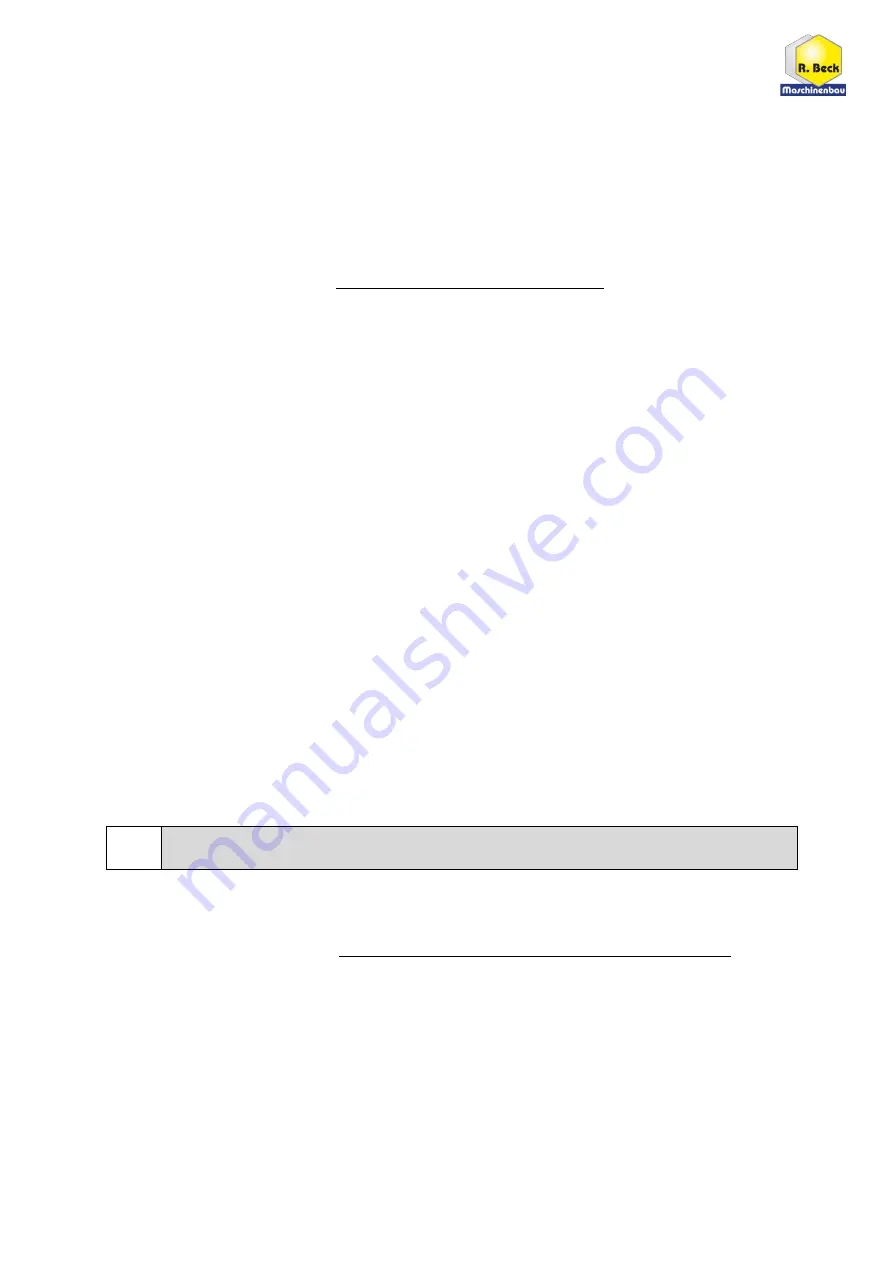
21
BA_BM_EXAKT-ELG-DC_EN_37-23.docx
8.4
Transport to the place of use
After unpacking, the roller conveyor can be moved to the installation site using a lift truck. When doing so, the
general safety regulations must be followed and observed. For procedure refer to section
8.5
Requirements for the installation site
The following guidelines apply with regard to space requirements, load-bearing capacity and the condition of
the substrate:
•
Space requirements: L x H x W = Length according to customer requirements x 1800 x 700 mm
•
Load capacity:
Concrete of classification B 15
•
Conditions:
Level, smooth, non-slip and tilt-free
8.6
Temporary storage
If the roller & measuring conveyor is not put into operation immediately after delivery, it must be stored carefully
in a protected place. Carefully cover the entire roller & measuring conveyor so that neither dust nor moisture
can penetrate.
8.6.1
Short term storage
•
Dry environment
•
Protect components at risk of corrosion
•
Park in a stable place
8.6.2
Long term storage
•
Dry environment
•
Protect components at risk of corrosion
•
Protect roller & measuring conveyor from dirt
•
Park in a stable place
•
Dismantle roller & measuring conveyor into individual segments if required
8.7
Lashing on a transport vehicle
For further transport, the roller conveyor must be lashed to the loading area of the transport vehicle on a pallet.
For this purpose, a sufficient number of lashing straps with the appropriate load-bearing capacity must be used.
The responsibility for safe loading is borne by the respective shipper!
Please note the following when lashing in the transport vehicle:
•
The loading area of the transport vehicle must always be clean and dry.
•
The lashing straps used and their number must be suitable for the total weight of the roller & measuring con-
veyor and distributed accordingly. The weight is approx. 100 kg per meter of roller conveyor length.
•
Loose and moving parts must be secured against slipping or packed in separate boxes if necessary.
•
Fastening on the loading area is done by lashing down: This means that the transport pallet is secured by
frictional locking. The load is pressed so firmly onto the loading surface that it can no longer slip. The clamp-
ing tool should have a high STF value at the frictional connection, e.g. long-lever ratchets.
•
In addition, anti-slip mats should be used to provide even more safety.
•
The ideal lashing angle (α) for tie
-down lashing is 83° to and 90°. Therefore, the lashing straps should pull
downwards approx. vertically. As the angle decreases, the pretensioning force of the lashing is reduced.
•
Observe the permissible total weight of the transport vehicle.
•
Ensure that the permissible axle loads of the transport vehicle are observed. The load must be distributed
evenly on all axles of the vehicle.
A separate lashing strap must be used for each lashing and must be tensioned individually on the
floor of the loading area of the vehicle! The pallet must also be secured against slipping.