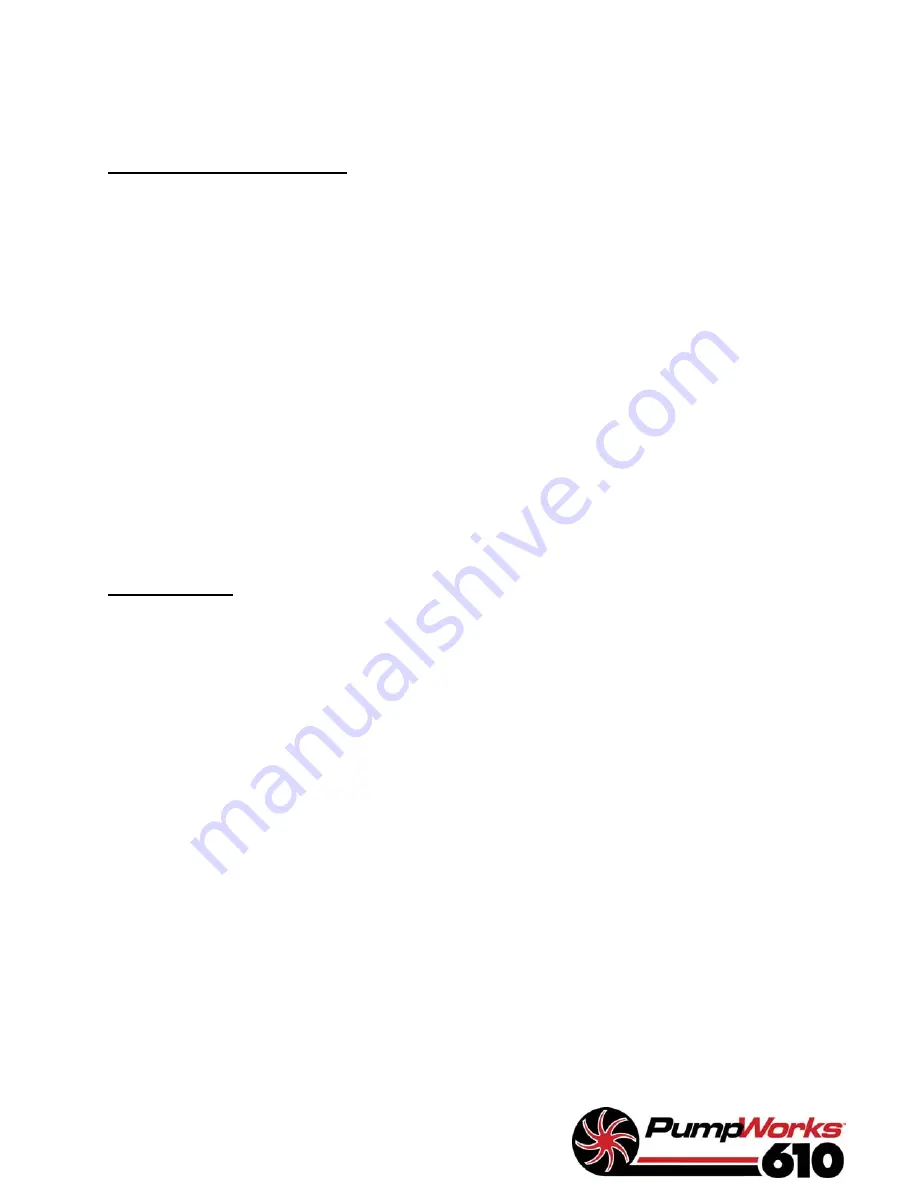
Model: PWD Rev. B_12/2/2015
should be of sufficient size to support the pump
foot.
The foot bolting can then be tightened to the
proper torque. Refer to standard torque charts,
or consult the factory if necessary.
DRIVER INSTALLATION
Once the driver has been mounted on the
base plate pedestals, the retaining bracket on
the drive shaft can be removed, if applicable. It
is important to inspect the shaft for runout. In
many cases, the motor will have a coupling hub
mounted on the driver from the factory. A check
by a dial indicator on the rim and face of the
coupling should be performed to ensure no
damage or warpage to the rotor has occurred.
The tolerances for runout should not exceed
.002” concentric (Rim), and .001” angular
(Face).
Set the motor to the magnetic center mark
and check the distance between shafts. Refer to
the general arrangement drawing for the proper
distance setting.
It is important to check the motor rotation
prior to coupling the units for operation. It may
be necessary to couple the units for alignment
purposes, but the motor should be uncoupled
and bump tested to ensure proper rotation prior
to operation.
PumpWorks normally allows approximately
.25” height difference for shimming of the motor.
Rough align the motor and check the motor for a
soft foot condition. The soft foot procedure is
described in the pump installation section above.
The total number of shims per foot should be
limited to 5 shims to prevent shim springing.
During the final alignment, considerations for
thermal growth of the driven equipment should
be considered. This includes vertical thermal
growth of the motor, as well as vertical and
horizontal growth of a driven gearbox.
ALIGNMENT
Proper alignment is important for the
longevity of your equipment. Although reverse
indicator alignment, and rim and face indicator
alignments can produce satisfactory results,
PumpWorks 610 strongly advises that laser
alignment equipment be utilized for the
alignment of this equipment.
Alignments should be performed by qualified
and experienced personnel. It is up to the end
user to ensure that all safety procedures,
especially lock out / tag out procedures, are
followed.
Motor rotation should be verified prior to
alignment, however, if initial alignment is
performed prior to checking the motor rotation,
the coupling of the driven unit should be
disengaged from the driver immediately after
alignment is performed. Motor rotation should
then be checked prior to reinstallation of the
coupling.
For motors with magnetically centered
rotors, ensure that the rotor is on magnetic
center and adjust to the proper end to end
distance between the shafts. Refer to the
General Arrangement Drawing as necessary for
the proper dimension. Ensure that no “soft foot”
condition exists on the motor or pump, if this has
not been performed. See the section “Pump
Installation” above for instructions on this
procedure.
The pump hold down holes should be
centered and torque to the proper torque value.
The motor bolts should have a minimum of 1/8”
clearance to the motor/driver mounting holes for
adjustment.
For laser alignments, the coupling spacer
needs to be installed for the final alignment.
Consideration should be taken for the vertical
thermal expansion of the motor. If a gearbox is
utilized, thermal expansion in the vertical and
horizontal directions should be compensated for.
The motor and gearbox manufacturers should
be able to supply expansion growth dimensions.
In the absence of such dimensions, the equation
for thermal expansion is expressed as follows:
Height / width (in inches) x Temperature Change (Ambient – Operating Temperature) x .0000067 (growth
coefficient)
Содержание PWD
Страница 1: ......
Страница 2: ...Page 2 of 28 Model PWD Rev B_12 2 2015 INSTALLATION OPERATION MAINTANENCE Model PWD ...