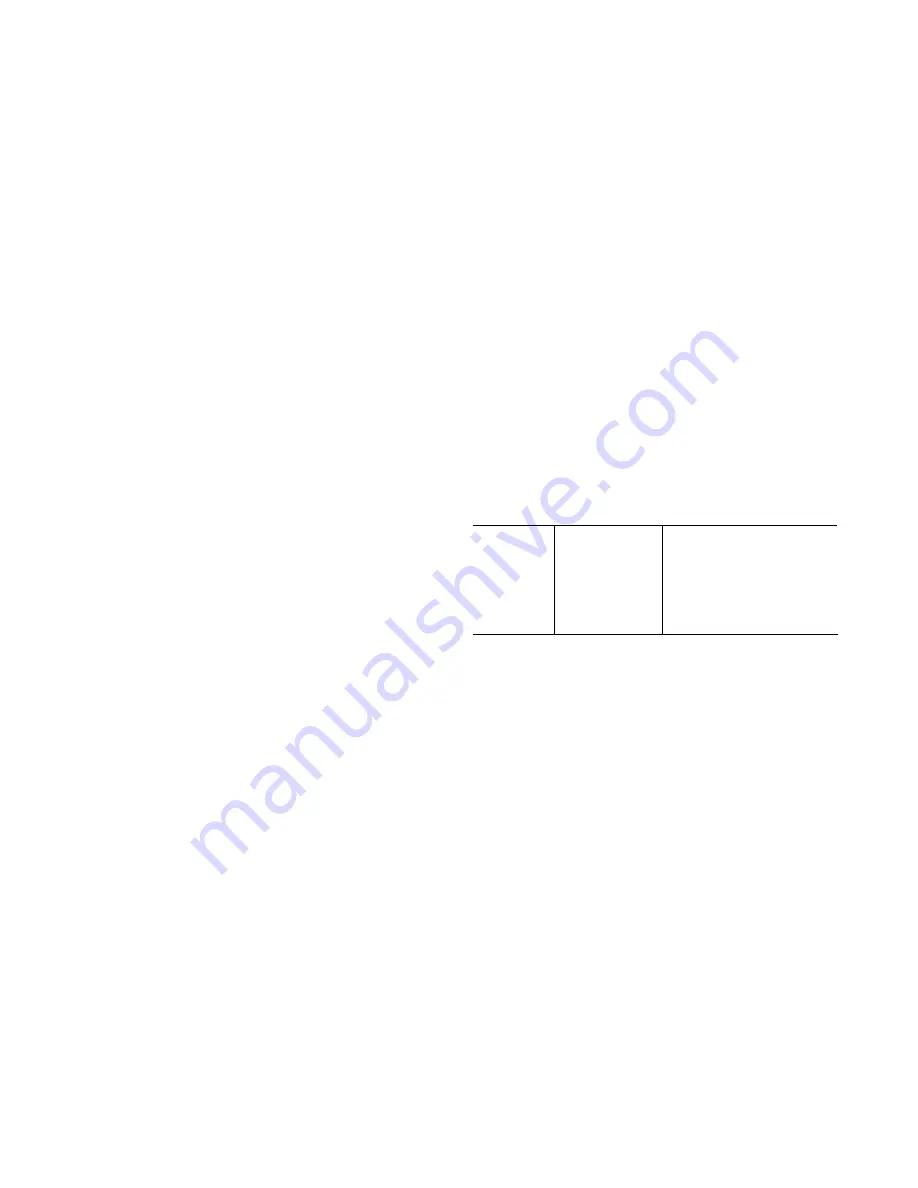
DOMINATOR INSTALLATION AND OPERATION INSTRUCTIONS
Page 11
Horizontal vent systems shall terminate at least
4 ft
,
1.2 m
below,
4 ft
,
1.2 m
horizontally from or
1 ft
,
0.3 m
above any door, window or gravity air inlet into
any building. It must not terminate less than
4 ft
,
1.2 m
horizontally from, and in no case above or below, unless
a
4 ft
,
1.2 m
horizontal distance is maintained, from
electric meters, gas meters, regulators and relief
equipment and not less than
7 ft
,
2.1 m
from any adjacent
public walkway. The bottom of the vent terminal(s) shall
be located at least
5 ft
,
1.5 m
above the air intake
terminal(s) unless there is a minimum
5 ft
,
1.5 m
,
horizontal separation between them. Avoid terminal
locations likely to be affected by winds, snowdrifts, people
and pets. Protect building materials and vegatation from
degradation caused by the fl ue gases.
To determine the appropriate power venter for the boiler/
water heater, see Table 6, Power Venter Sizes. Follow
the power venter manufacturer’s installation instructions.
Table 6 - Power Venter Sizes
OUTDOOR VENTING
When installed outdoors the Dominator must be fi tted
with the factory supplied outdoor vent hood and air
intake hood, see Figure 8. Multiple units must be spaced
per Figure 9.
The boiler/water heater must be at least
10 ft
,
3.0 m
from any door, window or gravity air inlet into any
building and at least
3 ft
,
0.9 m
from any overhang
unless local codes dictate differently.
Avoid locations where wind defl ection off of adjacent
walls, buildings or shrubbery might cause a down draft.
The unit(s) should be located at least
3 ft
,
0.9 m
from
structures. Outdoor installations are not recommended
in areas where the danger of snow blockage exists.
CAUTION: Do not place the boiler/water heater in a
location that would subject it to runoff from adjacent
buildings or damage may occur voiding the
warranty!
Horizontal vent systems shall terminate at least
4 ft
,
1.2 m
below,
4 ft
,
1.2 m
horizontally from or
1 ft
,
0.3 m
above any door, window or gravity air inlet into
any building. It must not terminate less than
4 ft
,
1.2 m
horizontally from, and in no case above or below, unless
a
4 ft
,
1.2 m
horizontal distance is maintained, from
electric meters, gas meters, regulators and relief
equipment and not less than
7 ft
,
2.1 m
from any
adjacent public walkway. The bottom of the vent
terminal(s) shall be located at least
5 ft
,
1.5 m
above
the air intake terminal(s) unless there is a minimum
5 ft
,
1.5 m
horizontal separation between them. Avoid
terminal locations likely to be affected by winds, snow
drifts, people and pets. Protect building materials and
vegetation from degradation caused by the fl ue gases.
Vertical Direct Vent Systems - See Figure 6
The maximum length for the ver tical vent and
combustion air pipes is
35 ft
,
10.7 m
plus two 90°
elbows for each. If any part of a single wall metal vent
system passes through an unheated space it must be
insulated with insulation rated for
400°F
,
204°C
. Structual
penetrations must be made using approved fi re-stops.
A listed, nonrestrictive vent cap must be used. The top
of a vertical vent system must extend at least
5
1
/
2
ft
,
1.7 m
above the roof surface that it passes through,
4 ft
,
1.2 m
above the intake air cap, see Figure 6.
HORIZONTAL VENT,
NEGATIVE PRESSURE, CATEGORY I
In this confi guration a wall-mounted power venter must
be used to pull the fl ue products horizontally from the
unit and vent them to the outdoors, see Figures 3, 4 &
5. The air for combustion is taken from the space in
which the unit is installed, or from the outdoors. The
applicable instructions under the “COMBUSTION AIR
& VENTILATION” section must be followed!
To maximize the performace of single wall sheet metal
vent systems locate 90° elbows as far from the boiler
as possible and from one another. For best results,
horizontal vent systems should be as short and straight
as possible.
When horizontal vent runs exceed
5 ft
,
1.5 m
they must
be supported at
3 ft
,
0.9 m
intervals with overhead
hangers. The vent system must be pitched down, toward
the vent terminal,
1/4 in/ft
,
20 mm/m
. If any part of a
single wall metal vent system passes through an
unheated space it must be insulated with insulation
rated for
400°F
,
204°C
.
Dominator Power Venter
Max. Pipe Length
Model
Model
FT
m
300
HS-1
30*
9
400
HS-2
100
31
600
HS-2
67**
21
750-900
HS-3
100
31
1050-1350
HS-4
100
31
1500-2100
HS-5
100
31
*Choose HS-2 for
100 ft
,
31 m
, Max. Pipe length
**Choose HS-3 for
100 ft
,
31 m
, Max. Pipe Length