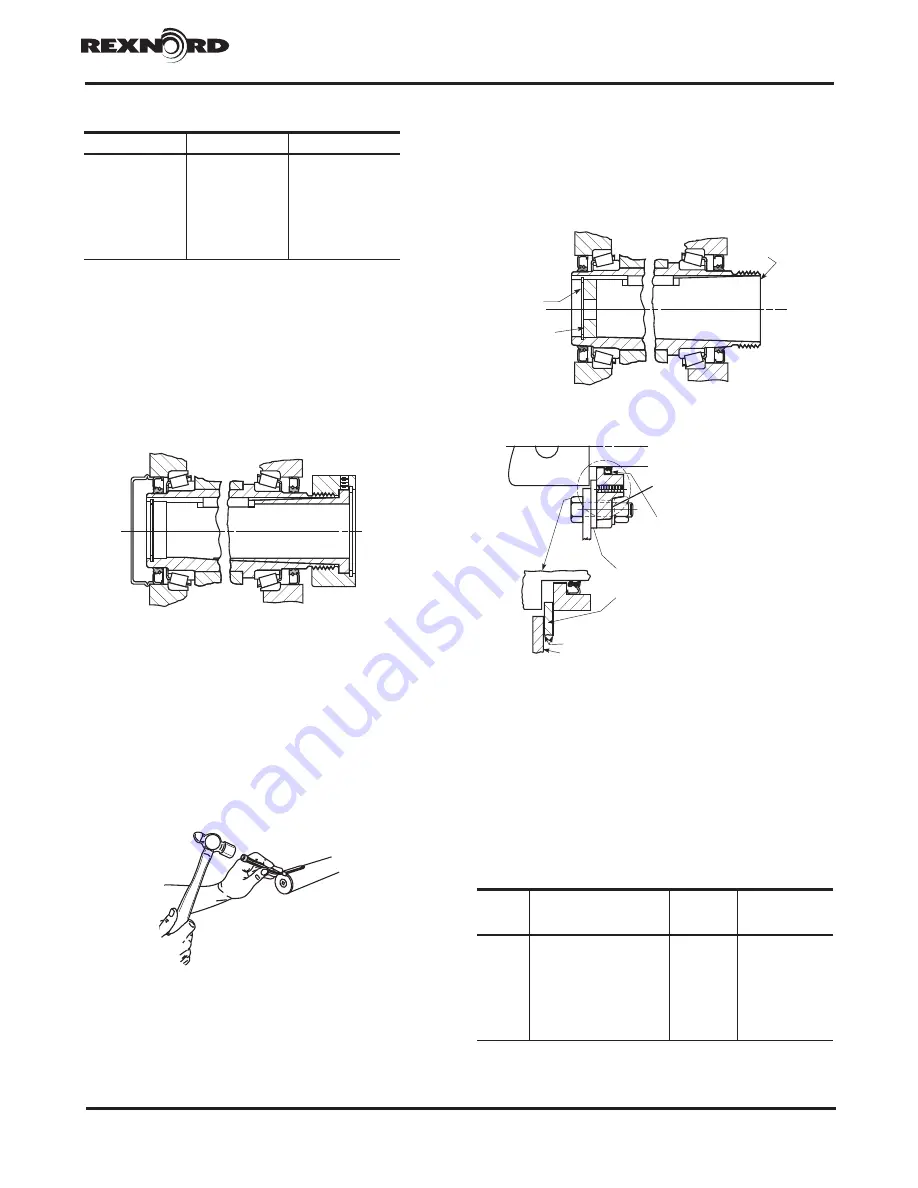
Falk Quadrive Shaft Mounted Drives Model A • Owners Manual
Sizes 5107-5315
(Page 5 of 52)
Rexnord (PN-2128394)
378-200
3001 W. Canal St., Milwaukee, WI 53208-4200 USA
January 2019
Telephone:
414-342-3131
Fax:
414-937-4359
www.rexnord.com
Supersedes 04-17
a
THIN WALL BUSHING
(with keyway slot through
the bushing wall) — With the driven shaft keyway
at the 12 o’clock position, slide bushing assembly
onto the driven shaft, nut end first, and position
the keyway slot over the shaft keyway (the bushing
may have to be pried open slightly) Insert the
drive, key furnished with the bushing, into the
shaft keyway Proceed to Step 7
4107 and will employ a 2 437” (61 9 mm) or 3 000”
(76 2 mm) diameter drive shaft, place the (2) gaskets
and trough end spacer, packaged separately, over
the trough end surface of the seal housing, Figure 6
Continue outfitting based on the type of trough end
seal to be installed: (a) Waste Packing Seal; (b) Lip
Seal or; (c) Packing Gland Seal
TABLE 2 — N Dimension Inches (mm)
DRIVE SIZE
Minimum
Maximum
5107
5.00 (127)
7.19 (183)
5115
5.55 (141)
8.05 (204)
5203
5.53 (140)
7.78 (198)
5207
6.11 (155)
8.72 (221)
5215
7.08 (180)
10.15 (258)
5307
7.39 (188)
10.69 (272)
5315
7.92 (201)
10.74 (273)
c
The minimum engagement is necessary for full bushing
engagement; the maximum engagement is only required if a
thrust plate will be++oyed to remove the drive from the driven
shaft
b
THICK WALL BUSHING
(with separate internal
and external keyways) — Insert the driven shaft
key into the driven shaft keyway If the driven
shaft has an open-ended keyway, stake the
keyway, Figure 4, to prevent axial dislocation of
the shaft key under operating conditions Slide
the bushing assembly onto the driven shaft (the
bushing may have to be pried open slightly)
Rotate the shaft so the external keyway in the
bushing is at the 12 o’clock position Then insert
the drive key, furnished with the bushing, into
the keyway Proceed to Step 7
4
JSC — NOTE
: See Appendix K for non-tapered
drive shafts Remove the hollow shaft cover
from the input side of the hollow shaft bore and
save Separate contents from the drive shaft
kit Install thrust plate and retaining ring in the
hollow shaft, Figure 5 When the drive is a size
Figure 4
HOLLOW
SHAFT
RETAINING
RING
THRUST
PLATE
OUTPUT
SIDE
Figure 5
DRIVE
SHAFT
DRIVESHAFT
MECHANICAL LIP SEAL
TROUGH END
GASKET
THROUGH END SPACER
(SIZE 5107 WITH 2.437” (61.9 mm)
& 3.000” (76.2 mm) DRIVE SHAFTS ONLY)
Figure 6
a
WASTE PACKING SEAL (Figure 7) —
Slide drive
shaft thru seal housing Insert key into drive shaft and
slide drive shaft into hollow shaft The seal housing
registers into the basic drive seal bore Install the drive
shaft thrust plate fastener thru thrust plate and torque
to the value specified in Table 3 Use the seal housing
fasteners to secure the seal housing to the basic drive
housing Refer to Table 4 for proper torque value
Reinstall hollow shaft cover Pack seal housing with
waste packing and proceed to Step 5
TABLE 3 — JR & JSC Thrust Plate Fastener
Data (
Non-Lubricated Fasteners)
DRIVE
SIZE
Fastener Size
& Grade
Torque
lb-ft (Nm)
Min Thread
Depth Inches
(mm)
5107
.500-13UNC x 3.25, GR. 8
92 (125)
2.00 (50.8)
5115
.500-13UNC x 3.25, GR. 8
92 (125)
2.00 (50.8)
5203
.625-11UNC x 3.50, GR. 8
183 (248)
2.00 (50.8)
5207
.625-11UNC x 3.50, GR. 8
183 (248)
2.00 (50.8)
5215
.875-9UNC x 3.50, GR. 8
533 (723)
2.50 (63.5)
5307
1.00-8UNC x 4.00. GR. 5
567 (769)
2.75 (69.8)
5315
1.00-8UNC x 4.00. GR. 8
792 (1074)
2.75 (69.8)
c
Fastener lengths given are for applications using tapered drive shafts
Other lengths may be needed for applications using tapered bushings
1 00-8UNC x 3 50, GR 5 for 5307JF