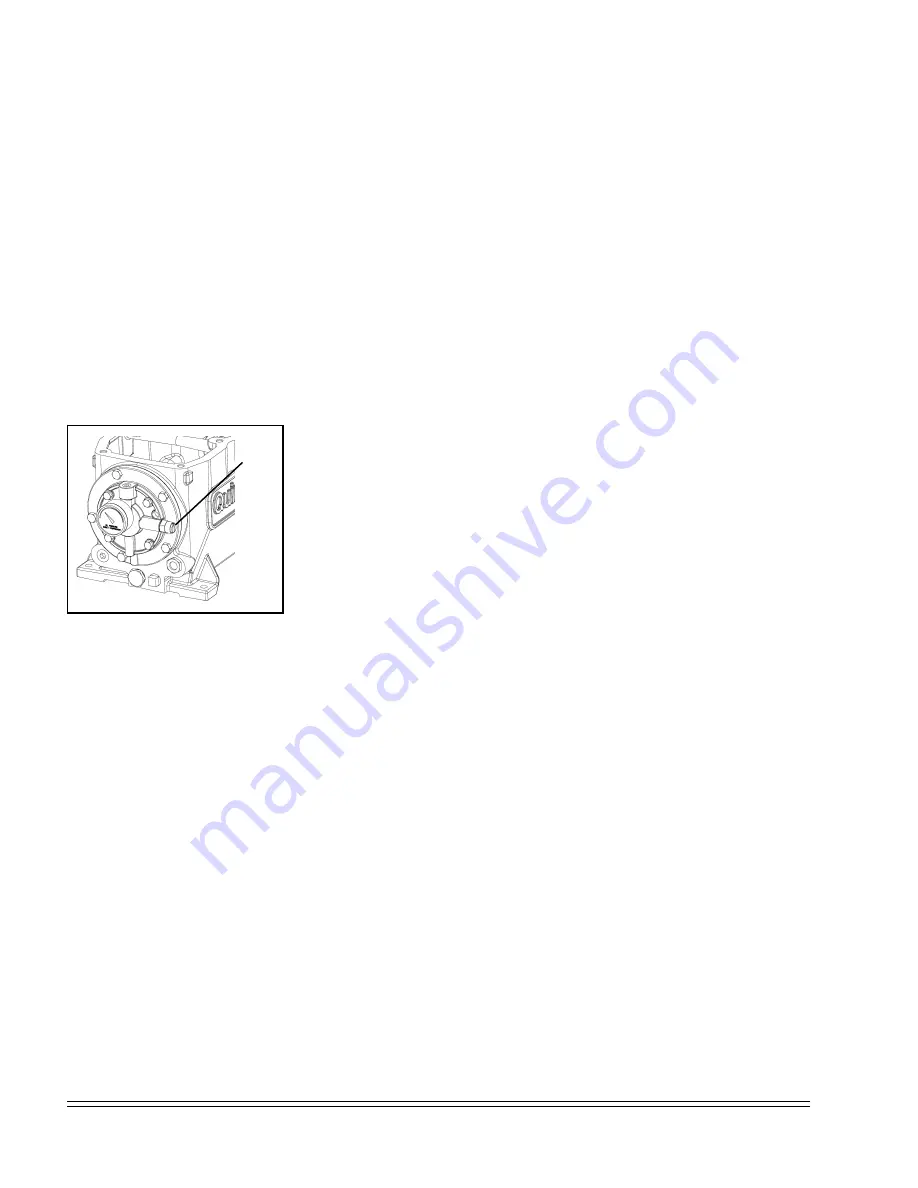
Industrial / Air Master Series
Quincy Compressor
50161-105, March 2008
24
3501 Wismann Lane, Quincy Ill. - 62305-3116
Step 12)
After all the above conditions have been satisfied, the unit can be
connected to the proper power source.
Step 13)
Jog the starter switch to check the rotational direction of the
compressor. It should agree with the rotation arrow embossed on
the compressor sheave.
Step 14)
Check for proper rotation of the cylinder cooling fan (fins inside
sheave). The fan should blow cooling air across the cylinder.
Initial Starting & Operating
This instruction manual, as well as any instructions supplied by manufactur-
ers of supporting equipment, should be read and understood prior to starting
the compressor. If there are any questions regarding any part of the instruc-
tions, please call your local Quincy distributor, or the Quincy Compressor
factory.
With the pre-starting checklist completed and satisfied, start the com-
pressor. Watch and listen for excessive vibration and strange noises. If either
exist, stop the compressor. Refer to
SECTION 6,
Troubleshooting
for help
in determining the cause of such problems.
If you are starting a pressure lubricated model, check the oil pressure.
Compressors producing up to 175 PSIG of discharge air pressure should
maintain 18 to 20 PSIG of oil pressure.
Normally the oil pressure does not need to be adjusted. But if it does,
loosen the locknut on the adjustment screw located on the right side of the
oil pump housing (see
Fig. 4-1, Oil Pressure Adjustment
). Increase the
oil pressure by turning the adjustment screw clockwise; decrease the oil
pressure by turning the adjusting screw counterclockwise. After adjust-
ment tighten the locknut.
Check the air receiver pressure gauge or system pressure gauge for proper
readings. If inadequate or excessive air pressure conditions exist, refer to
Section 6 Troubleshooting
.
Observe compressor operation closely for the first hour of operation and
then frequently for the next seven hours. After the first eight hours, monitor the
compressor at least once every eight hours. If any abnormal conditions are
witnessed, stop the compressor and correct the problem. After two days of
operation check belt tension, lubricant level, and inspect the system for leaks.
A new or rebuilt reciprocating compressor should be run for a total of 100
hours at full discharge operating pressure to break-in the new piston rings.
Until the rings are seated, the compressor will discharge higher than normal
amounts of lubricant. In light of this fact, the lubricant level should be checked
more frequently during the 100 hour break-in period.
Pix 1220
Fig. 4-1
Oil Pressure Adjustment
OIL
PRESSURE
ADJUSTMENT
SCREW
Содержание Air Master Series
Страница 46: ......