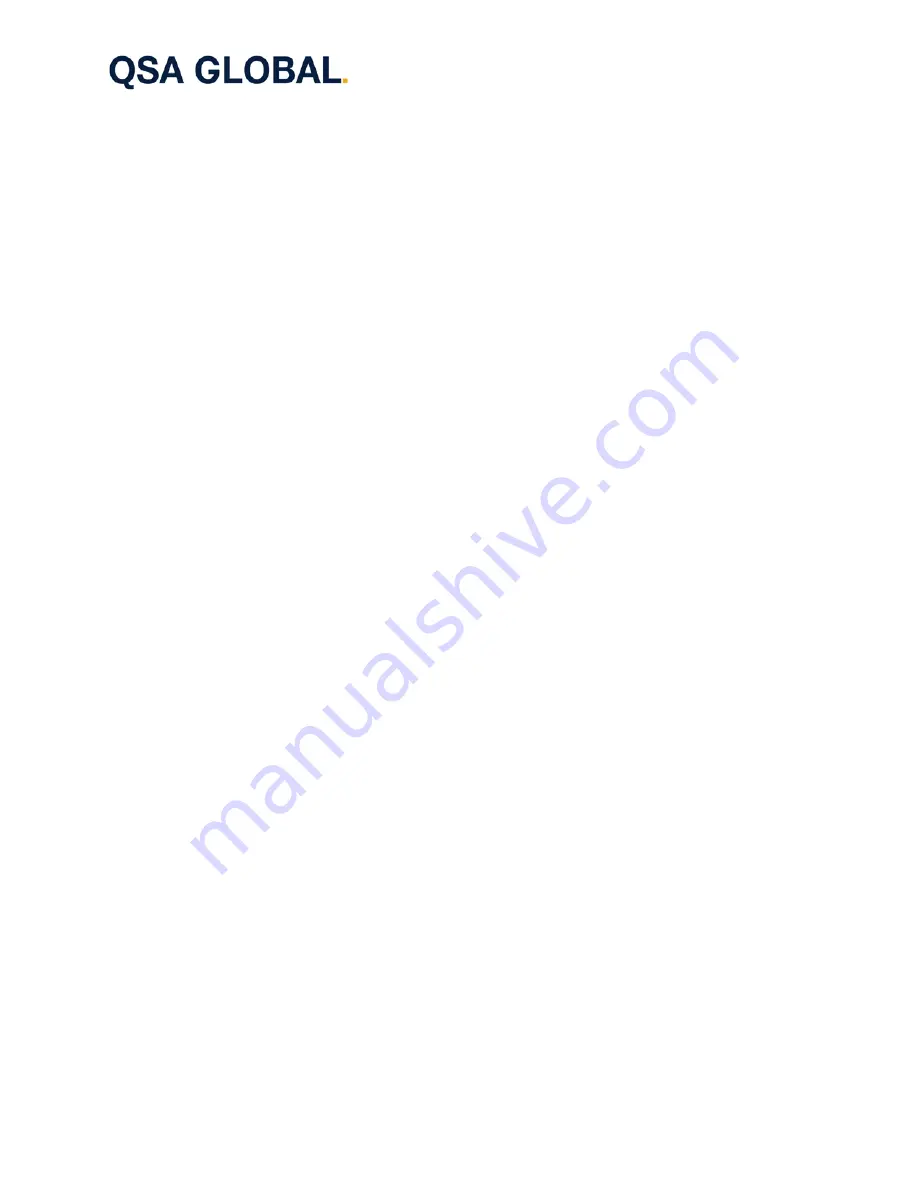
QSA Global, Inc.
40 North Avenue Burlington, MA 01803
888.272.2242
781.272.2000
qsa-global.com
Operations Manual
MAN-038 March 2019
Page 35 of 100
b. Pull approximately 12 in (30.5 cm) of control cable out of the connecting plug assembly and inspect
for the following anomalies directly behind the connector:
Cuts, breaks, nicks or fraying of the spiral windings of the control cable.
Areas with kinks or permanent bends.
Rust (a red oxide) on the inner core of the control cable.
Uniformity of the spacing (elongations or compressions) between the outer spiral windings. Also
check for flattened areas and wear.
Bend the connector section of control cable back towards itself (forming a “U”) and release the
cable to test for flexibility or ‘spring’ of the control cable. A cable that has been subjected to the
flexibility test and remains in the bent position after the test provides an indication of internal
corrosion and
must be removed from service
.
Verify that a light coating of mil-spec grease is present on the control cable. The light coating of
grease is necessary to prevent the penetration of water and chemicals that can oxidize and
permanently damage the control cable.
c. Check for freedom of movement of the control cable within the remote controls by moving the control
crank handle back and forth approximately one-quarter turn. During this test, take care to avoid
cranking the control cable onto the ground exposing it to dirt and sand. If any resistance is felt during
this check, re-inspect the control conduits for dents or depressions. If dents are not present on the
remote control conduits, the control cable may be rusted stiff somewhere within the control conduits.
Do not use remote controls that do not function properly or exhibit defects described above.
d. A final check of the control cable connector and source assembly connector is accomplished by use
of a Model 550 NO GO gauge to check for significant wear on the connectors that would affect safety.
Without using excessive force, check the following four positions (see Figure 9):
1 Ball at the end of the control cable connector must NOT GO into the hole of the gauge.
2 The shank or stem of the control cable connector must NOT GO into the smaller of the two
notches located on the side of the gauge.
3 The width of the gauge must NOT GO into the female slot of the source assembly connector.
4 After a positive connection between the control cable and source assembly connectors has been
accomplished, verify that the larger notch located on the side of the gauge will NOT GO in the
gap between the joined connectors.
Replace any components that fail any of the NO GO gauge tests, because a failure indicates
significant wear that could allow safety features of the design to be defeated.
IMPORTANT REMINDER
Do not compromise on safety. Always perform a daily inspection of the gamma-ray source
projector, projection sheaths and remote controls prior to use. Defective equipment that is
discovered during the daily inspection must be removed from service until repaired or
replaced.