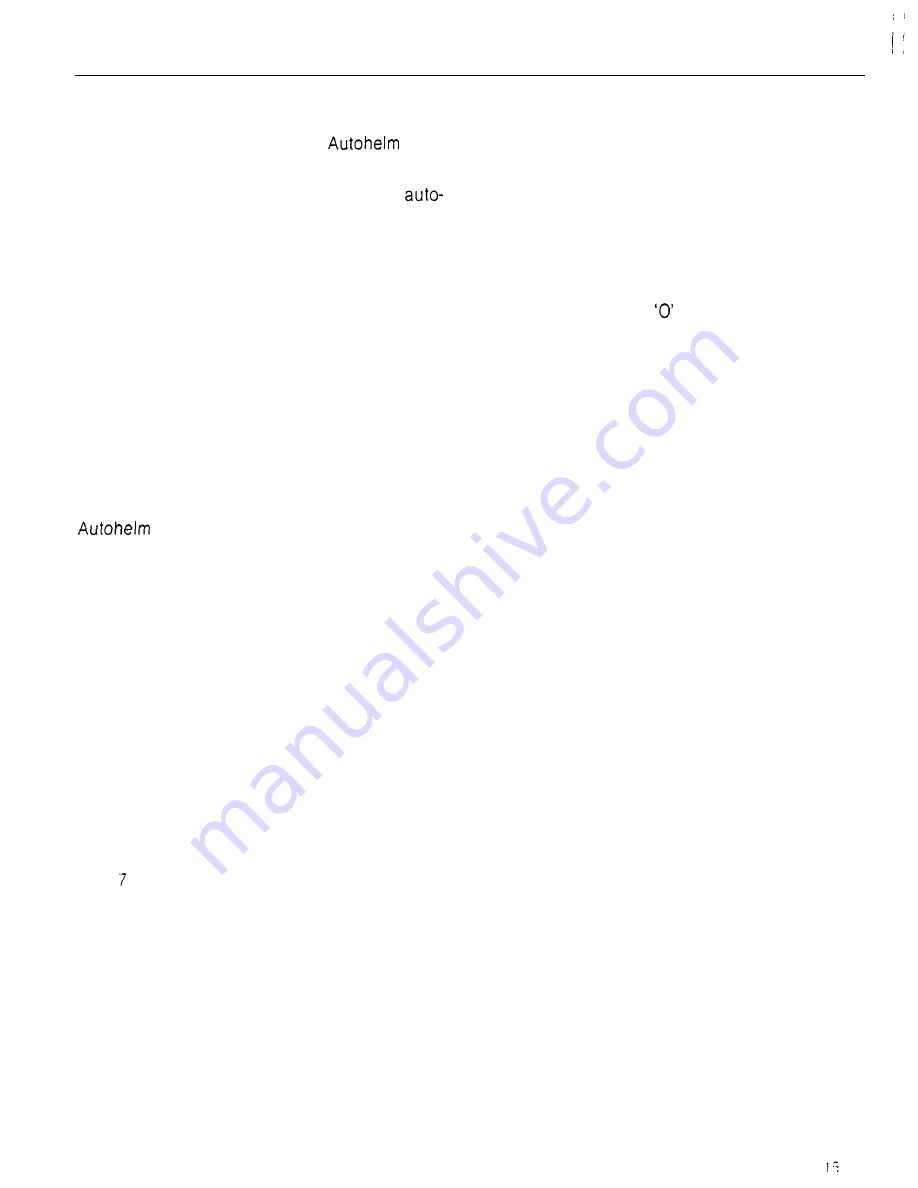
3.0 OPERATION
3.1 BASIC PRINCIPLES
The following description of the
5000
principle of operation will help in providing a
complete understanding of its controls. The
control unit houses an extremely sensitive
setting electronic compass. When the autopilot
is in operation, deviation from course is
continuously monitored by the compass and
corrective rudder is applied by the drive unit to
return the vessel to course. The amount of
applied rudder is proportional to the course
error at any time, and thus when the original
course is restored the rudder will be
neutralised. The amount of the rudder applied
for a given off-course error is adjustable to
match both the steering characteristics of the
vessel and speed through the water. A vessel
with a small rudder for example, will require
more corrective helm than a similar sized vessel
with a larger rudder. Similarly, a high speed
power boat will require considerably less
corrective helm at planing speeds than it will at
lower displacement speeds (Fig.1 8.)
The characteristic which distinguishes the
5000 is its ability to make automatic
correction for changes in trim or weather helm.
When changes in trim occur the set course can
only be maintained by the application of
permanent rudder offset to restore balance.
Many automatic pilots are incapable of this and
will allow the vessel to bear on to a new
heading to achieve a new state of balance.
Under these circumstances the Autoheim 5000
detects that the original course has not been
restored and will continue to apply additional
helm in the appropriate direction until the
vessel returns to the original heading. This
facility ensures that the originally set course is
held irrespective of changes in balance that
may occur during the course of a passage.
3.2 CONTROLS
3.2.1 CONTROL UNIT
Fig.1 shows the position of all controls. Each
control has the following functions:
OFF
Push to de-energise the autopilot. The electro-
magnetic clutch in the drive unit is disengaged
for manual steering.
SET
Push to energise the compass circuit and
initiate the automatic compass setting
sequence. The compass is finally set to the
manually steered heading when both the red
and green pilot lights are extinguished.
DUTY
Push to fully energise the autopilot for
automatic steering duty.
REMOTE
Push to transfer basic automatic pilot control to
the auxiliary control unit.
SEA
Rotate to adjust compass sensitivity to suit sea
conditions. In position
the compass is fully
sensitised for operation in calm sea conditions.
Clockwise rotation to position ‘7’ progressively
densensitises the compass for operation in
rough sea conditions. Adjustment of this
important control is fully discussed later.
R U D D E R
Rotate to adjust rudder response. In position ‘0’
rudder movement is minimised. Clockwise
rotation to position ‘7’ progressively increases
the amount of applied rudder. Adjustment
technique is fully discussed later.
STEER
Rotate counter-clockwise or clockwise to alter
course to port or starboard respectively. Each
scale division represents 5 degrees of course
alteration. The steer control will rotate
automatically when the control unit is switched
to
Set.
The controls on the rear case are used to
adjust the auto-pilot’s response to suit the
particular installation and the vessel’s steering
characteristics.
Each control has the following functions:
GAIN
Presets the overall system gain to compensate
for variations in the mechanical reduction
between the drive unit and the rudder and the
vessel’s steering characteristics. For initial sea
trial purposes this control is set according to
the recommendations given in Fig.1 8.
PHASE SWITCH
The phase switch is located on the internal
PCB and is accessible by removal of a blank
rubber grommet from the rear case. The phase
switch reverses the direction of
corrective
rudder action and its setting procedure is
described later.
NB Recommended gain control settings for
hydraulic drive installations are given in
the hydraulic drive unit instructions.