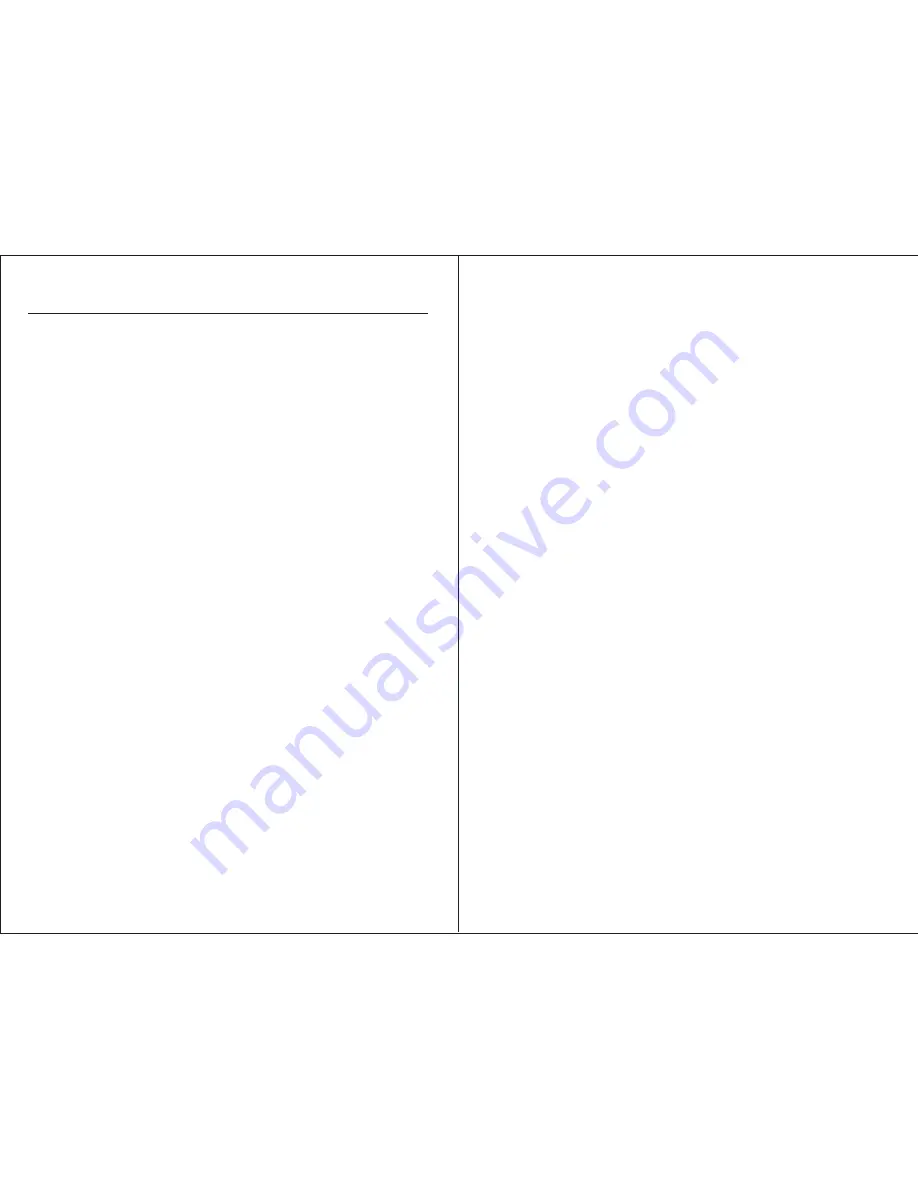
-7-
Helpful hints that can extend the life of your air tools
• Oil tools daily. If the oil that comes out of the exhaust port looks dirty, repeat the oiling
process until the oil ejected runs clear. Lubricating the tool after each use will assist in
maintaining your tool during storage. This is because water, dirt and any foreign
substances that get left for any period of time will rust and corrode the air motor and
bearings.
• Make sure the tool has an operating pressure of 90 PSI when running. Too long,
small or restricted air lines can cause a significant loss of air pressure which will cause the
tool to work harder, eventually causing the tool to wear out or break prematurely.
Most tool failures are caused by one or more of the following:
• Lack of lubrication
• Too much or too little air pressure
• Dirt, rust or water in air lines
• Throwing, dragging or dropping the tool
• Incorrect hose or coupler size
• Incorrect tool for screw size
Use the right tool for the job.
Use the following guide for bolt size to be fastened:
¼" drive tools, maximum screw size ¼"
⅜" drive tools, maximum screw size ½"
½" drive tools, maximum screw size ⅝"
¾" drive tools, maximum screw size 1"
1" drive tools, maximum screw size 1 ½"