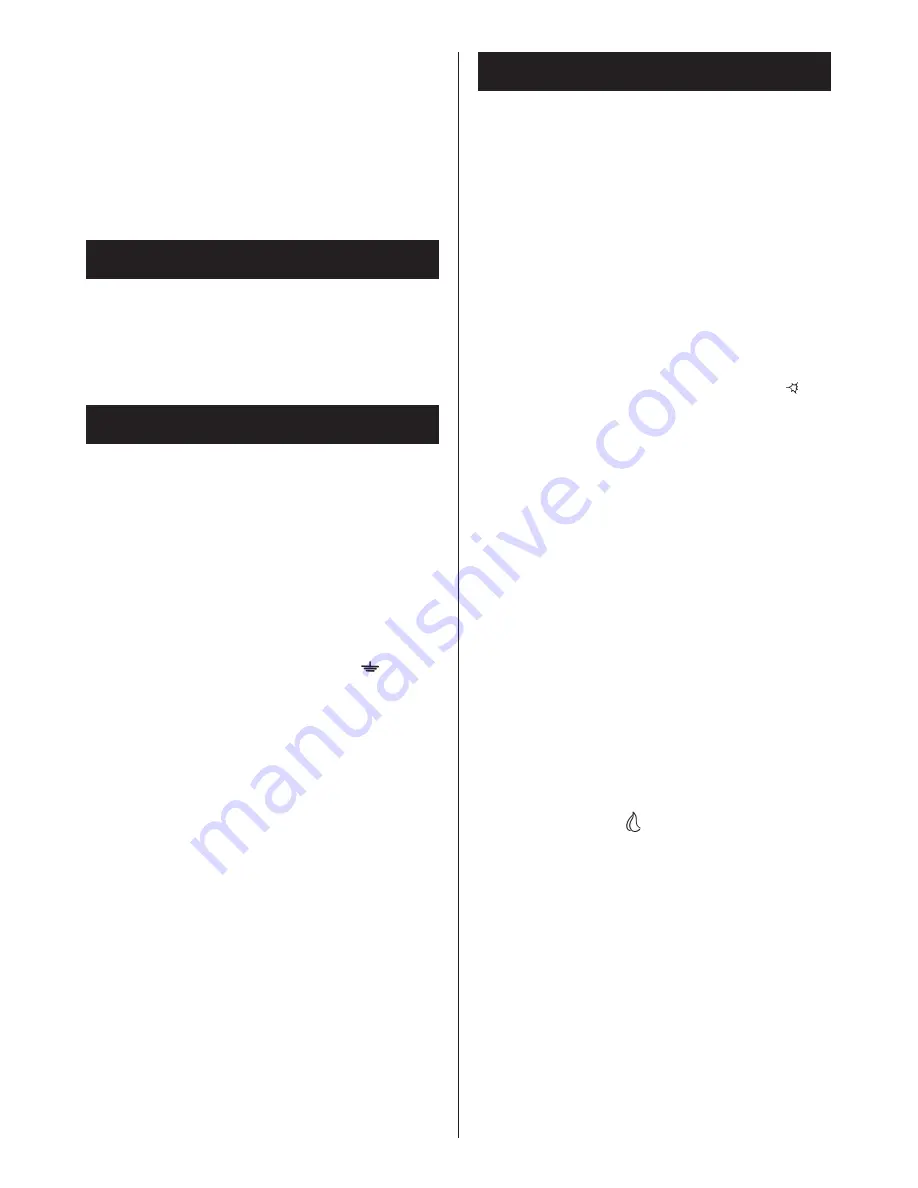
4.
Insulating covers are placed in position and their
chrome hinge spindle inserted and held in position
with the circlips provided.
5.
The handrail brackets are held on the front edge of
the cooker top-plate casting. Remove the travel nuts
and replace with the handrail brackets ensuring the
fibre protecting washers are in position. Insert the
handrail with the fitted endcaps into the brackets,
positioning them correctly, and tighten the locating
bolts.
1.
Connect the gas supply to the pre-formed 15mm
O.D. copper pipe from the integral union gas service
cock on the appliance.
2.
Test the whole of the gas installation, including the
meter for soundness and purge in accordance with
the relevant recommendations.
A 240V ~ 50Hz electrical supply is required near to the
appliance.
The appliance is supplied with a 0.75mm
2
(24x0.2mm) - 3
core PVC x 3 meters long replaceable power supply
cable, which must be connected as described under
“Electricity Supply”.
A label attached to the end of the flexible cable gives
details of the cable core colour coding and their function
which should be adhered to. When connecting to a 3 pin
plug, observe the following recommendations:-
1.
The wire which is coloured green-and-yellow must be
connected to the terminal in the plug which is marked
with the letter E or by the earth symbol or
coloured green or green and yellow.
2.
The wire which is coloured blue must be connected
to the terminal which is marked with the letter N or
coloured black.
3.
The wire which is coloured brown must be connected
to the terminal which is marked with the letter L or
coloured red.
NOTE: IN THE EVENT OF AN ELECTRICAL FAULT
AFTER INSTALLATION OF THE APPLIANCE,
PRELIMINARY SYSTEM CHECKS SHALL BE
CARRIED OUT (e.g. AS DESCRIBED IN THE
MULTIMETER INSTRUCTION BOOK).
IMPORTANT: IF THE PILOT IS EXTINGUISHED FOR
ANY REASON, ALWAYS WAIT AT LEAST 3 MINUTES
BEFORE RE-ATTEMPTING TO RELIGHT.
1.
Switch OFF the electrical supply at the wall socket
and ensure the optional programmer if fitted is
switched to the OFF position.
2.
Ensure that the thermostat knob D is at the LOW
position. Fig. 7.
3.
Open the outer burner door A.
4.
Turn ON the service cock E (below the cooker burner
control valve) so that the screwdriver slot is in line
with pipework.
5.
Turn the control knob B to the ignition symbol and
depress it fully.
6.
Keeping Control Knob B depressed fully
simultaneously press Piezo Spark Generator C
repeatedly until the pilot flame lights. This is visible
through the sight glass F (Fig. 7) (A few seconds must
be allowed for gas to reach the pilot burner).
7.
Continue to hold down Control Knob B for at least 15
seconds after the pilot flame has lit, then release the
knob slowly. The pilot flame will remain alight if its
presence has been detected by the flame sensor unit.
If the flame does not remain alight
wait 3 minutes
and
repeat the sequence holding the control knob B for a
slightly longer time.
8.
Check the leak detection fluid for gas soundness at
the joint of the pilot supply pipe with the control valve.
9.
Check that the pilot flame is enveloping the pilot
thermocouple.
10.
With the thermostat knob D still at its minimum
setting (LOW). TURN the Control Knob B to the large
main flame symbol .
11.
Check that the main burner has lit.
12.
Check that the burner pressure is correct at Test
Nipple G for Low Fire.
13.
Leave at LOW fire for 5 minutes.
14.
Turn thermostat knob D to No. 9, turn ON the
electricity supply, and the programmer if fitted
requires setting to continuous.
15.
Check that the main burner flame has increased from
LOW to HIGH.
16.
Check that the burner pressure is correct for this
setting.
GAS INSTALLATION
ELECTRICAL CONNECTIONS
LIGHTING THE BURNER -
See Fig. 7
5
Содержание 200G/L
Страница 12: ...12 FAULT FINDING ...
Страница 13: ...FAULT FINDING 13 ...
Страница 14: ...14 ...
Страница 15: ...15 ...