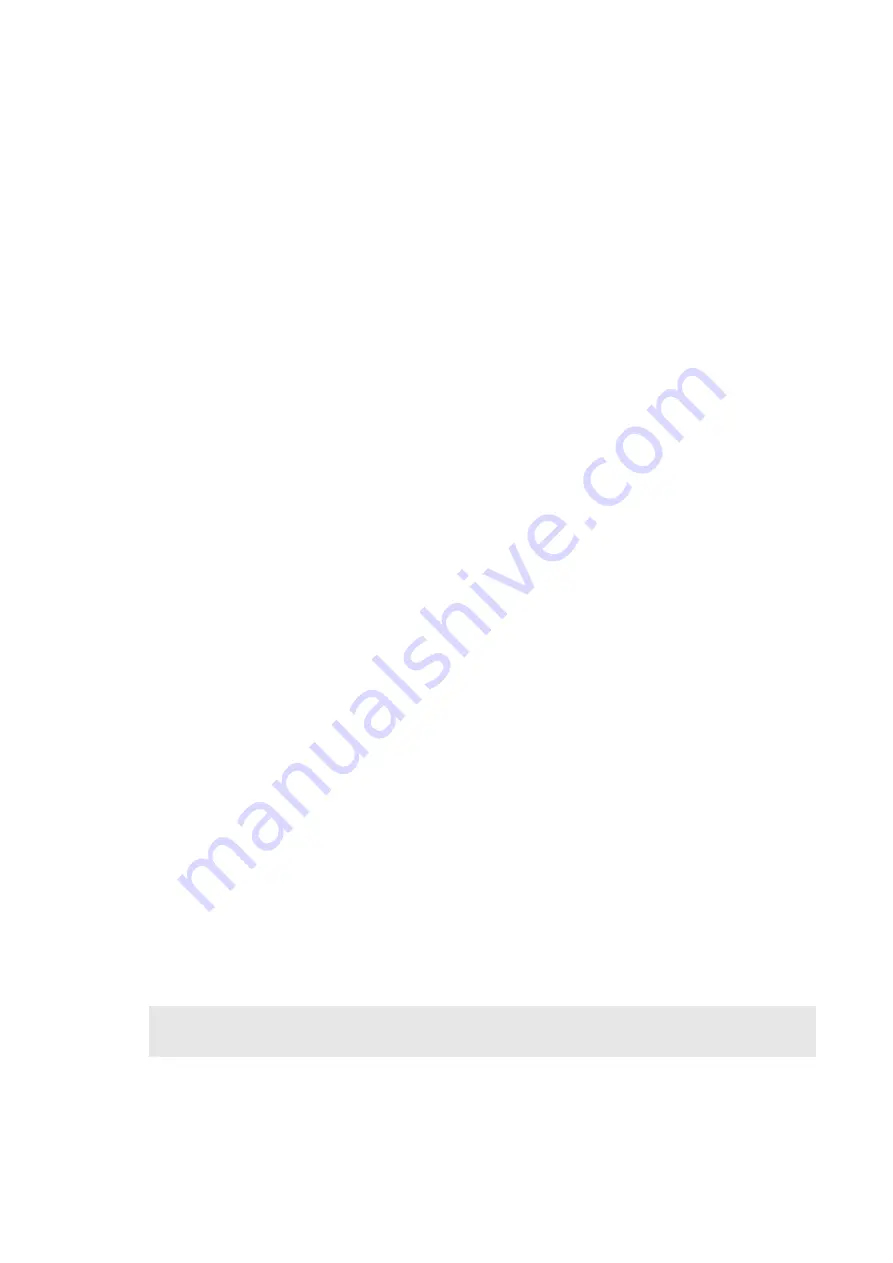
Project Name / Date
Division 23 52 33.13 - 3
mounted and wired, which automatically shuts off the boiler pump at a set period after boiler
shut-down to avoid standby losses associated with constant pump operation.
G. Firing Mode
1. For model 989B, provide two-stage firing control of the gas input to the boiler.
2. For model 1259B, provide three-stage firing control of the gas input to the boiler.
3. For models 1529B – 2339B, provide four-stage control of the gas input to the boiler.
H. Boiler Diagnostics
1. Provide external LED panel displaying the following boiler status/faults:
a. Power on - Green
b. Call for heat – Amber
c. Burner on – Blue
d. Safety fault - Red
2. A Central Point Wiring board with diagnostic LED’s indicating the status of each relay.
3. Provide ignition module indicating the following flash codes by LED signal:
a. 1 flash – low air pressure
b. 2 flashes – flame in the combustion chamber w/o CFH
c. 3 flashes – ignition lock-out (flame failure)
d. 4 flashes – low hot surface igniter current
e. 5 flashes – low 24VAC
f. 6 flashes – internal fault
I.
Combustion Chamber: The lightweight, high temperature, multi-piece, interlocking ceramic fiber
combustion chamber liner shall be sealed to reduce standby radiation losses, reducing jacket
losses and increasing unit efficiency.
J. Venting
1. When routed vertically, the boiler’s flue material and size shall be in accordance with the
National Fuel Gas Code, ANSI Z223.1/NFPA54 latest edition (Category I).
2. When routed horizontally, the boiler(s) flue material and size shall meet or exceed the
requirements as specified for Category III in the National Fuel Gas Code, ANSI Z223.1/NFPA
54 latest edition.
3. The boiler(s) shall be ducted combustion air ready.
K. Cabinet
1. The corrosion-resistant galvanized steel jackets shall be finished with a baked-on epoxy
powder coat which is suitable for outdoor installation, applied prior to assembly for complete
coverage, and shall incorporate louvers in the outer panels to divert air past heated surfaces.
2. The boiler(s), if located on a combustible floor, shall not require a separate combustible floor
base.
3. The boiler(s) shall have the option of venting the flue products either through the top or the
back of the unit.
4. Combustion air intake shall be on the left side of the cabinet, right side optional.
L. Operating Controls
1. The boiler(s) shall feature an optional multi-stage digital controller with adjustable outdoor
reset, mounted and wired.
2. Water and air temperature sensors shall be shipped loose for field installation by installing
contractor.
Specifier Note: The remaining items in this section are options. Delete those that are not being
specified.
IMPORTANT:
The Cold Water Start and Cold Water Run Systems cannot be
used on the same boiler.
M. Boiler Pump - Refer to Equipment Schedule
N. SureRack™ Boiler Stacking Kit
1. The boilers shall be stacked directly one on top of the other, without offset, to minimize
footprint.
O. Cold Water Start System
1. The boiler(s) shall be configured with a cold water start automatic proportional by-pass system