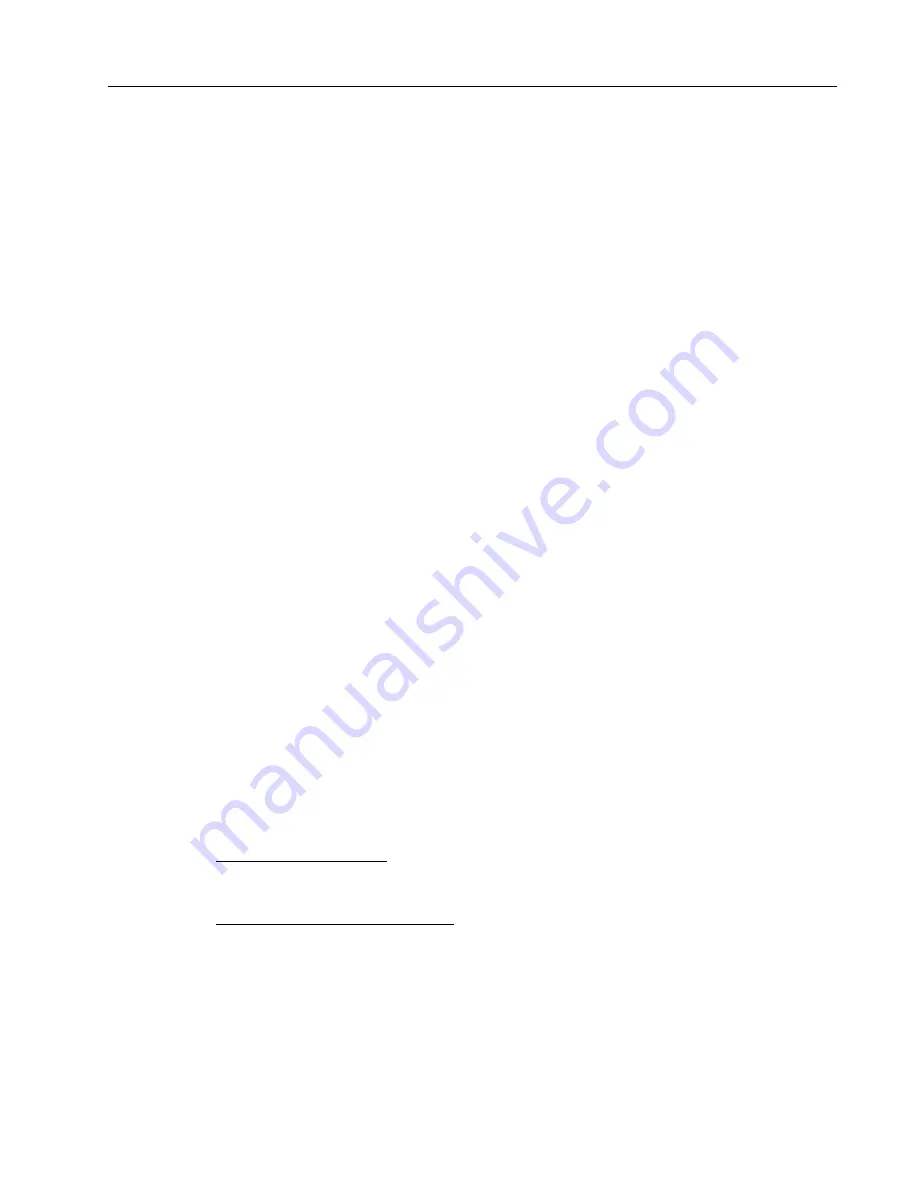
RAM DBS II
Refrigeration Solid State Starter
1.0 Description
1.1
Overview
The DBS (digital bypass solid state) reduced-voltage starter is a microprocessor controlled motor
starting device which utilizes six SCRs (silicon controlled rectifiers) to electronically reduce the
applied voltage to an AC induction motor, allowing the motor to start at a reduced current. Because
the DBS accelerates the motor in a smooth stepless manner, it reduces drop in the supply voltage as
well as mechanical shock on the driven equipment, that is normally experienced with two-step,
electromechanical, reduced-voltage starting methods.
The DBS can be programmed to provide a gradual build up of torque, from zero to almost full motor
locked rotor torque, or to limit starting currents to a constant value, which prevents an excessive
voltage drop during motor starting.
1.2
Standard Features
Universal Source Matching:
The DBS automatically adjusts itself to any input voltage between 200
and 600 VAC and any frequency from 45 to 65 Hz.
Closed Loop Starting:
The DBS starts a motor in a continuous controlled current mode, which
eliminates mechanical shock to the motor.
Automatic Bypass:
The DBS includes a bypass contactor that is automatically engaged after the
motor has reached full speed, or when the bypass delay has expired. The bypass contactor reduces
power losses and heat build-up so that the DBS controller, in an unventilated enclosure in a 40
o
C
ambient, can continuously operate a fully-loaded motor.
Electronic Motor Overload Protection:
The DBS has integral electronic motor protection. This
micro-processor-based feature provides comprehensive motor overload protection as well as
monitoring and annunciating system alarm and shutdown conditions. See Section 1.7 for full
explanation of motor overload protection features.
LED Diagnostics:
The DBS has four LEDs provided on the front of its control board to indicate the
operating state of the DBS.
Motor Connection:
No special motor is required. Any standard 3-phase motor can be connected to the
DBS. See Figure 10 in the Appendix for typical 3-wire connection diagrams.
Starting Modes:
Two starting modes provide optimum performance to match the DBS to the motor load
characteristics:
a.
Constant Current Mode:
Starting current is limited to a maximum level, adjustable from
200-425% of FLA, until the motor attains full speed. This mode is recommended for light to
moderate inertial-type loads. See Figure 6, Section 5.
b.
Step Ramp (Current Ramp) Mode:
After the starting current quickly reaches the current
step limit, it can ramp up to 500% FLA. The ramp time allowed can be set from 3-30 seconds.
This mode is recommended for heavy inertial and friction-type loads. See Figure 7,
Section 5.
Control:
A programmer/display unit (KL4) is mounted in the door of the controller's enclosure. The
motor's operating conditions are displayed and motor specifications and operating parameters are
programmed though the KL4.
UL and CUL Approved:
All models have been tested and approved by Underwriters Laboratory per
UL 508 Standard, and conform to Canadian National standards.
1
1.0 Description
StockCheck.com