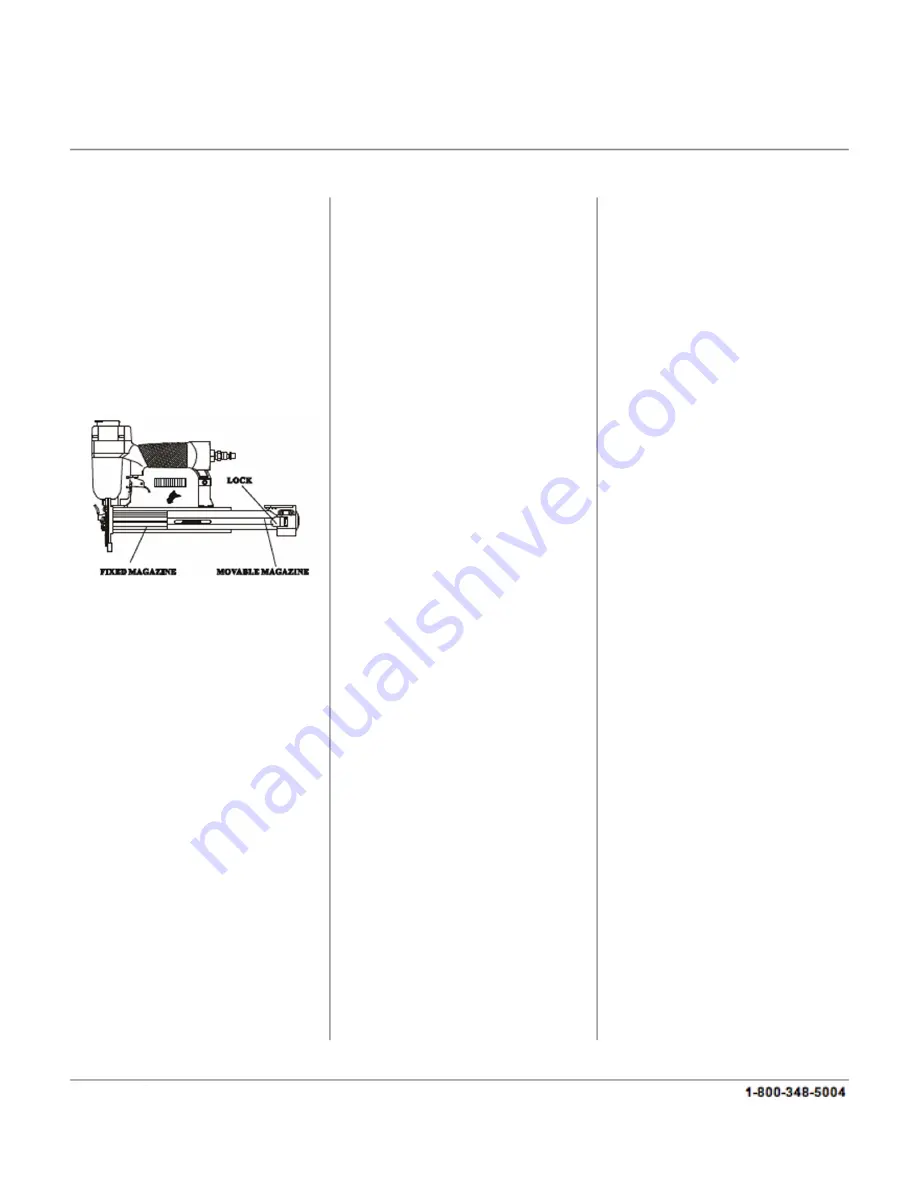
3
2) Turn the compressor on and
set the regulator to the proper
pressure for the size and type of
fasteners being used.
3) Connect the tool to the air
supply.
LOADING THE FASTENERS
1) Depress the lock to release
the movable magazine and pull
the magazine out fully as shown
below.
2) Place a full clip of the
specified type and size fasteners
on the fixed magazine, up to 100
fasteners may be loaded in the
magazine.
3) Push the movable magazine
assembly forward until it was
locked.
OPERATING THE TOOL
Test the driving depth in a
sample piece of wood before
using. If the fasteners are being
driven too far or not far enough,
adjust the regulator to provide
less air pressure or more air
pressure.
1) Connect the tool to the air
supply. Make sure the air
pressure is in correct range.
2) Load the fastener as above
the direction given in the
LOAD
THE FASTENERS
section.
3) Hold the body and press the
drive guide to the work surface.
Be sure the tool is straight and
then gently depress the trigger to
drive the fastener.
4) Lift the tool off the work
surface.
5) The tool has two driving
modes.
§
Put the nose on the work
surface, lightly push the tool
towards the working surface until
the safe bracket is depressed.
Depress the trigger to drive the
fastener.
§
Depress the trigger, then
repeatedly impact the safe
bracket. The tool can repeatedly
drive the fasteners. The tool will
drive one fastener when the safe
bracket is impacted one time.
REGULAR MAINTENANCE
1) Frequent, but not excessive,
lubrication is required for best
performance. Oil added through
the airline connection will
lubricate internal parts. An
automatic airline oiler is
recommended but oil may be
added manually before every
operation or after about 1 hour of
continuous use. Only a few
drops of oil at a time are
necessary. Too much oil will
collect inside the tool and be
blown out during the exhaust
cycle. ONLY USE PNEUMATIC
TOOL OIL. Do not use detergent
oil or additives as these
lubricants will cause accelerated
wear to the seal in the tool.
2) Use a small amount of oil on
all moving parts and pivots.
3) Dirt and water in the air
supply are major causes of
pneumatic tool wear. Use a
filter/oiler for better performance
and longer life. The filter must
have adequate flow capacity for
the specific application. Consult
the manufacturer’s instructions
for proper maintenance of your
filter.
4) Keep tools clean for better
and safer performance. Use
nonflammable cleaning
solutions (
CAUTION:
Such
solutions may damage O-Ring
and other tool parts) only if
necessary. DO NOT SOAK.