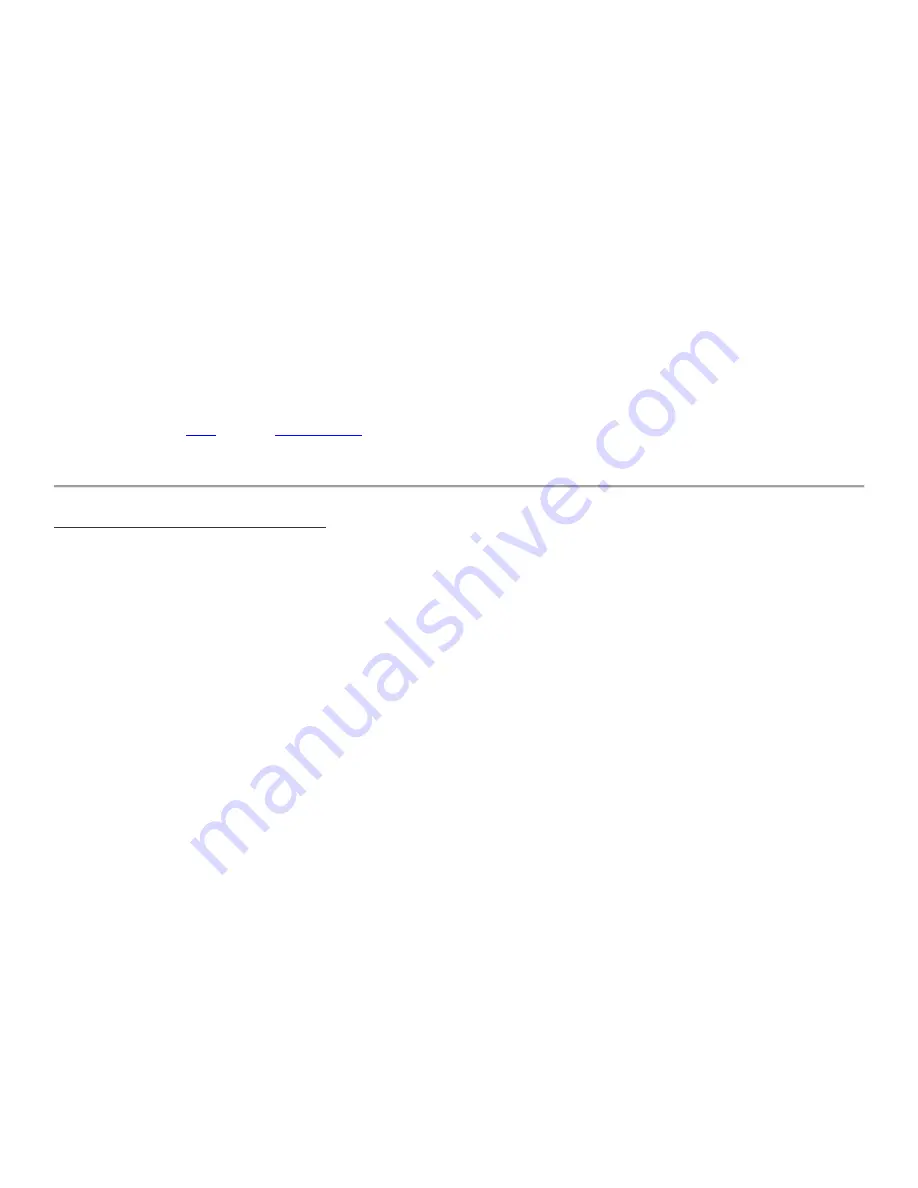
Page
3
of
25
Also don't panic if you had additional components left over: some capacitors are not used in some band versions of the
kit. And sometimes the kit packers make a mistake and put in one too many of a component (which is better than one too
few, right?).
Also check that the transistors are installed correctly - they are not all BS170's, there is also one MPS751 (or MPS2907).
Make sure that the MPS751 is in the right place (Q6). Check that all the other components are correct too, including:
Component value
Orientation of electrolytic capacitors
Orientation of transistors - the transistor body shape must match the silkscreen; the centre wire of the transistor is
bent forward to fit the centre point of the triangle, in the case of the BS170's
Diode orientation is correct: the stripe on the PCB matches the stripe on the component
IC dimples line up with the PCB
All pins of ICs are properly installed in their holes/socket positions (not bent under the chip)
These are preliminary checks, not very exciting, but they are a lot easier than some of the signal tracing that follows. And
surprisingly often, you can find the fault just visually like this, without any more complex investigation.
pages, to see if any of the problematic symptoms you see on your radio
are mentioned there.
Techniques for replacing components
Replacing components should be an absolute last resort! Check EVERYTHING else first! It is easy to suspect a damaged
component... but often, the component is not the problem, something else is! Replacing components is not easy, and
sometimes you can easily damage the delicate traces on the PCB. Removing components from through-hole plated,
double-sided PCBs is not easy. So run through ALL other checks first, to make sure you are certain the component is
broken, before trying it!
Removing a resistor or capacitor is normally not so hard, because they have only two wires. I find that by alternately
heating one joint and gently pulling, then the other, the component can be "rocked" free of the PCB. If the wires are bent
at all on the underside of the board, then start off by straightening them up, so they stand out at right-angles to the PCB.
This makes the job a lot easier.
Transistors can also be removed by the same technique, one wire at a time, gradually pushing them this way and that, to
gently ease them out bit by bit. Don't be tempted to use too much force, which can lift PCB traces, pads, or even pull out
the through-hole plating.
If the component is just installed in the wrong place, and you want to remove it and re-use it, then you need to be very
careful not to damage the component as well as the PCB. If the component is broken, then you don't care about
damaging it. This can make it easier to remove. For example in the case of a transistor, you can just cut off the transistor
wires with a wire cutter. Then remove each wire one at a time, with the soldering iron.
In the case of IC's I don't think you have any choice but to destroy the IC during removal. They have too many legs and
you can't easily heat them all at once, or lever the chip out one leg at a time. Surface Mount ICs are easiest to remove
and can survive the experience. Some people have hot air techniques where they blast the board with hot air until all the
solder joints of the IC are heated, and it just lifts out while everything is molten. This might be Ok if you are salvaging a
chip from an old PCB and you don't care much about what happens to the PCB, which can easily get damaged by all the
heat. In our case, we do care about the PCB. My method for removing chips (destructively) is, use a very sharp wire-
cutter and snip each of the pins right next to the chip body. The chip body can be cut out. Then remove each pin one by
one with the soldering iron.
In order to install new components, you will want to clear the solder out of the holes. The holes are all through-hole plated
and the solder wants to stay in the hole. But you want to get it out, so you can install the fresh component. There are
several ways of doing this. I find that the easiest way is desoldering braid. This is a thin ribbon of copper braid which looks
a bit like the outer shield braid of a coax. You put the braid on the hole and hold the soldering iron to it. When the solder
melts, it gets sucked up into the braid, out of the hole, just like water into a sponge. That's the theory and it doesn't always
work. Don't push too hard with the soldering iron, or hold the soldering iron to the pad too long. Too much heat and it is
easy to lift PCB pads.