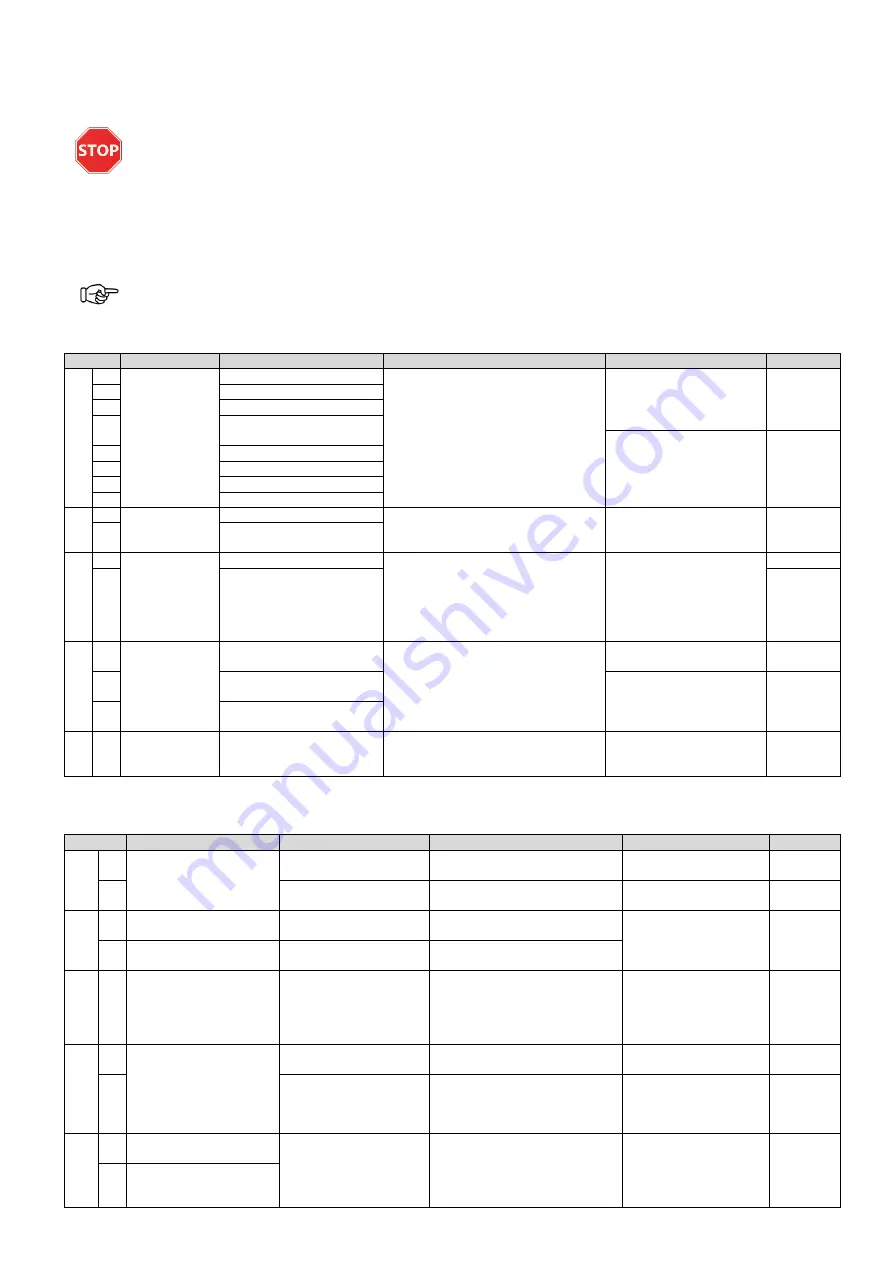
9
Troubleshooting
Warning:
Electrocution hazard! Before working on any live elements, pull out the mains plug
respectively switch off the main installation switch!
If a malfunction occurs which might be detrimental to the safety of the users, and
which cannot be eliminated without delay, the operator must be informed and if required
the installation shall be taken out of operation. The installation must be repaired as
soon as possible.
Note:
Every troubleshooting procedure which is carried out must be entered into the control booklet!
9.1
Drive mechanism
No.
Description
Cause
Elimination
Checking time
Reaction
E1
03
Encoder
Channels A+B lost
Check the encoder connection.
Check the motor cable.
The sense of rotation of the motor is not
in compliance with the rod assembly.
The door is blocked.
Check if a jumper has been inserted on
X106.
During run.
H
04
Short-circuit A+B
05
Dysfunctions
06
Motor cable plugged in
uncorrectly
Prior to start-up.
H
07
No channel A
08
No channel B
09
No channel A+B
10
Short-circuit A+B
E2
01
Motor current
Current too high
Check the motor cable.
Check if a jumper has been inserted on
X106.
Prior to star-up.
H
02
Current too low
Jumper missing
E3
01
Cushioning
Test failed once
Switch the drive unit to the MANUAL
operating mode and carefully check if the
door closes in a cushioned manner. If not:
replace the hardware. If yes:
check/correct the friction of the door leaf
and the prestressing of the closing spring.
Prior to the closing motion,
after start-up, and
subsequently every 24 h.
W
02
Test failed twice.
Damping defective.
F
E4
01
Reference
switchr
Detected in the open
position.
Check the connection and the switching
point of the reference switch.
The reference switch must be activated
in the closed position (switching contact
open).
Open position.
F
02
Not detected in the closed
position.
Prior to the first setting-up
run.
A
03
Not detected in open
position.
E5
00
Power limitation
Overload of the control. The
maximum power is restricted.
Check/correct the friction of the door leaf
and the pre-stressing of the closing
spring.
Permanent.
A
9.2
Operating
No.
Description
Cause
Elimination
Checking time
Reaction
E10
01
Fullteach required
Parameter Ao, Rod, Invers
or dAxis changed.
Carry out a teach.
Upon changing the
drive unit configuration.
H
02
Minimum opening angle
has not been reached.
Check the locking/electric lock.
During Teach.
H
E11
01
Halfteach required
(Opening)
Parameter Vo changed.
Carry out a complete and
unhindered .opening cycle.
Upon changing the
motional parameters.
W
02
Halfteach required
(Closing)
Parameter Vc or FSlam
changed.
Carry out a complete and
unhindered .closing cycle.
E12
03
Excessively high current
consumption during Teach
in the open position (> 5 A)
Drive unit pushes against
the open position stop
piece or an obstacle. The
spring tension is possibly
too high.
Reduce the opening angle Ao.
Reduce the spring tension.
Open position Teach 3
(E11).
F
E14
01
Locking/electric lock
The door leaf got caught in
the locking/electric lock.
Check the function of the locking/
electric lock.
When opening from a
closed position.
H
02
The inverted operation has
no locking, or the
interlocking force Fch has
not been programmed.
Program/increase the interlocking
force Fch.
At the end of the teach-in
procedure.
W
E15
01
Obstacle in opening
direction
Too many successive
obstacles have occured.
Examine the installation.
Remove the obstacle.
Move the door leaf to the target
position.
Permanent.
H, A
Restart
after 60 s
02
Number of obstacles within
60 seconds