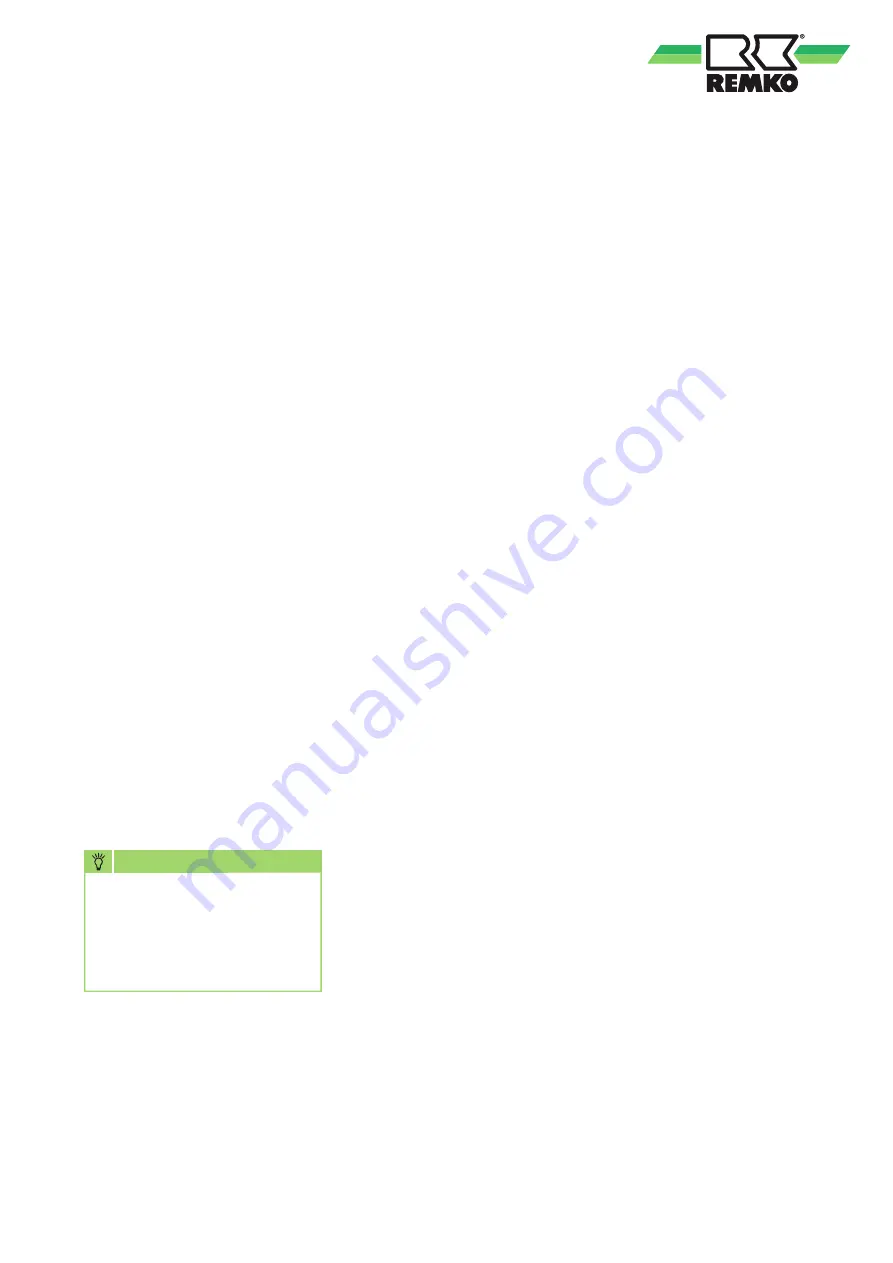
■
Wiring
Lines must be checked for the
following damage:
- Damage to the insulation
- Corrosion at the contact points
- Excessive pressure on the lines
- Damage due to vibrations
- Damage due to sharp edges
- Damage due to other influ-
ences not mentioned here
Also consider the ageing of the
material and continuous vibra-
tion loads due to compressors or
fans when checking.
■
Identify combustible refriger-
ant
Do not use any potential igni-
tion source when searching
for refrigerant leaks under any
circumstance. The use of a leak
detection lamp or other similar
devices with a naked flame is not
permitted.
1. Ensure that the components
are installed correctly.
2. Ensure that sealing materi-
als are not changed in such a
way that combustible gases or
objects could penetrate into the
interior of the components.
3. Spare parts must correspond
to the manufacturer’s specifica-
tions.
NOTE
The use of silicones can influence
the effectiveness of leak detection
devices! Intrinsically safe com-
ponents must not be insulated
before starting work.
■
Leak detection methods
The following leak detection
methods are permitted for sys-
tems with combustible refriger-
ants. Electronic equipment must
be used for detecting leaks.
These must be selected with the
sensitivity matched to the situ-
ation and recalibrated if neces-
sary (calibration must take place
in a refrigerant-free environ-
ment). The leak detection device
must be adjusted to the lowest
flammability limit (LFL) of the re-
frigerant. Liquid leakage instru-
ments are permitted for most
refrigerants. Chlorinated sub-
stances are the exception here
as the chlorine in combination
with the refrigerants can cause
corrosion on the copper cables.
If a leak is detected, all potential
open ignition sources must be
removed immediately. If a leak
has been detected in the system
which requires reworking of the
piping in the form of soldering,
the system must be completely
free of refrigerant or, if possible,
the affected part disconnected
from the system using stopcocks.
The affected system parts must
be flushed with oxygen-free
nitrogen run before and during
the repair work.
■
Emptying and evacuating the
system
If the refrigerant circuit must
be opened for repairs or other
reasons, this must be carried out
in a safe and professional way. In
any event, proceed with extreme
caution since ignition may occur
at any time! Stick to the follow-
ing procedure:
1. Drain the refrigerant
2. Flush the system with insert
gas
3. Evacuate
4. Repeat steps 2 to 3 if required
5. Opening the system by cutting
or soldering
The system must be flushed with
oxygen-free nitrogen in order to
guarantee safety. The flushing
process must be repeated multi-
ple times if necessary. Do not use
compressed air or oxygen for the
flushing process! After evacuat-
ing, flushing takes place by filling
with dried nitrogen until the
operating pressure is reached
and then the system must be
evacuated again. This flushing
process must often be repeated
until there is no more refriger-
ant in the system. After the last
flushing, the system must be
brought to the ambient pres-
sure in order to start work. The
flushing process is indispensable
when soldering work is required
on the piping. Ensure that the
vacuum pump outlet is not near
an ignition source and continu-
ous ventilation is guaranteed.
■
Filling process
The following requirements for
the general specifications must
also be fulfilled during the filling
process:
- Ensure that no contamination
occurs from other refrigerants
(residues in the filling equip-
ment).
- Keep the lines as short as pos-
sible to minimise the likelihood
of residues forming.
- Filling bottles and cylinders
must be stood upright.
- Ensure that the system is
earthed before filling.
- Label the system with the re-
frigerant type designation after
filling
- Never exceed the maximum fill
level.
The system must be checked for
leaks (pressure test!) before fill-
ing. The system must be checked
for leaks once more after fill-
ing and before commissioning.
Check for leaks again when leav-
ing the work space.
11