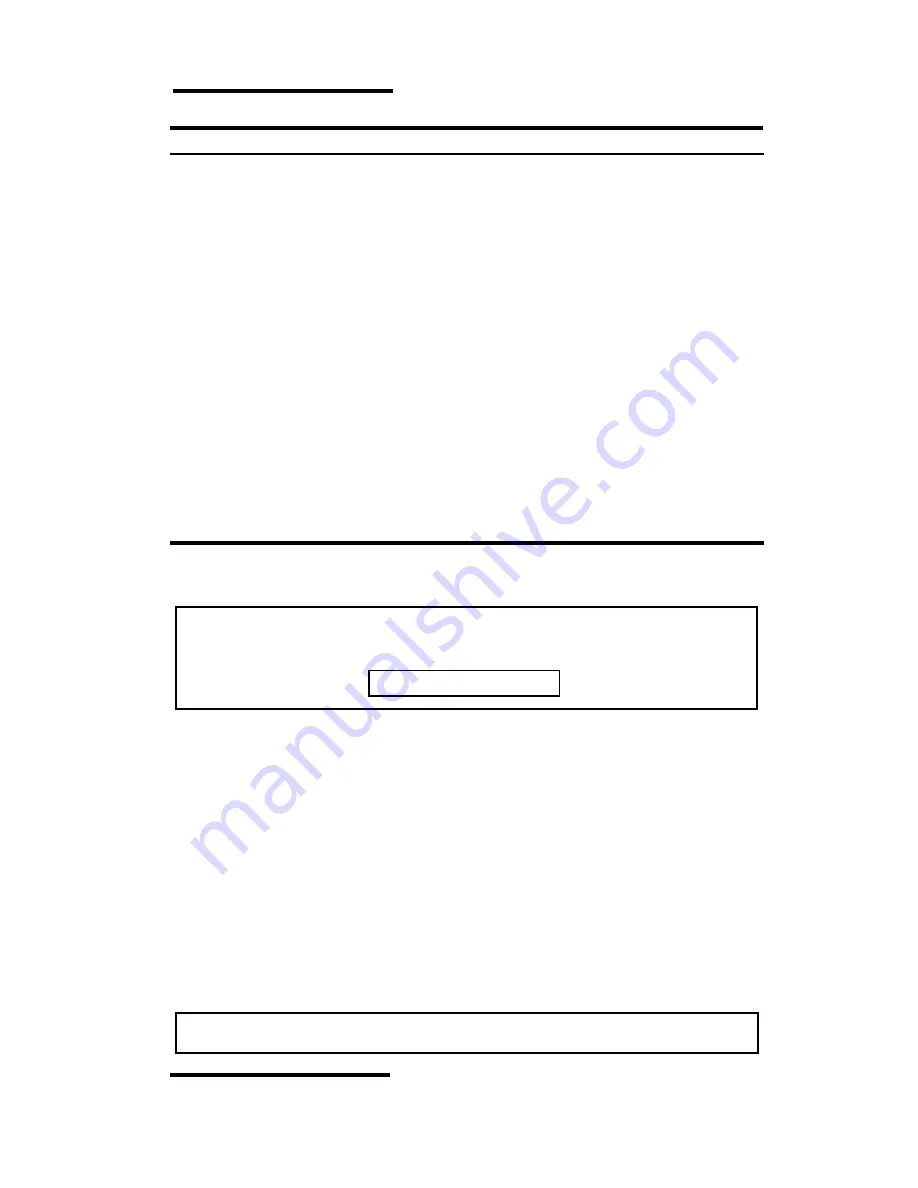
PARTS LISTING / MAINTENANCE
PARTS LISTING / MAINTENANCE
13
COBRA TOOL PARTS LIST
KEY
PART NO.
DESCRIPTION
1
SC301500
SPALL GUARD
2
SC301009
FRONT BARREL (BASEPLATE )
3
SC301011A
SHEAR CLIP (PKG. OF 3)
4
SC301010
FASTENER GUIDE
5
SC301200A
PISTON ASSEMBLY
6
SC301208
PISTON RING
7
SC302012
PAWL ( STOP )
8
SC301006
REAR BARREL ( PISTON SLEEVE )
9
SC301014A
BARREL RETENTION ASSEMBLY
10
SC301016
PUSH PIN
11
SC301046A
DETENT BALL ASSEMBLY
12
SC301034A
TRIGGER ASSEMBLY AND PIN
13
SC301001
TOOL BODY
14
SC301113
BOLT ( 2 )
15
SC301300A
SEAR HOLDER ASSEMBLY
16
SC301531
SPRING, ADVANCE BAR
17
SC301400
FIRING PIN ASSEMBLY
18
SC301026A
FIRING PIN SPRING ASSEMBLY
19
SC301600
HANDLE ASSEMBLY
MAINTENANCE
IMPROPERLY MAINTAINED TOOLS CAN CAUSE SEROIUS INJURIES
TO TOOL OPERATORS AND BYSTANDERS
CLEAN TOOL DAILY
Always make sure the tool is not loaded before performing any service or
repair and always wear safety goggles when cleaning or servicing the tool.
NORMAL CLEANING
All front end parts shown in the disassembly section are to be cleaned daily with a
good detergent oil and wire brush. Remove all dirt and carbon buildup and wipe
parts dry with a clean rag. Check all parts for wear or damage before reassembly
and replace or repair any worn or damaged parts.
COMPLETE CLEANING / GENERAL MAINTENANCE
Heavy use or constant exposure to dirt and debris may require that the tool be
cleaned more extensively. Complete disassembly and cleaning of all parts may be
necessary to restore the tool to normal operation. General maintenance should be
performed every six months or more often if the tool is subjected to heavy use.
Contact your authorized Ramset Distributor for assistance.
ALWAYS FUNCTION TEST THE TOOL AFTER PERFORMING ANY SERVICE.
SEE PAGE 9 FOR DETAILS ON THE FUNCTION TEST.