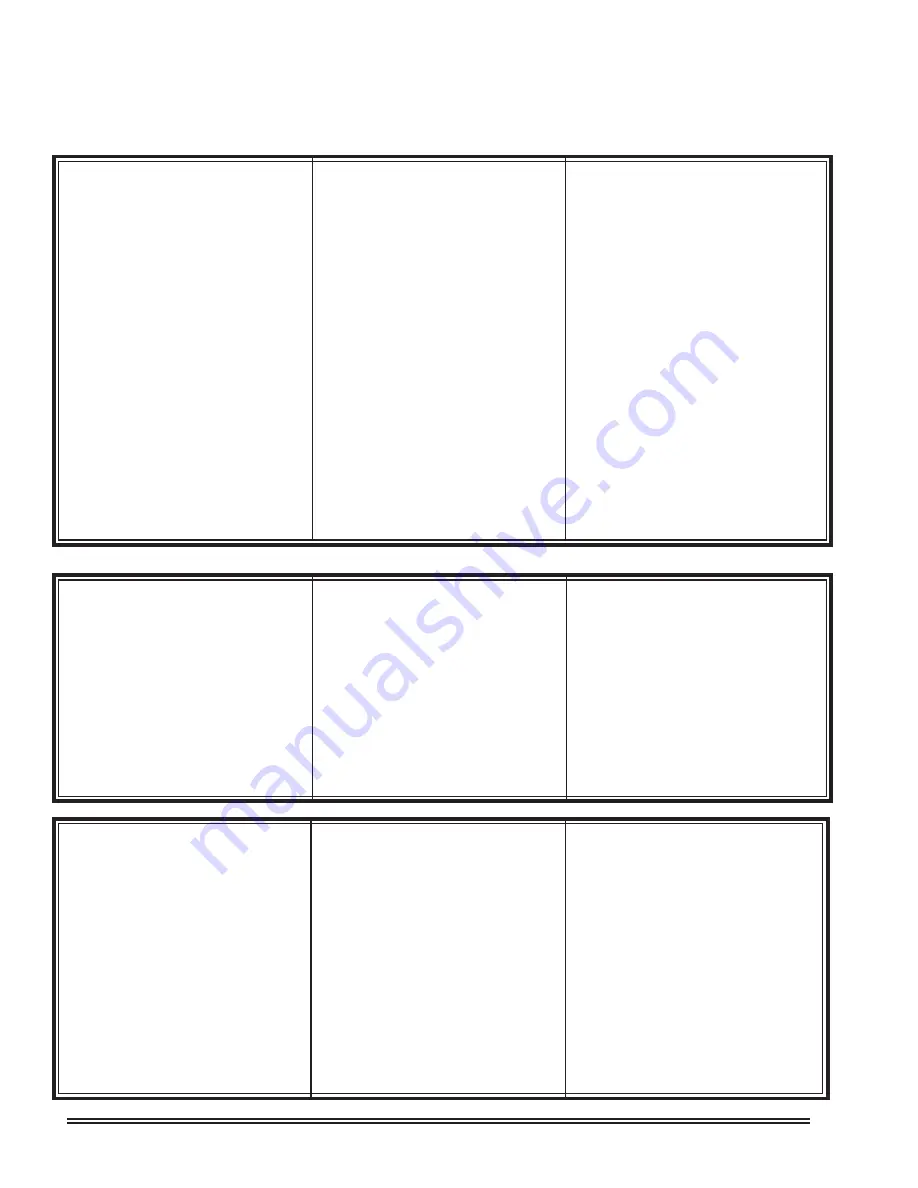
Quincy Compressor
1312100602, September 2012
9
3501 Wisman Lane, Quincy IL - 62305-3116
1. Use additional hose instead
of extra extension cord or use
heavier gauge extension cord.
2. Repair electrical connections.
3. Check with voltmeter.
4. Replace with correctly sized
motor.
5. Replace motor.
6. Change power cord & voltage
of motor to match voltage of
power source.
3. Fuses blow or circuit breakers
trip.
2. Motor hums or runs slowly
when first turned on.
1. Light duty extension cord be-
ing used.
2. Loose electrical connection.
3. Low voltage.
4. Motor sized incorrectly.
5. Defective motor.
6. Motor voltage does not match
voltage of power source.
1. Loose electrical connection.
2. Too many lights or appliances
being operated on the same
circuit as the compressor (cir-
cuit overloaded).
3. Defective check valve or un-
loader.
4. Low voltage.
5. Motor sized incorrectly.
6. Incorrect size fuse or circuit
breaker.
7. Defective motor.
8. Motor voltage does not match
voltage of power source.
1. Repair electrical connections.
2. Try another circuit or remove
other appliances from circuit
being used.
3. Replace check valve or un-
loader.
4. Check with voltmeter.
5. Replace with correctly sized
motor.
6. Check for proper size fuse.
7. Replace motor.
8. Change power cord & voltage
of motor to match voltage of
power source.
PROBLEM
CAUSES
CORRECTION
1. Plug power cord in.
2. Switch to “auto”.
3. Turn OFF/AUTO switch to
the “OFF” po sition. Push the
motor thermal over load (red)
button firmly until a click is
heard. Turn auto/off switch to
“auto”.
4. Replace fuse or reset circuit
breaker.
5. Replace or repair pressure
switch.
6. Replace or repair motor.
7. Add lubricant (refer to Lubri-
cation).
8. Adjust belt (refer to Belt
Alignment & Adjustment).
9. Change power cord & volt-
age of motor to match power
source.
1. Power cord not plugged in.
2. OFF/AUTO switch in “OFF”
position.
3. Motor overload relay tripped.
4. Fuse blown &/or circuit
breaker is tripped.
5. Defective pressure switch.
6. Defective motor.
7. Lack of lubricant in compres-
sor (can cause serious damage
to compressor).
8. Belt too tight or too loose.
9. Motor voltage does not match
voltage of power source.
1. Compressor won’t operate.
TROUBLESHOOTING
Read and understand all the safety precautions listed in the front of this manual and follow all procedures
listed in MAINTENANCE before making repairs.