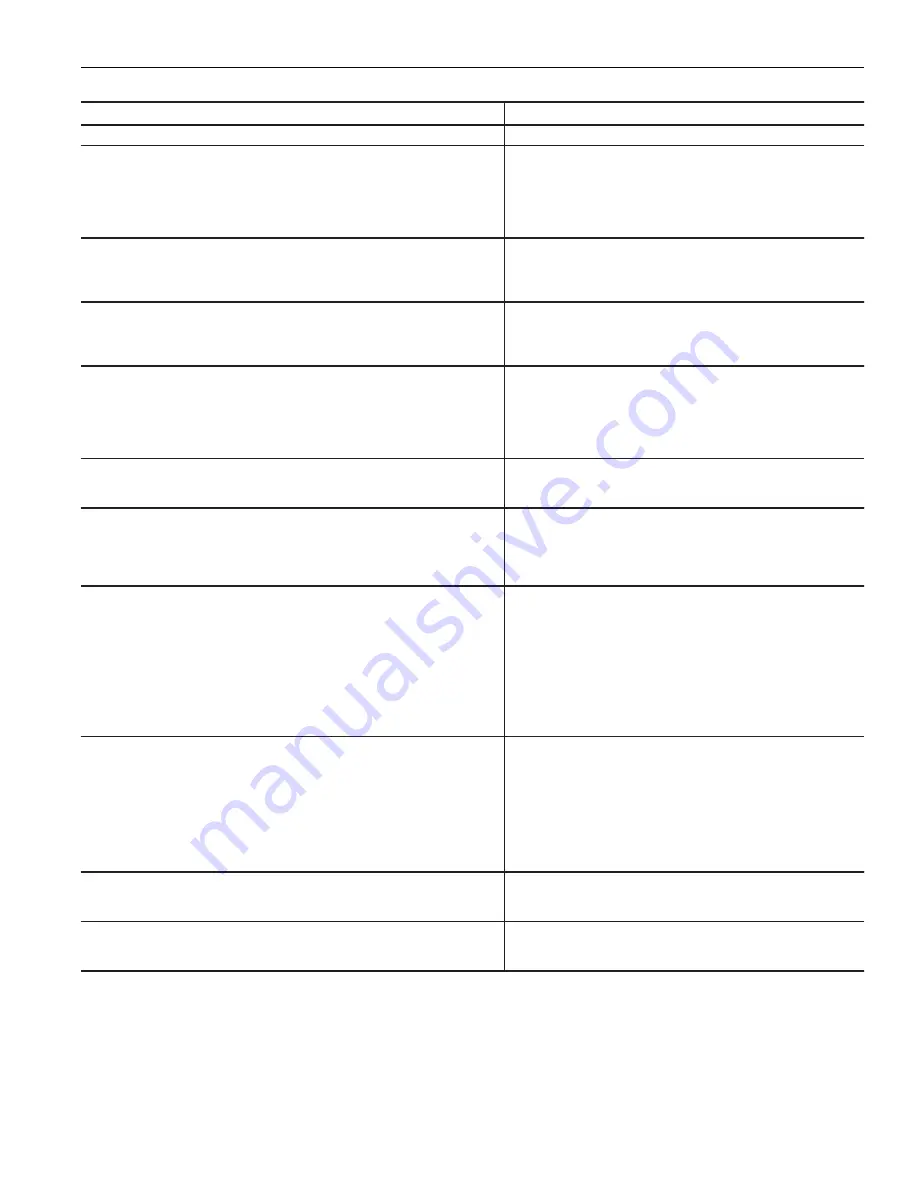
SECTION 24: T
ROUBLESHOOTING
141 of 154
FIELD TEST
REMEDY
1. Arrow on side of Valve should point in direction of gas fl ow.
1. Install properly.
2. Check for 24VAC at amplifi er terminals 7 & 8.
3. Inspect for loose or broken wires between amplifi er terminals 1 & 2, and
TD114 terminals 1 & 2, and TD114 terminals 1 & 3.
4. Connect test resistor as described in Preliminary Circuit Analysis, in Max-
itrol product information sheet. Follow procedure outlined.
5. Check items 2, 3, and 4.
2. Prove the power source.
3. Tighten connections or replace wiring.
4. If modulating voltages are obtained, Check TS114 circuit for sho
Replace TS114 if necessary.
5. If items 2, 3, and 4 check out and modulating voltages are still no
obtained, amplifi er may be assumed faulty. Replace.
6. Measure resistance across modulator terminals with connecting wires
detached.
7. Inspect. Plunger should be installed per diagrams in Maxitrol information
sheet and operate freely in solenoid sleeve.
6. Replace modulator head if not approximately 45-55 ohms for M6
Valve and 60-80 ohms for MR212 Valve.
7. Clean or replace plunger if necessary. Install per Maxitrol produc
information sheet.
8. See valve adjustments in Section 19.5.
9. Measure manifold pressure as outlined in Section 19.4.
8. Adjust to proper minimum fi re.
9. If reading is greater than 1.0 in wc negative pressure, check for
clogged fi lters or other inlet air restrictions. Consult factory for othe
solutions.
10. Inspect for shorts at or between Amplifi er terminals 1 & 2 or TD114 termi-
nals 1 & 3.
11. Check TS114/TS10765 for open internal circuit. Connect test resistor as
described in Preliminary Circuit Analysis, in Maxitrol product information sheet.
Follow procedure outlined.
12. Inspect
10. Correct wiring if shorts exist.
11. If modulating voltages are obtained, check TS114/TS10765 for o
circuits. Replace TS114/TS10765.
12. Correct the wiring.
13. Remove button plate and inspect valve and seat.
14. Inspect. Plunger should be smooth, clean, and operate freely in solenoid
sleeve.
13. Clean seat. Clean valve or replace if necessary.
14. Clean, or if necessary, replace plunger.
15. Read pressure at inlet to modulating valve using a manometer with unit
operating at full fi re. Pressure should be equal to the sum of outlet pressure
setting plus pressure drop of the valve (see Maxitrol capacity chart).
16. Read manifold pressure using manometer and compare with recommen-
dation of equipment manufacturer.
15. Increase inlet pressure if possible.
16. See valve adjustments in Section 19.5.
17. Adjust sensitivity control counter-clockwise.
18. Connect test resistor as described in Preliminary Circuit Analysis, in
Maxitrol product information sheet. Turn TD114 selector dial so heater goes
through its entire modulating range.
19. Temporarily wire each of TD114, TS114, and MR212 externally and ob-
serve heater/equipment operation.
20. With test resistor connected (per item #18) and TD114 locally connected
(per item #19), turn TD114 selector dial through entire modulating range. Ob-
serve D.C. voltage across modulator terminals.
17. If fl ame stabilizes, adjust sensitivity control to maintain an even
fl ame.
18. If the fl ame is steady throughout the entire modulating range, th
TS114 must be moved.
19. If smooth operation results, isolate effected wiring from source
induced voltage.
20. If erratic or unstable DC voltages are obtained throughout the
modulating range, the amplifi er may be assumed faulty. Replace. I
erratic operation is noted only over a small range of 2 or 3 volts, the
age source may contain surges. Consult factory.
21. Inlet Air Sensor changes 1°, for each 3.5°, 5°, or 8° outside temperature
change from 60° (pre-determined - turndown varies with model used).
22. Check wiring diagrams per maxitrol product.*
23. Sensed temperature (thermometer next to TS114) does not correspond to
TD114 setting.
24. Sensed temperature (thermometer next to TS114) does not represent
average discharge air temperature.
25. Remove Override Thermostat lead from terminal 2 of TD114.
*information sheet
21. Sensed temperature will vary from TD114 dial settings. This is
intentional.
22. Correct wiring.
23. See calibration procedure.
24. Move TS114 to location where average representative temperat
can be sensed.
25. TD114 dial setting, then check thermostat setting and/or check
ing for shorts.
26. Measure resistance across modulator terminals with red lead wires
disconnected.
27. Inspect wiring.
26. Replace modulator head if less than 40 ohms.
27. Correct wiring if short is found.
28. Check “Override Temperature Selector” of TD114.
29. Check for high fi re (Maximum manifold pressure specifi ed for heater).
28. Reset to correct temperature.
29. If on high fi re, control can do no more. Heater unable to furnish
ditional heat to raise temperature.
Содержание 4044
Страница 2: ......
Страница 4: ......
Страница 6: ......
Страница 8: ......
Страница 48: ...4000 SERIES INSTALLATION OPERATION AND SERVICE MANUAL 40 of 154 FIGURE 30 Evaporative Cooling Trap Detail...
Страница 73: ...SECTION15 VIBRATION ISOLATION 65 of 154 FIGURE 52 Curb Mounted Roof Curb Roof Curb...
Страница 108: ...4000 SERIES INSTALLATION OPERATION AND SERVICE MANUAL 100 of 154 19 15 Honeywell RM7890 Flame Safeguard...
Страница 109: ...SECTION19 ELECTRICAL 101 of 154...
Страница 110: ...4000 SERIES INSTALLATION OPERATION AND SERVICE MANUAL 102 of 154...
Страница 111: ...SECTION19 ELECTRICAL 103 of 154...
Страница 112: ...4000 SERIES INSTALLATION OPERATION AND SERVICE MANUAL 104 of 154...
Страница 113: ...SECTION19 ELECTRICAL 105 of 154...
Страница 114: ...4000 SERIES INSTALLATION OPERATION AND SERVICE MANUAL 106 of 154...
Страница 115: ...SECTION19 ELECTRICAL 107 of 154...
Страница 116: ...4000 SERIES INSTALLATION OPERATION AND SERVICE MANUAL 108 of 154...
Страница 117: ...SECTION19 ELECTRICAL 109 of 154...
Страница 118: ...4000 SERIES INSTALLATION OPERATION AND SERVICE MANUAL 110 of 154...
Страница 119: ...SECTION19 ELECTRICAL 111 of 154...
Страница 121: ...SECTION 20 DIRECT FIRED BURNER 113 of 154 FIGURE 71 Midco HMA 2A Burner...
Страница 122: ...4000 SERIES INSTALLATION OPERATION AND SERVICE MANUAL 114 of 154...
Страница 125: ...SECTION 20 DIRECT FIRED BURNER 117 of 154...
Страница 126: ...4000 SERIES INSTALLATION OPERATION AND SERVICE MANUAL 118 of 154...
Страница 127: ...SECTION 20 DIRECT FIRED BURNER 119 of 154 20 3 Honeywell UV Flame Detector...
Страница 128: ...4000 SERIES INSTALLATION OPERATION AND SERVICE MANUAL 120 of 154 20 4 Honeywell UV Flame Detector Continued...
Страница 160: ...4000 SERIES INSTALLATION OPERATION AND SERVICE MANUAL 152 of 154...
Страница 161: ...SECTION 27 THE RAPID 4000 SERIES WARRANTY 153 of 154...
Страница 162: ...4000 SERIES INSTALLATION OPERATION AND SERVICE MANUAL 154 of 154...