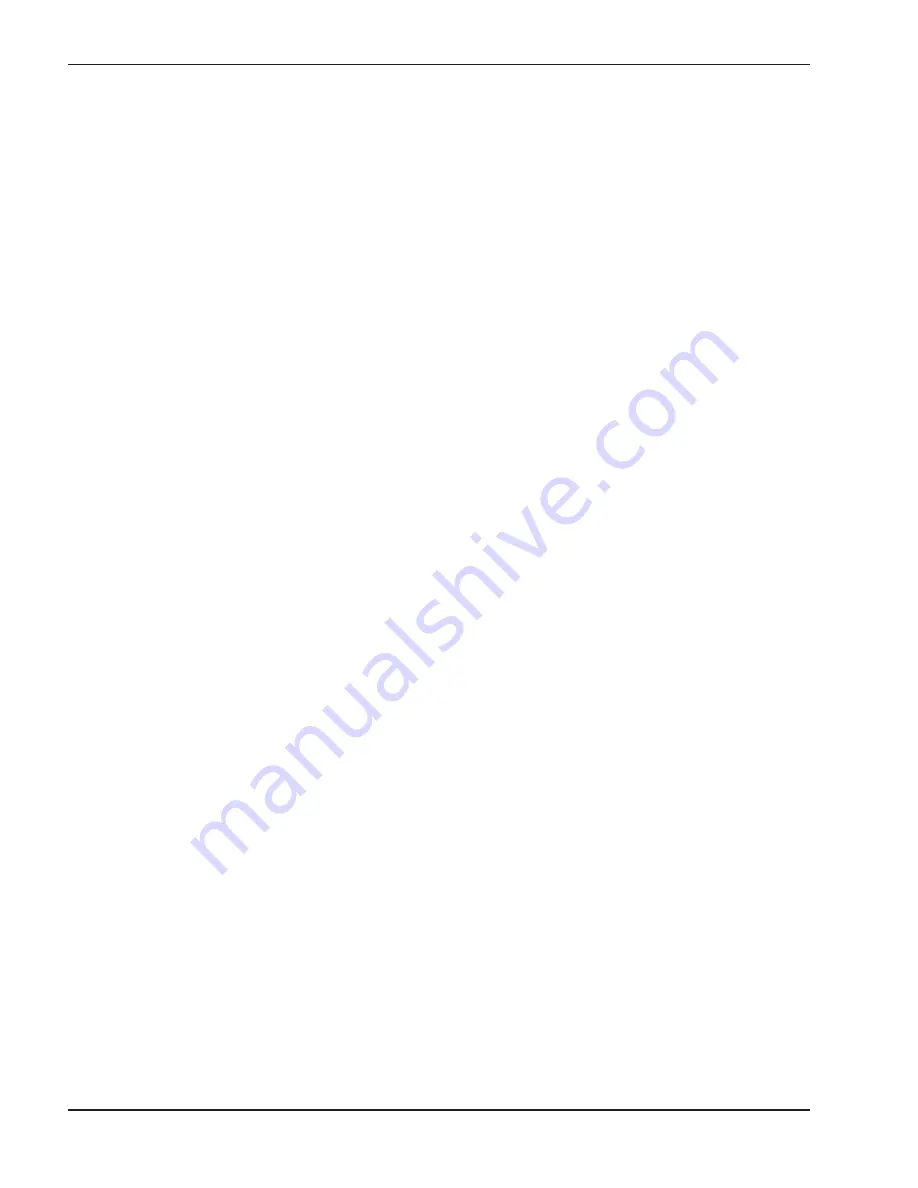
36
MECHANICAL PROBLEM
When boiler is turned on nothing
happens.
Thermostat in "ON" position causes
relay and pump to operate, but boiler
does not fire.
Continuous shut down of manual reset
high limit.
Sooting
CAUTION-Soot may be combustible.
Wet down and exercise caution when
cleaning.
Continuous shut down of low water cut-
off or flow switch.
Low flame.
Outer jacket very hot (blistered paint).
POSSIBLE CAUSE
Pilot is not lit………………………………
No power to the boiler…………………...
Bad transformer………………………….
Inoperative thermostat…………………..
Inoperative toggle switch………………..
Inoperative relay………………………….
Main gas valve is closed……………….
Plugged bleed line on gas valve or
gas pressure regulator…………………..
Broken pump coupler……………………
Shutdown by low water cut-off,
caused by air……………………………..
Gas valve defective………………………
Temperature setting too low…………….
Low water flow……………………………
Interrupted pump operation……………..
Modulating control set too high………..
Mechanical modulating control…………
Air starvation……………………………..
Condensation……………………………..
Toxic fumes which cause a chemical
reaction with copper tubes or destroy
combustion……………………………….
Improper venting…………………………
Insufficient system flow………………….
Low water due to leaking………………..
Air in system………………………………
Line strainer dirty…………………………
Lime in heat exchanger…………………
Gas supply………………………………..
Insects or debris clogging burners..........
Burner intake ports low gas pressure….
Venting or combustion air……………….
Broken refractory…..…………………….
CORRECTIVE ACTION
Light pilot. (Standing pilot models)
Check the circuit breaker, outdoor con-
troller, etc., upstream of boiler.
If power to Leads L1 and L2 of trans-
former, but no power on 24V side, re-
place.
Jumper thermostat. Replace with new if
boiler fires.
If power to toggle switch, but not
through switch, replace.
If power to relay, but not operating,
replace.
Open valve.
Loosen bleed line and clean.
Replace coupler. Inspect bearing as-
sembly, and if frozen, lubricate or re-
place.
Bleed air from system.
Check for power to gas valve. If valve
has power but will not open, check vent
tube for blockage. If clear, replace
valve.
Reset high limit to higher temperature.
Check system water pumps.
Check pump oil if necessary.
Reset modulator to a lower setting.
Check and replace if necessary.
Refer to installation instructions regard-
ing combustion air requirements.
Set bypass valve to prevent boiler inlet
temperature from dropping below
105 °F.
Remove all sources of fumes, such as
freon, chloride, or isolate the boiler.
Follow recommended vent installation
instructions.
Check pumps and piping.
Inspect for leakage and repair.
Inspect for leakage and repair. Install
an automatic air vent.
Clean.
Ream tubes.
Debris in gas line (pipe dope, rocks,
etc.). Gas line too small.
Improperly sized gas meter.
Gas regulator adjustment.
Clean burners.
Adjust gas pressure.
Refer to installation instructions regard-
ing combustion air requirement.
Replace refractory panels.