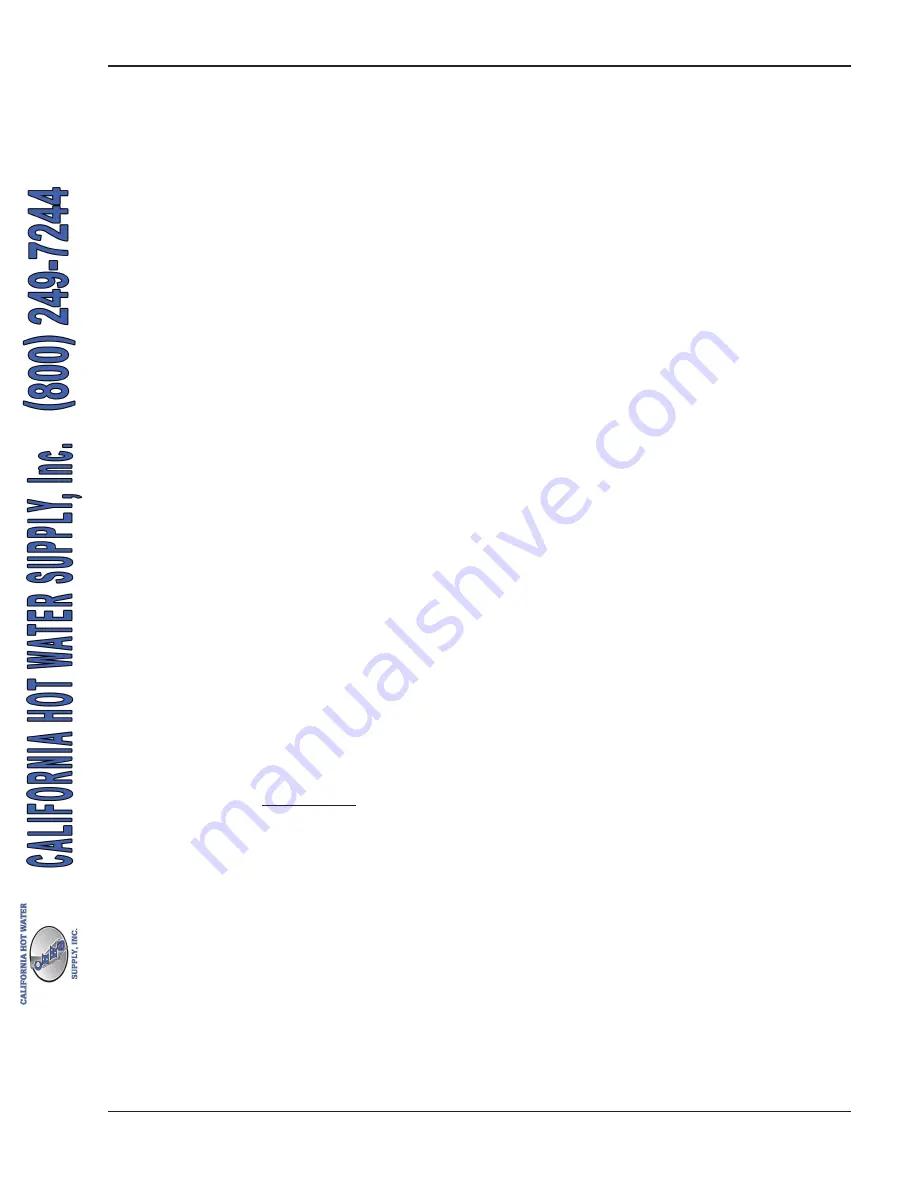
4.
Conduct a combustion test at full fire. Carbon diox-
ide should be 8.5 to 9.0% at full fire for natural gas,
and between 9.5 to 10.0% for propane gas.
Carbon monoxide should be < 100 ppm.
5.
Check valve coil for 60 cycle hum or buzz. Check
for leaks at all valve fittings using a soapy water
solution (while heater is operating). Test other
operating parts of all safety shut-off and control
valves and increase or decrease settings
(depending on the type of control) until the safety
circuit opens. Reset to original setting after each
device is tested.
6.
Perform leakage test on gas valves (See Fig. 49).
7.
Test air switch in accordance with manufacturer’s
instructions. (Turn panel switch to the “On” posi-
tion until blower is proven, then turn the switch to
“Off.”
8.
Inspect and clean burner using shop air.
9.
Reset fault history after any testing.
As Required
1.
Recondition or replace low water cut-off device (if
equipped).
2.
Check drip leg and gas strainers.
3.
Check flame failure detection system. (See “Post
Start-Up Check,” page 46.)
4.
Check igniter. (Resistance reading should be 42-
70 ohms at ambient temperature).
5.
Check flame signal strength. (Flame signal should
be greater than 1
microampere
as measured at
the 2 pins on the upper left corner of the ignition
control).
6.
Check firing rate control by checking the manifold
pressure. (See “Manifold Check” on page 44.)
7.
Test safety/safety relief valve(s) in accordance
with ASME Heater and Pressure Vessel Code
Section IV and Section VIII as applicable.
APPENDIX
Inside Air Contamination
All heaters experience some condensation during
start-up. The condensate from flue gas is acidic.
Combustion air can be contaminated by certain vapors
in the air which raise the acidity of the condensate.
Higher acidity levels attack many materials including
stainless steel, which is commonly used in high effi-
ciency systems. The heater can be supplied with
corrosion-resistant, non-metallic intake air vent materi-
al. You may, however, choose to use outside
combustion air for one or more of these reasons:
1.
Installation is in an area containing contaminants
listed below which will induce acidic condensation.
2.
You want to reduce infiltration into your building
through openings around windows and doors.
3.
You are using AL29-4C stainless steel vent pipe,
which is more corrosion-resistant than standard
metallic vent pipe. In extremely contaminated ar-
eas, this may also experience deterioration.
Products causing contaminated combustion air:
•
spray cans containing chloro/fluorocarbons
•
permanent wave solutions
•
chlorinated waxes/cleaners
•
chlorine-based swimming pool chemicals
•
calcium chloride used for thawing
•
sodium chloride used for water softening
•
refrigerant leaks
•
paint or varnish removers
•
hydrochloric acid/muriatic acid
•
cements and glues
•
antistatic fabric softeners used in clothes dryers
•
chloride-type bleaches, detergents, and cleaning
solvents found in household laundry rooms
•
adhesives used to fasten building products
•
similar products
Areas where contaminated combustion air commonly
exists:
•
dry cleaning/laundry areas
•
metal fabrication plants
•
beauty shops
•
refrigeration repair shops
•
photo processing plants
•
auto body shops
•
plastic manufacturing plants
•
furniture refinishing areas and establishments
•
new building construction
•
remodeling areas
•
open pit skimmers
Check for areas and products listed above before in-
stalling heater. If found:
•
remove products permanently, OR
•
install TruSeal direct vent.
California Hot Water Supply, Inc.
(800) 249-7244
51