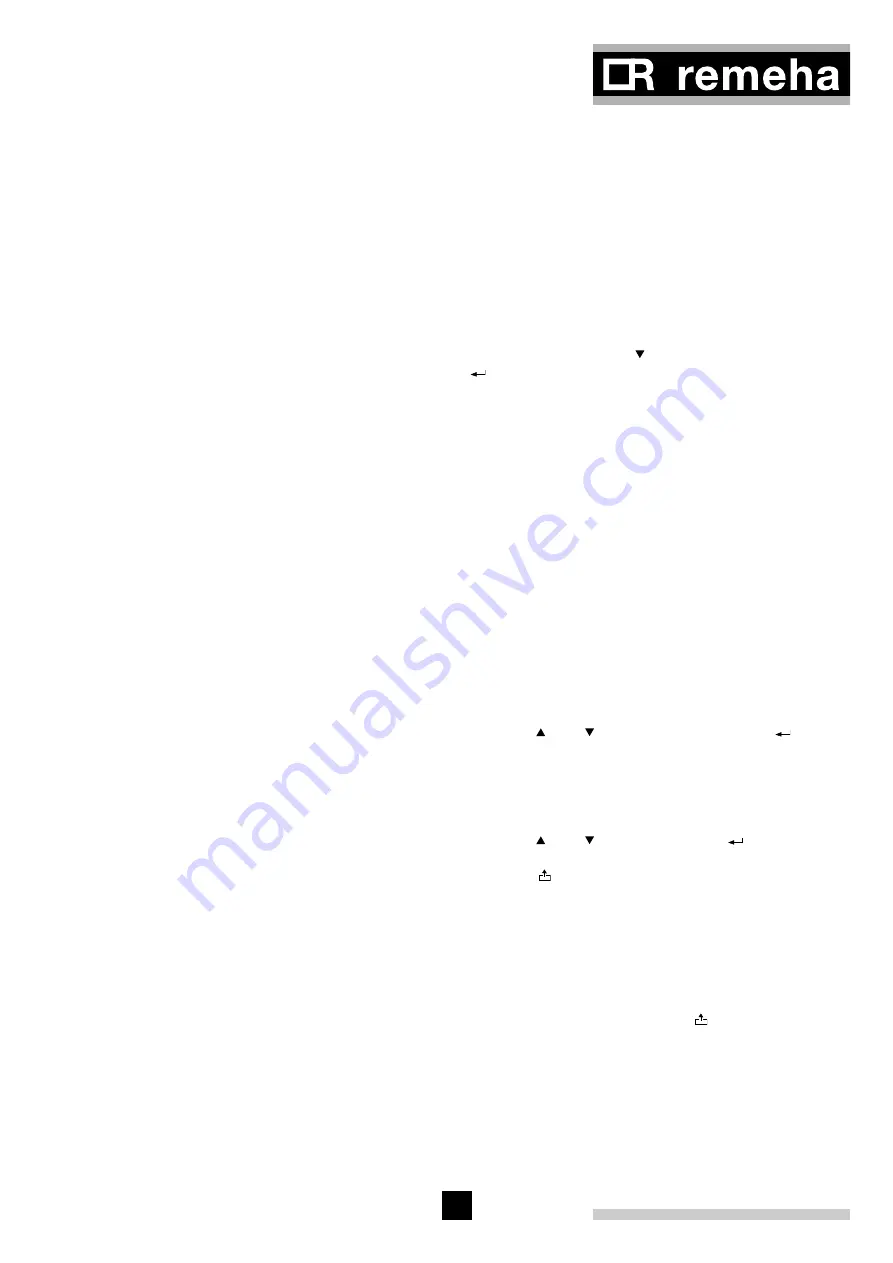
19
Option 10 Stabilisation time:
After ignition, the boiler will function on maximal load du-
ring a lapse of time to be choosen.
This period can be set between 40 and 600 seconds
(standard setting 180 seconds)
To 2) Service test
This option enables direct manual control of the boiler
by the service engineer. All outside influences are over-
ridden (except for the safety devices) at the moment the
service engineer uses the available options.
The following settings are possible (always select the
desired option using the ' ' button and confirm with the
'
' button).
When the boiler is in operation:
- Turn off the boiler.
- Switch the boiler from minimum to maximum load
(or the other way around, depending on the situation).
When the boiler is out of operation:
- Start the boiler.
- Switch the fan on or off.
- Switch the fan to maximum or minimum speed.
- Activate the ignition for 5 seconds
(first the fan will prepurge for 30 seconds).
To 3) Failure data
Five shut down and five lock out failures can be stored in
the memory of the control unit. If a failure is repeated
several times, it is stored only once. For every failure
stored the operational condition at the moment of failure
can also be displayed. This facilitates easy trouble shoo-
ting. The locking or the blocking failure memory can be
selected in the main menu of the "History data" option,
using the ' ' and ' ' buttons. Confirm with the '
' button.
Depending on the option selected, the number of block-
ing or lock out failures stored in the memory (maxi mum
5 of each) is displayed. Failure No. 1 is the most recent
failure, failure No. 2 the last but one, etc. To know which
failure occurred last, the failure counter must be set to 1
using the ' ' and ' ' buttons. When the '
' button is
pressed for confirmation, the failure in question is seleced.
Using the ' ' button, various menus can now be called
up, all indicating the operational condition of the boiler at
the moment of failure (see also para. 12).
The memory of the blocking failures is lost when the line
voltage is lost, the memory of lock out failures is saved.
To 4) Service level II (factory level)
Not accessible.
From every menu within the service level the user level
can be accessed by pressing the ' ' button once or
several times, depending on the position within the menu
structure at that time. If the service level is exited,
the service code entered remains active for another 30
minutes. The service level can therefore automatically be
accessed from the user level during these 30 minutes
without having to enter the code again.
Furthermore, the control unit will automatically switch
back to the user level after 30 minutes.
Option 2 Language:
A choice of English, Dutch, French or German.
Option 3 Setpoint hysteresis:
Using this parameter, the switch hysteresis can be set
at the flow temperature. As standard, this value is set at
10°C. The boiler will always issue a control stop when the
flow temperature equals the preset maximum flow tem-
pe5°C. The switch hysteresis determines when
the boiler will switch on. A setting of 10°C means that the
temperature must fall 10°C below the preset maximum
operating tempe5°C before the boiler switches on.
This setting can be varied between 5 and 15°C.
Option 4 Maximum flue gas temperature:
The maximum flue gas temperature can be set between
80 and 230°C (standard setting is 230°C).
Option 5 Pressure settings:
With this option, it is possible to set the maximum and
minimum differential pressures of the boiler. The maxi-
mum differential pressure is set as standard at the setting
for 100% load (see the label on the boiler, adjacent to the
type plate). This setting can be reduced in order to lower
the maximum boiler load. This means that the maxi mum
boiler load can be perfectly adjusted to comply with the
heat requirements of the building. Con sult our technical
department. The mi ni mum differential air pressure is set
as standard at 50% load. This setting can be reduced
down to the value for a minimum load of 33%
(see label on the boiler, adjacent to the type plate).
Option 6 Relay switch:
The control system has two operation sensor relays, one
for sensing low power, and one for sensing high power.
The change-over point from low to high can be set using
these parameters. As standard, the setting is 95%.
In other words, at a power below 95%, the operating
message ‘low power’ is issued, and at a power exceeding
95%, an operating message ‘high power’ is issued.
The chan ge-over point can be set between 10 and 99%
and, if required, altered.
Option 7 Gas leak detection:
If a gas leak control is built in, this can be announced to
the control unit via this screen.
Option 8 Set hours:
If the display print has to be replaced, it is possible to
transfer boiler service hours onto the new print.
Low flame and high flame hours need to be noted. After
which it is possible to set these hours onto the new print
by using option nr. 8.
Option 9 High limit temperature:
If desired, it is possible to decrease the high limit tempe-
rature of the boiler.
Attention: This setting can only be lowered.
If you do so, please also lower the maximum service
temperature in order to avoid an boiler lock-out.