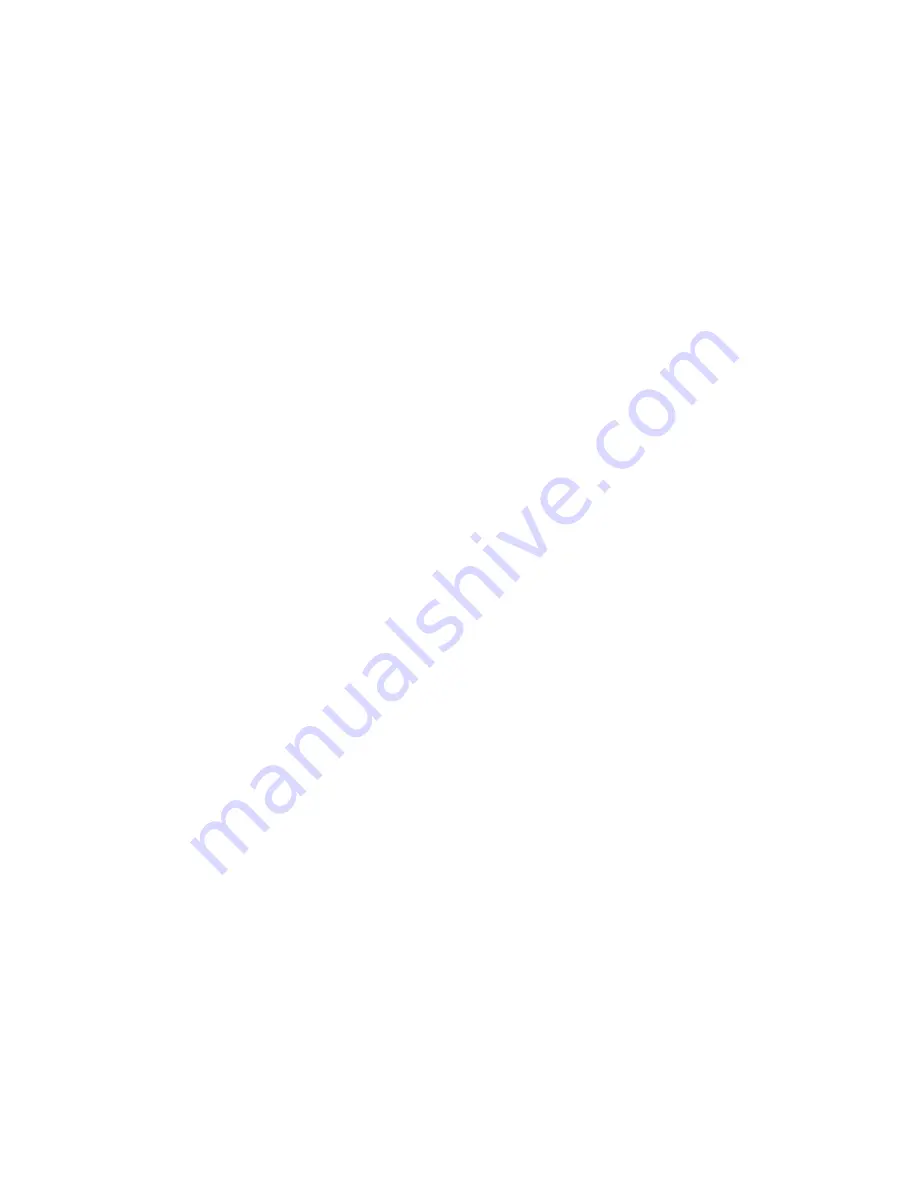
179414-001A
*179414-001*
For technical assistance, contact your
Distributor/VAR/Reseller for service.
For further assistance, contact the Printronix Customer Support Center.
Printronix Customer Support Center
Americas
(714) 368-2686
Web site: http://www.printronix.com/public/servicessupport/default.aspx
Printronix Supplier Center
Americas
(800) 733-1900
Web site: http://www.printronix.com/public/supplies/default.aspx
Printronix, Inc.
14600 Myford Road
P.O. Box 19559
Irvine, CA 92623-9559
Phone: (714) 368-2300
Fax: (714) 368-2600
Содержание SLPA7000e
Страница 1: ...SLPA7000e Smart Label Printer Applicator Operator s Reference Training Manual...
Страница 2: ......
Страница 3: ...Operator s Reference Training Manual SLPA7000e Smart Label Printer Applicator...
Страница 22: ...22 Chapter 1 Calibrating The Printer...
Страница 38: ...38 Chapter 2 Loading A Saved Configuration...
Страница 60: ...60 Chapter 4 System Adjustments...
Страница 62: ...62 Chapter 5 Illustrated Parts Breakdown Figure 25 Ribbon Drive Assembly 1 14 2 3 5 7 8 6 9 10 11 12 4 13...
Страница 66: ...66 Chapter 5 Illustrated Parts Breakdown Figure 27 Brake Assembly 1 8 2 4 3 5 6 7 9 10 11 12 13 14 15 16...
Страница 68: ...68 Chapter 5 Illustrated Parts Breakdown Figure 28 14 inch Cylinder Assembly 1 2 3 4 5 6 7 8 9 10 11 12 13 14...
Страница 70: ...70 Chapter 5 Illustrated Parts Breakdown...
Страница 74: ...74...
Страница 75: ......