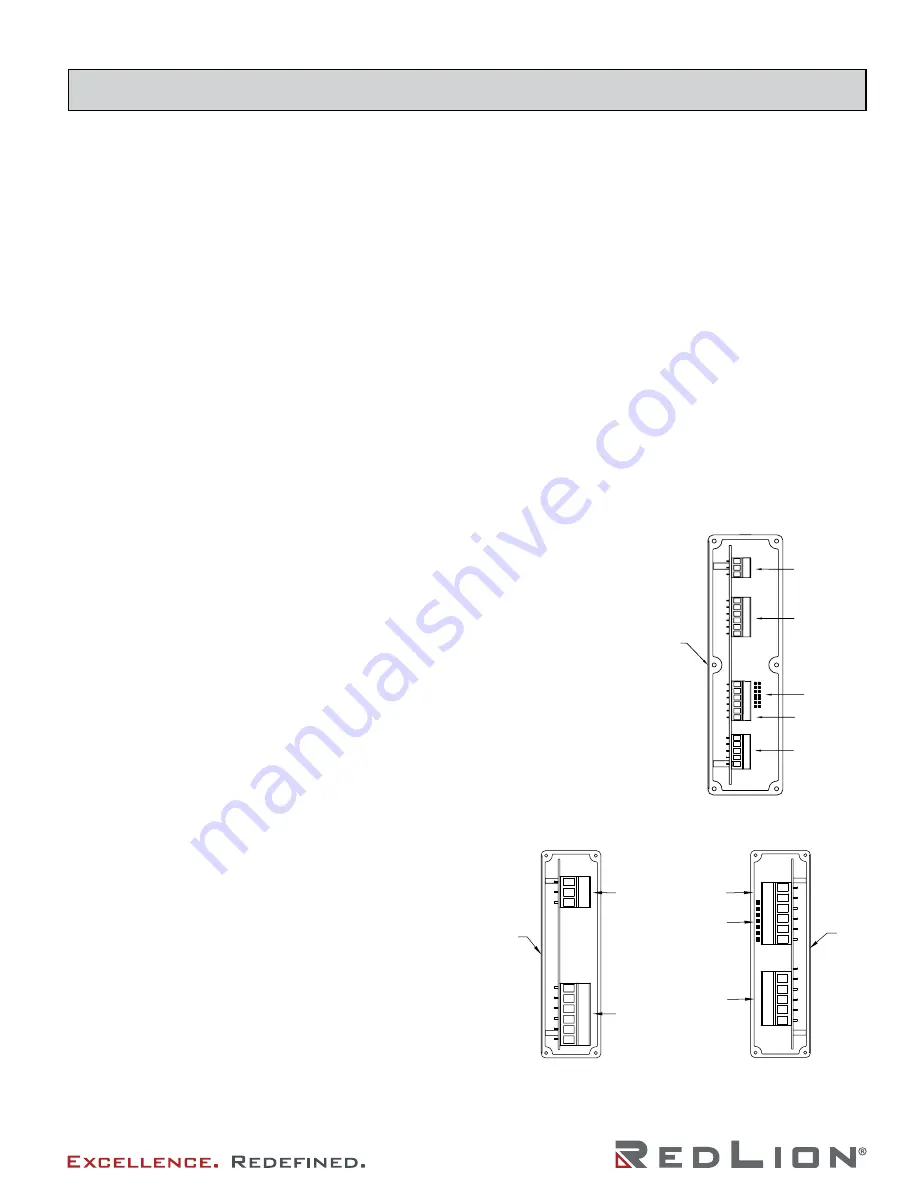
Revised 08 2021
Drawing No. LP0673
3
3.0 W
IrIng
the
M
eter
EMC INSTALLATION GUIDELINES
Although Red Lion Controls Products are designed with a high degree
of immunity to Electromagnetic Interference (EMI), proper installation
and wiring methods must be followed to ensure compatibility in each
application. The type of the electrical noise, source or coupling method
into a unit may be different for various installations. Cable length, routing,
and shield termination are very important and can mean the difference
between a successful or troublesome installation. Listed are some EMI
guidelines for a successful installation in an industrial environment.
1. A unit should be mounted in a metal enclosure, which is properly
connected to protective earth.
2. Use shielded cables for all Signal and Control inputs. The shield
connection should be made as short as possible. The connection point
for the shield depends somewhat upon the application. Listed below
are the recommended methods of connecting the shield, in order of
their effectiveness.
a. Connect the shield to earth ground (protective earth) at one end
where the unit is mounted.
b. Connect the shield to earth ground at both ends of the cable, usually
when the noise source frequency is over 1 MHz.
3. Never run Signal or Control cables in the same conduit or raceway
with AC power lines, conductors, feeding motors, solenoids, SCR
controls, and heaters, etc. The cables should be run through metal
conduit that is properly grounded. This is especially useful in
applications where cable runs are long and portable two-way radios
are used in close proximity or if the installation is near a commercial
radio transmitter. Also, Signal or Control cables within an enclosure
should be routed as far away as possible from contactors, control
relays, transformers, and other noisy components.
4. Long cable runs are more susceptible to EMI pickup than short cable
runs.
5. In extremely high EMI environments, the use of external EMI
suppression devices such as Ferrite Suppression Cores for signal and
control cables is effective. The following EMI suppression devices (or
equivalent) are recommended:
Fair-Rite part number 0443167251 (RLC part number FCOR0000)
Line Filters for input power cables:
Schaffner # FN2010-1/07 (Red Lion Controls # LFIL0000)
6. To protect relay contacts that control inductive loads and to minimize
radiated and conducted noise (EMI), some type of contact protection
network is normally installed across the load, the contacts or both. The
most effective location is across the load.
a. Using a snubber, which is a resistor-capacitor (RC) network or metal
oxide varistor (MOV) across an AC inductive load is very effective at
reducing EMI and increasing relay contact life.
b. If a DC inductive load (such as a DC relay coil) is controlled by a
transistor switch, care must be taken not to exceed the breakdown
voltage of the transistor when the load is switched. One of the most
effective ways is to place a diode across the inductive load. Most
RLC products with solid state outputs have internal zener diode
protection. However external diode protection at the load is always
a good design practice to limit EMI. Although the use of a snubber
or varistor could be used.
RLC part numbers: Snubber: SNUB0000
Varistor: ILS11500 or ILS23000
7. Care should be taken when connecting input and output devices to the
instrument. When a separate input and output common is provided,
they should not be mixed. Therefore a sensor common should NOT be
connected to an output common. This would cause EMI on the
sensitive input common, which could affect the instrument’s operation.
Visit RLC’s web site at http://www.redlion.net/emi for more information
on EMI guidelines, Safety and CE issues as they relate to Red Lion
Controls products.
WIRING OVERVIEW
Electrical connections are made via pluggable terminal blocks located
inside the meter. All conductors should conform to the meter's voltage
and current ratings. All cabling should conform to appropriate standards
of good installation, local codes and regulations. It is recommended that
the power supplied to the meter (DC or AC) be protected by a fuse or
circuit breaker. When wiring the meter, compare the numbers on the
label on the back of the meter case against those shown in wiring
drawings for proper wire position. Strip the wire, leaving approximately
0.4" (10 mm) bare lead exposed (stranded wires should be tinned with
solder.) Insert the lead under the correct screw clamp terminal and
tighten until the wire is secure. (Pull wire to verify tightness.) Each
terminal can accept up to one #14 AWG (2.55 mm) wire, two #18 AWG
(1.02 mm), or four #20 AWG (0.61 mm). Use copper conductors only,
with insulation rated at 90°C.
WIRING CONNECTIONS
Internal removable terminal blocks are used for power and signal
wiring. Access to terminal blocks is through conduit fittings. Remove end
plates with ¼" nut driver. For LD4 versions, all wiring is on right side of
unit. For LD2 versions, power and relay wiring is on the right side and the
input, serial, DC out and user input is on the left side.
Feed the wire stripped end of cable(s) through the cord grip(s).
Un-plug the internal removable terminal blocks and wire appropriately.
Plug in the terminal blocks, connect the drain wire from shielded
cable(s) to the screw on the side plate for proper grounding, and slide the
end plate(s) into place and
tighten to case. Hand tighten
all cap screws and then tighten
the cap screws at the opposite
corner diagonally.
Important
: To maintain the
Type 4X/IP65 specification,
the cord grip must be
tightened around a cable
with an outside diameter of
0.181" (4.6 mm) to 0.312"
(7.9 mm). If the cord grip is
unused, remove it and
replace with the LD cord
grip plug (part # LDPLUG00).
The LDPLUG00 must be
ordered separately.
Front
TBA
3
2
1
Front
TBB
46
5
13
2
TBC
TBD
3
1
2
4
56
RANGE SELECT
1
23
4
5
LD2
RIGHT SIDE VIEW
LEFT SIDE VIEW
Front
TBA
3
2
1
46
5
3
2
1
TBB
RANGE SELECT
6
5
4
23
1
TBC
5
34
2
1
TBD
LD4