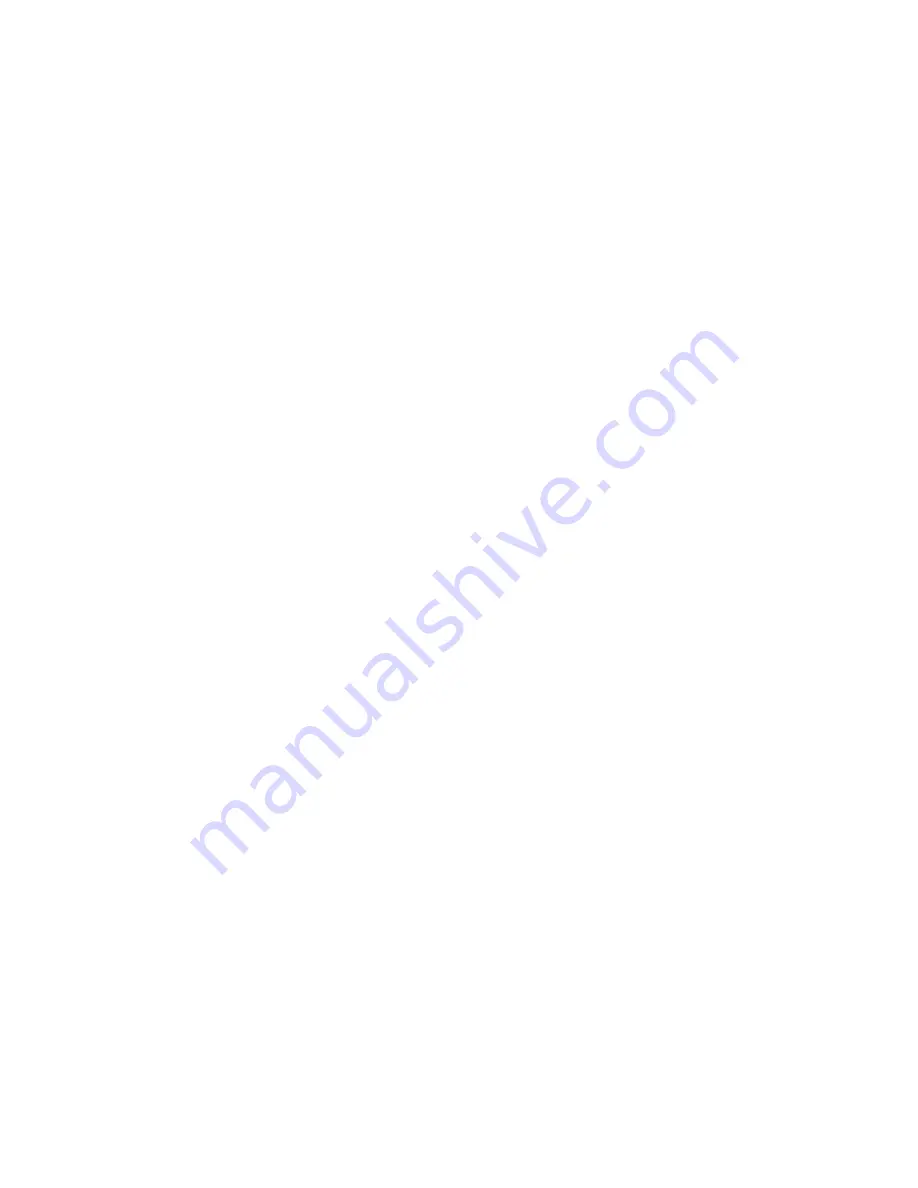
United States installations only:
Randell will pay for the replacement compressor only. Freight, labor, refrigerant, handling
and all other miscellaneous charges are the responsibility of the customer. Randell will
fulfill its warranty obligation by using one of the four methods provided below, which will be
selected by the Randell in house service technician:
1. Provide reimbursement to servicing customer for the cost of the locally obtained replace-
ment compressor in exchange for the return of the defective compressor returned to
Randell freight prepaid. Randell does limit the amount of reimbursement allowed and
does require a copy of the local supply house bill for replacement compressor.
Customer should not pay servicing agent up front for compressor.
2. Provide repair at the manufacturing facility by requiring that the defective unit be sent
back to Randell freight prepaid. Perform repair at the expense of Randell and ship the
item back to job location freight collect.
3. Furnish a replacement compressor freight collect in exchange for the return of the defec-
tive compressor sent back freight prepaid.
4. Furnish complete condensing unit or replacement package freight collect in exchange for
the return of the defective compressor sent back freight prepaid. (decisions based on
whether or not to send complete condensing unit will be made by Randell in-house
service technician).
Export Warranty
Our export warranties will cover all non electrical parts for the period of one year from the
date of shipment to be free of defects in material or workmanship. Electrical parts are also
covered if ordered and operated on 60 Hz. Electrical components, ordered and operated
on 50 Hz, are warranted for the first 90 days from shipment only. Service labor is covered
for the first 90 days with authorization from factory prior to service. Warranty is automati-
cally initiated 60 days from ship date. Inbound costs on any factory supplied items would be
the responsibility of the customer. Adherence to recommended equipment maintenance
procedures, according to the owners manual provided with each unit, is required for this
warranty to remain in effect, and can have a substantial effect on extending the service life
of your equipment. Equipment abuse voids any warranty. Extended warranties are not
available for parts, labor or compressors on units shipped outside the United States.
Freight Damage
Any and all freight damage that occurs to a Randell piece of equipment as a result of
carrier handling is not considered warranty, and is not covered under warranty guidelines.
Any freight damage incurred during shipping needs to have a freight claim filed by the
receiver with the shipping carrier (note all damages on freight bill at time of delivery). Inter-
nal or concealed damage may fall under Randell’s responsibility dependent upon the cir-
cumstances surrounding each specific incident and are at the discretion of the Randell in-
house service technician.
Содержание 2010FMJB
Страница 16: ...EASY TO FOLLOW TROUBLE SHOOTING CHART...
Страница 19: ...PARTS LIST FOR 2010FMJB...
Страница 20: ......
Страница 21: ......
Страница 22: ......
Страница 23: ......
Страница 24: ......