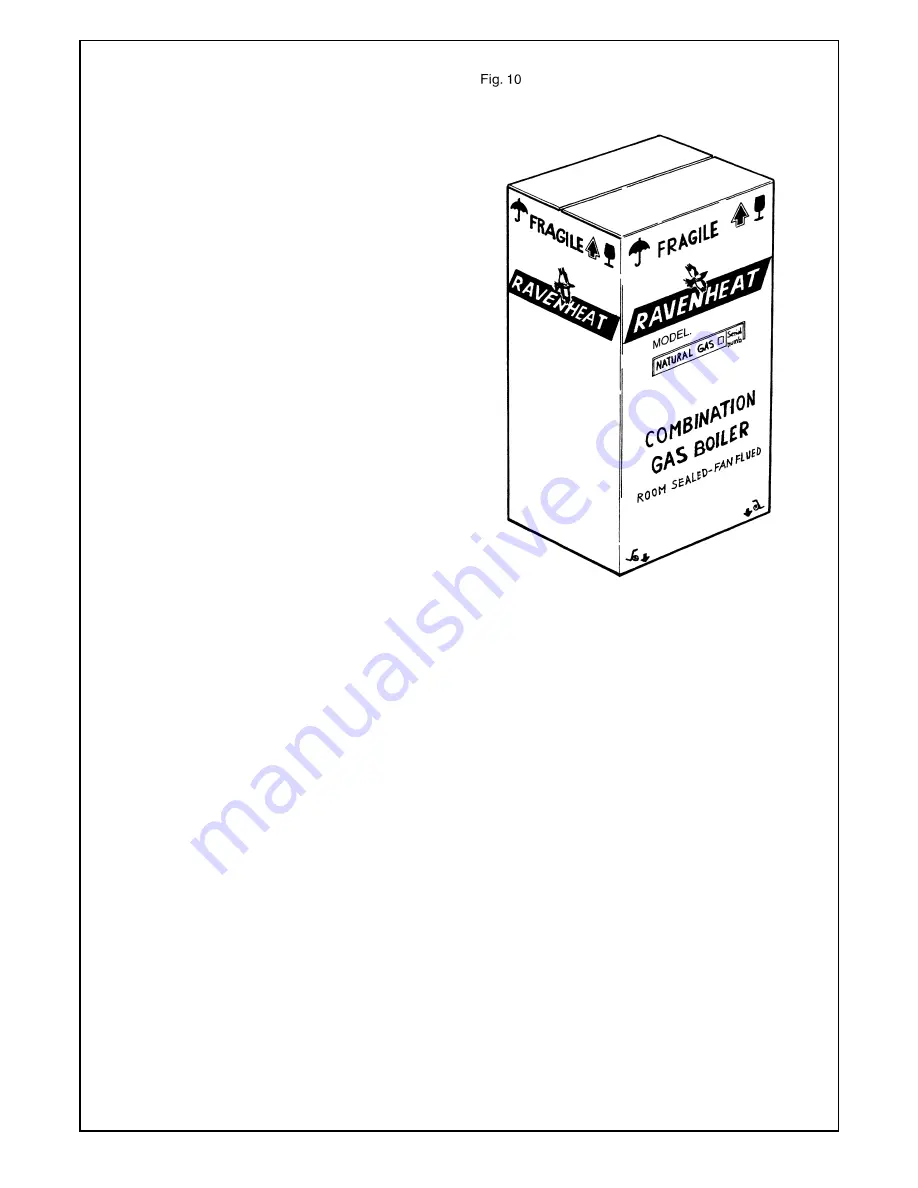
15
SALAMANDER CURROSION GUARD
Salamander (Eng) Ltd
Tel: (0121) 3780952 /4508
4.8.10 Hard water areas
If the area of installation is recognized as hard
water, it is recommended that a suitable water
treatment device is installed in the mains.
The water hardness can be determined by using
the standard test paper or by referring to local
water authority.
4.9 DOMESTIC
WATER
4.9.1
The domestic hot water must be in accordance
with the relevant recommendations of BS 5546.
Copper tubing to BS 2871 1 is recommended
for water carrying pipework and MUST be used
for pipework carrying potable water.
4.10 ELECTRICAL
SUPPLY
Warning: this appliance must be earthed
4.10.1
External wiring to the appliance must be carried
out by a competent person and be in accordance
with the current I.E.E. Regulations and local
regulations which apply. The Ravenheat boiler is
supplied for connection to a 230 V ~ 50 Hz single
phase supply.
The supply must be fused at 3 A.
NOTE. The method of connection to the
electricity supply MUST facilitate complete
electrical isolation of the appliance, by the
use of a fused, double pole isolator, having a
contact separation of at least 3 mm in all poles.
The point of connection to the electricity supply
must be readily accessible and adjacent to
the appliance except, where the appliance is
installed in a bathroom, this MUST be sited
outside the bathroom.
SECTION 5
INSTALLATION
5.1 WARNING
5.1.1
It is MOST IMPORTANT that this appliance is
installed in a VERTICAL POSITION, with the
flue air duct passing through the wall.
Make sure flue slopes 2.5° down towards the
boiler that is 45 mm/m fall per metre of flue
length.
Содержание CSI85A
Страница 1: ...CSI 85 A T ...
Страница 16: ...17 ...
Страница 42: ...43 ...
Страница 43: ...Is fan Running at Maximum speed 44 ...
Страница 44: ...45 ...
Страница 45: ...46 ...
Страница 49: ...15 50 ...
Страница 52: ...COD 0017LIB06006 0 06 2005 ...