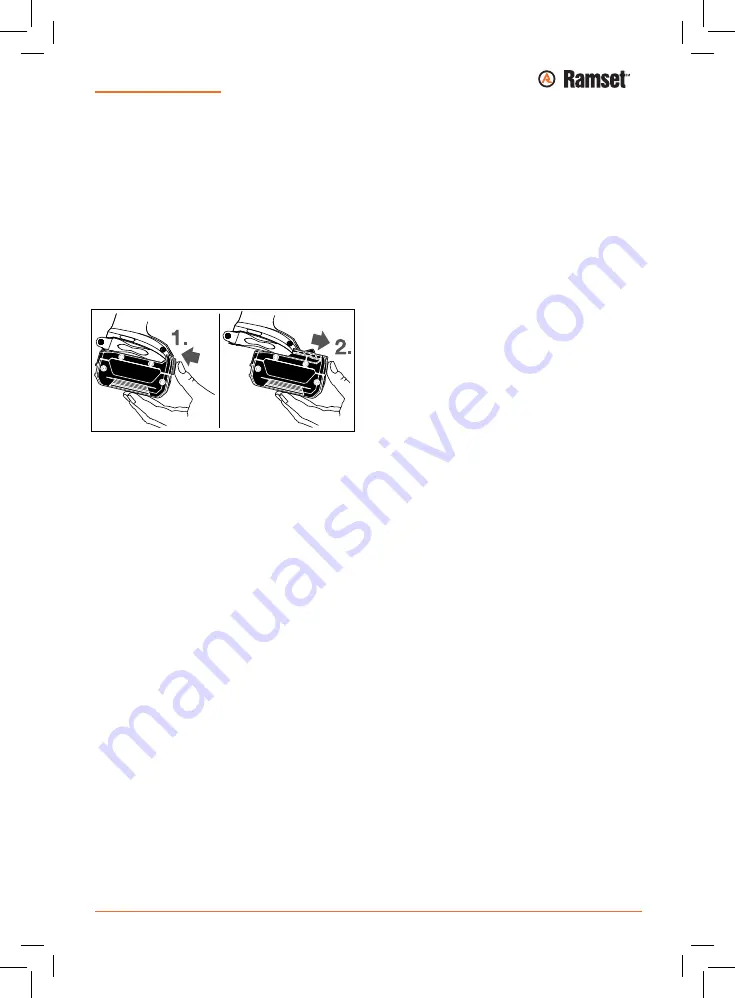
Impact Driver/Wrench 18V
Owners Manual
- 08 -
English |
17
Bosch Power Tools
1 609 92A 2CU | (2.11.16)
The lithium ion battery is protected against deep discharging
by the “Electronic Cell Protection (ECP)”. When the battery is
empty, the machine is switched off by means of a protective
circuit: The inserted tool no longer rotates.
Do not continue to press the On/Off switch after the
machine has been automatically switched off.
The bat-
tery can be damaged.
Observe the notes for disposal.
Removing the battery
The battery
4
is equipped with two locking levels that should
prevent the battery from falling out when pushing the battery
unlocking button
5
unintentionally. As long as the battery is
inserted in the power tool, it is held in position by means of a
spring.
To remove the battery
4
, press the unlocking button
5
and
pull out the battery toward the front.
Do not exert any force.
Changing the Tool
Before any work on the machine itself (e. g. mainte-
nance, tool change, etc.) as well as during transport
and storage, remove the battery from the power tool.
There is danger of injury when unintentionally actuating
the On/Off switch.
Regularly clean the power tool’s air vents.
The motor’s
fan will draw the dust inside the housing and excessive ac-
cumulation of powdered metal may cause electrical haz-
ards.
Inserting
Pull the locking sleeve
2
forward, push the insert tool to the
stop into the tool holder
1
and release the locking sleeve
2
to
lock the insert tool.
Screwdriver bits
16
can be inserted using a universal bit hold-
er with ball lock
15
.
Removing
Pull the locking sleeve
2
forward and remove the insert tool.
When working with an application tool, pay attention
that the application tool is connected securely on the
tool holder.
When the application tool is not securely con-
nected with the tool holder, it can come off during applica-
tion.
Slide the application tool
17
onto the square drive of the tool
holder
1
.
However based on the system, if the application tool
17
ap-
pears wobbly after connecting securely on the tool holder
1
;
this has no influence on the function/safety.
Some application tools (e.
g. double bits) cannot be safely se-
cured in the tool holder.
Operation
Method of Operation
The tool holder
1
with the tool is driven by an electric motor
via a gear and impact mechanism.
The working procedure is divided into two phases:
Screwing in
and
tightening
(impact mechanism in action).
The impact mechanism is activated as soon as the screwed
connection runs tight and thus load is put on the motor. In this
instance, the impact mechanism converts the power of the
motor to steady rotary impacts. When loosening screws or
nuts, the process is reversed.
Starting Operation
Inserting the battery
Use only original
Ramset
lithium ion batteries with the
voltage listed on the nameplate of your power tool.
Us-
ing other batteries can lead to injuries and pose a fire haz-
ard.
Set the rotational direction switch
9
to the centre position to
protect the power tool against accidental starting.
Insert the charged battery
4
from the front into the base of the
power tool until the battery is securely locked.
Reversing the rotational direction (see figure D)
The rotational direction switch
9
is used to reverse the rota-
tional direction of the machine. However, this is not possible
with the On/Off switch
10
actuated.
Right rotation:
For driving in screws and tightening nuts,
press the rotational direction switch
9
through to the left
stop.
Left Rotation:
For loosening and unscrewing screws and
nuts, press the rotational direction switch
9
through to the
right stop.
Switching On and Off
To
start
the machine, press the On/Off switch
10
and keep it
pressed.
To
switch off
the machine, release the On/Off switch
10
.
To save energy, only switch the power tool on when using it.
Adjusting the Speed
The speed of the switched on power tool can be variably ad-
justed, depending on how far the On/Off switch
10
is
pressed.
Light pressure on the On/Off switch
10
results in a low rota-
tional speed. Further pressure on the switch results in an in-
crease in speed.
OBJ_BUCH-2047-002.book Page 17 Wednesday, November 2, 2016 3:55 PM
18
| English
1 609 92A 2CU | (2.11.16)
Bosch Power Tools
Preselecting the Speed/Impact Frequency
With the button
6
you can preselect the required speed/im-
pact rate in three stages. Press the button
6
repeatedly until
the desired setting appears in the speed indicator
7
. The se-
lected setting will be saved.
The required speed/impact frequency depends on the mate-
rial and the working conditions, and can be determined
through practical testing.
Switching the “PowerLight” On/Off
To switch the “PowerLight”
11
on
, press button
8
. To switch
the “PowerLight”
11
off
, press button
8
again.
Working Advice
Apply the power tool to the screw/nut only when it is
switched off.
Rotating tool inserts can slip off.
The torque depends on the impact duration. The maximum
achieved torque results from the sum of all individual torques
achieved through impact. The maximum torque is achieved
after an impact duration of 6–10 seconds. After this dura-
tion, the tightening torque is increased only minimally.
The impact duration is to be determined for each required
tightening torque. The actually achieved tightening torque is
always to be checked with a torque wrench.
Screw Applications with Hard, Spring-loaded or Soft Seat
When in a test, the achieved torques in an impact series are
measured and transferred into a diagram, resulting in the
curve of a torque characteristic. The height of the curve corre-
sponds with the maximum reachable torque, and the steep-
ness indicates the duration in which this is achieved.
A torque gradient depends on the following factors:
– Strength properties of the screws/nuts
– Type of backing (washer, disc spring, seal)
– Strength properties of the material being screwed/bolted
together
– Lubrication conditions at the screw/bolt connection
The following application cases result accordingly:
– A
hard seat
is given for metal-to-metal screw applications
with the use of washers. After a relatively short impact du-
ration, the maximum torque is reached (steep characteris-
tic curve). Unnecessary long impact duration only causes
damage to the machine.
– A
spring-loaded seat
is given for metal-to-metal screw ap-
plications, however with the use of spring washers, disc
springs, studs or screws/nuts with conical seat as well as
when using extensions.
– A
soft seat
is given for screw applications, e. g., metal on
wood or when using lead washers or fibre washers as back-
ing.
For a spring-loaded seat as well as for a soft seat, the maxi-
mum tightening torque is lower than for a hard seat. Also, a
clearly longer impact duration is required.
Reference Values for Maximum Screw/Bolt Tightening Torques
Calculated from the tensional cross-section; utilization of the yield point 90 % (with friction coefficient μ
total
= 0.12). As a control
measure, always check the tightening torque with a torque wrench.
Tips
Before screwing larger, longer screws into hard materials, it is
advisable to predrill a pilot hole with the core diameter of the
thread to approx.
2
/
3
of the screw length.
Note:
Pay attention that no metal particles enter the power
tool.
Belt Clip
With the belt clip
3
, the machine can be hung onto a belt. The
user has both hands free and the machine is always at hand.
Recommendations for Optimal Handling of the Battery
Protect the battery against moisture and water.
Store the battery only within a temperature range between
0 °C and 50 °C. As an example, do not leave the battery in the
car in summer.
Occasionally clean the venting slots of the battery using a soft,
clean and dry brush.
A significantly reduced working period after charging indi-
cates that the battery is used and must be replaced.
Observe the notes for disposal.
Maintenance and Service
Maintenance and Cleaning
Before any work on the machine itself (e. g. mainte-
nance, tool change, etc.) as well as during transport
and storage, remove the battery from the power tool.
There is danger of injury when unintentionally actuating
the On/Off switch.
Property Classes accord-
ing to DIN 267
Standard Screws/Bolts
High-strength Bolts
3.6
4.6
5.6
4.8
6.6
5.8
6.8
6.9
8.8
10.9
12.9
M 6
2.71
3.61
4.52
4.8
5.42
6.02
7.22
8.13
9.7
13.6
16.2
M 8
6.57
8.7
11
11.6
13.1
14.6
17.5
19.7
23
33
39
M 10
13
17.5
22
23
26
29
35
39
47
65
78
M 12
22.6
30
37.6
40
45
50
60
67
80
113
135
M 14
36
48
60
65
72
79
95
107
130
180
215
M 16
55
73
92
98
110
122
147
165
196
275
330
OBJ_BUCH-2047-002.book Page 18 Wednesday, November 2, 2016 3:55 PM