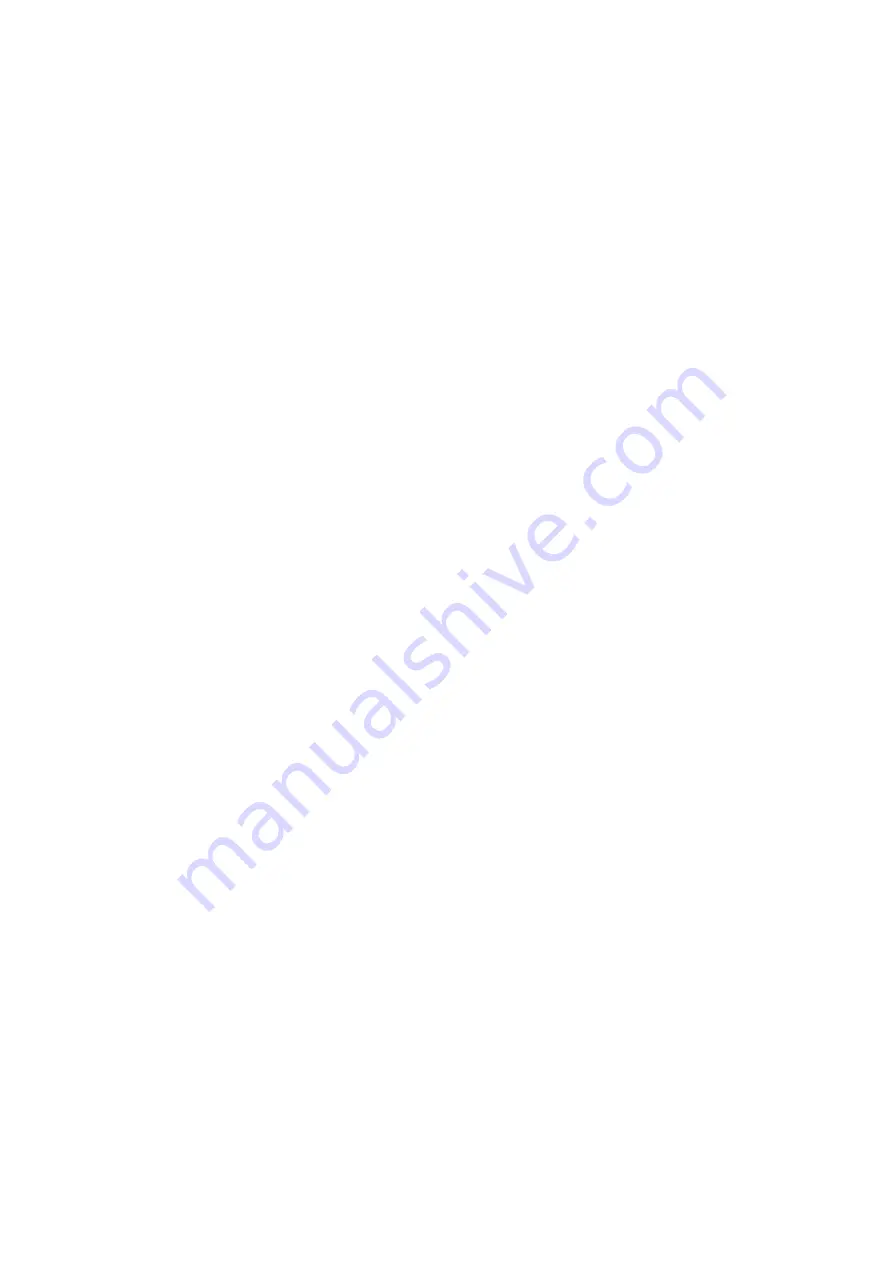
If the chimney is cooled by lack of insulation the difference in weight will also decrease the natu-
ral draught. The cooling of the chimney can vary a lot, amongst other things depending on the
wind
A bad chimney can create the following effects:
1. Pressure fluctuations at start up that create overpressure in the combustion chamber and
possibly exhaust gases and soot in the room and top oven.
2. A smoky flame during the time necessary to heat the chimney until the natural draught has
stabilised.
3. Deterioration of the chimney due to condensation af the water vapour into water and acid
components.
4.
Noise and heat transferring to adjacent rooms.
5. Soot deposits near the chimney and poor distribution of the exhaust gases due to low veloci-
ty (too cool gases in too large a chimney area.
FOR SPECIALIST HELP ON CHIMNEYS OR FLUE PROBLEMS CONTACT THE O.H. HELPLINE.
GOOD SOUND TECHNICAL ADVICE ON CHIMNEY’S AND FLUES CAN ALSO BE OBTAINED FROM
YOUR N.A.C.S. CHIMNEY-SWEEPING TECHNICIAN
OIL STORAGE & SUPPLY ( See BS5410 : Part 1 )
For this appliance the oil tank can be mounted at ground level. Also it can be fitted with the lowest oil
level in the tank 1.3m below the level of the oil pump, over 1.3m a circulator or lift pump is required.The
mild steel oil storage tank should be manufactured to BS 799 Part 5. Plastic oil tanks are covered by
OFTEC standard OFST100. The minimum recommended oil tank size is 1400 litres (300 gallons). Codes
of practice governing installation are covered by BS5410 Part 1.
Should a lift pump be required with the new building regulations and current trends in health and safety it
is recommended that the oil lifter is mounted external to the building.
2..
The pipe line MUST be of a suitable size (10 mm diameter is usually sufficient) to ensure
that maximum flow can be achieved (any other appliance should be accounted for).
3.
A manual isolator valve and oil filter must be fitted directly on the outlet from the oil tank.
4-
10 micron oil filter is fitted in control assembly to prevent small particles entering the burner
assembly.
Fire valves should also be fitted, one according to the instructions to protect the appliance
and a
second mounted external to the building to comply with the new Building Regulations
.
It is recommended that a manual shut off valve be fitted in the same room as the appliance.
On page , a diagram of a layout is shown which would comply with the new regulations and provide a
suitable oil supply to the appliance.
TOOLS REQUIRED - -
1.
Normal fitters tools for dismantling and assembling an Aga or Rayburn.
2. Grinder or powered Sabre saw for modifying the front casting.
3. Drills for broken off bolts, ideally 1/4 & 5/16 Whitworth