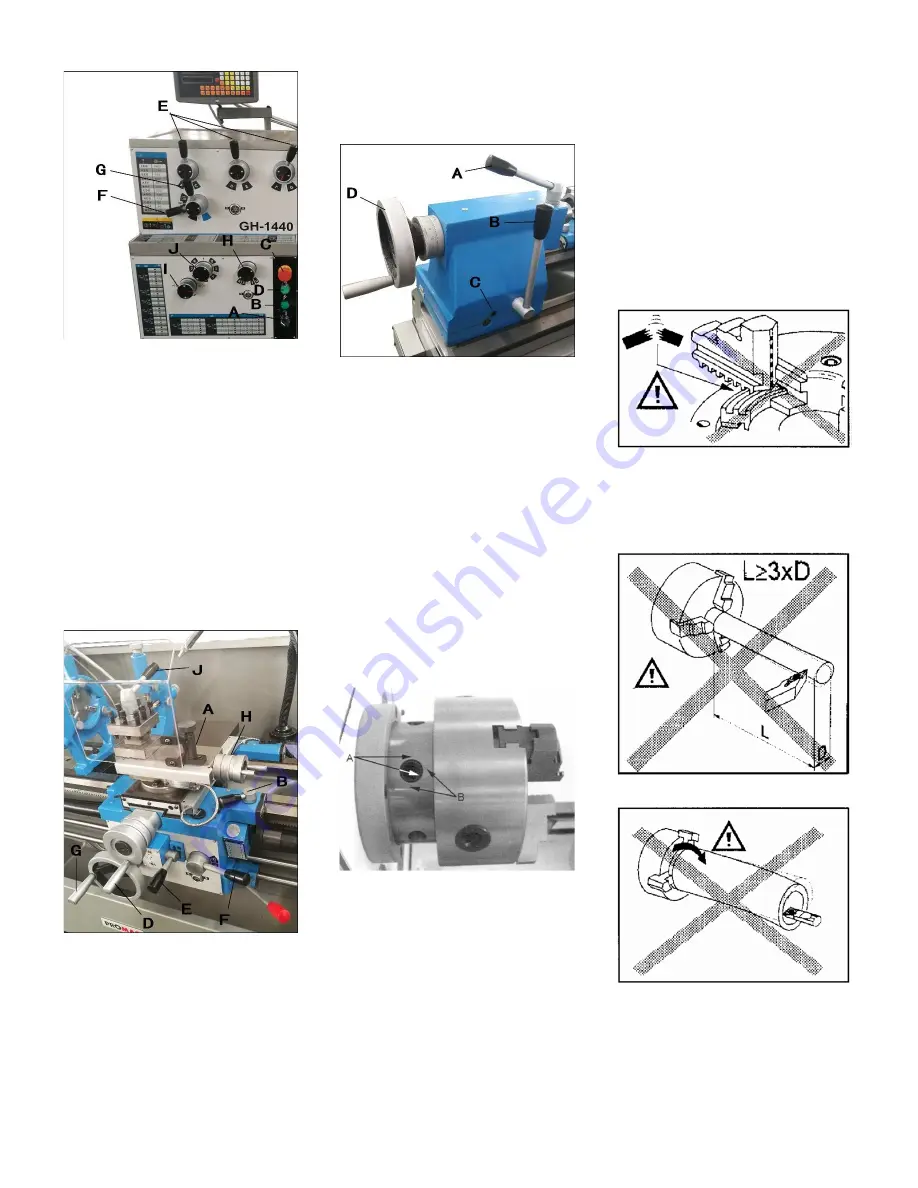
6
Fig 6
A….Coolant On/Off switch
B….Power indicator light
(shows that mains power is on)
C….Emergency stop button
D….Spindle jog button
E….Spindle speed levers
F…..Feed reversing lever
G….Feed / Lead selector lever
(max 650 rpm in position A)
H….Feed / Lead selector lever
S, U…for feed rod
R, T…for lead screw
Fig 7
A…..Top slide lock
B…..Carriage lock
D….Cross Slide Hand Wheel
E…..Automatic Feed Lever
longitudinal feed….right and up
cross feed………..left and down
F…..Half-Nut Lever (thread cutting)
G…..Longitudinal Travel Hand Wheel
H…..Top Slide Hand Wheel
J…..Tool post clamping lever
Fig 8
A….Tailstock Spindle Locking Lever
B.….Tailstock Locking lever
C….Tailstock off-set adjustment
D….Tailstock Spindle Hand Wheel
6.2 Chucking
Chuck removal:
Before removing the chuck from the
spindle, place board across the bed
ways under the chuck.
Support the chuck while turning three
cam locks ¼ turn counter-clockwise.
Line up the two marks (A, Fig 9) for
removal.
Fig 9
Carefully remove the chuck form the
spindle.
Clean all contact surfaces.
Chuck installation:
Lift the chuck up to the spindle nose
and press onto the spindle.
Tighten in place by turning the cam
locks ¼ turn clockwise.
The index mark (A) on the camlock
should be between the two indicator
arrows (B).
If not, adjust the cam studs by turning
them in or out by one turn as needed.
Tighten cam locks.
Attention:
Never exceed the max speed limitation
of the work holding device.
Jaw teeth and scroll must always be
fully engaged. Otherwise chuck jaws
may break and fly off in rotation (Fig
10).
Fig 10
Avoid long workpiece extensions.
Parts may bend (Fig 11) or fly off (Fig
12).
Use tailstock or rests to support.
Fig 11
Fig 12
Avoid short clamping contact (A, Fig
13) or clamping on a minor part
diameter (B).