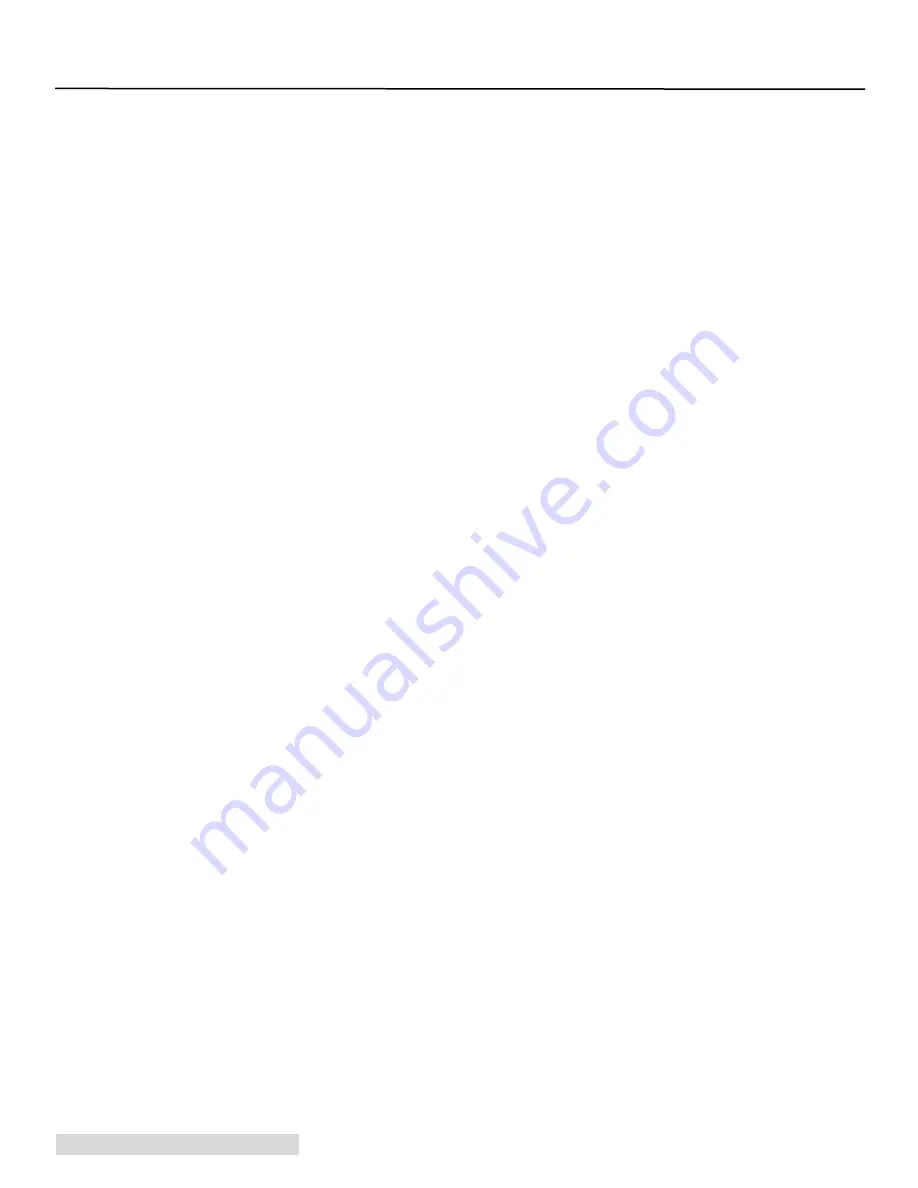
Troubleshooting
Labels are applied to the container crooked.
1. Check for container taper. Some containers such as wine bottles may have a slight taper
that will cause the label to be applied crooked. You may be able to apply your label
straight if you angle the container idler roller to correspond with the angel of the taper.
For example, if you normally apply labels to the bottle with both sides of the container
idler roller in the third notch from the drive roller, try putting one side in notch three and
the other side in notch four.
2. Roll Guides should also be positioned very close to the roll, but not squeezing any part of
the roll (so the roll has very little play side-to-side between the guides).
3. It may take several labels to allow the label stock to “straighten-out” or “settle-in” where
it will run for the duration of the roll. It will “settle-in” quicker if you make sure to get the
label stock loaded relatively square to the roll.
4. For larger heavier rolls make sure that the roll is positioned on top of the Roll Guides with
the magnetic portions facing in. This will minimize the chances that the heavy roll will
push the guides out of place.
5. For lighter rolls make sure the Roll Drag Arm is in place as described in the manual. If
you do not have a Roll Drag Arm please contact tech support.
Tapered bottles.
Many wine bottles have a slight taper to them. Using the normal procedures outlined in the
manual will cause the labels to be applied crooked. You may be able to apply your label
straight if you angle the container idler roller to correspond with the angel of the taper. For
example, if you normally apply labels to the bottle with both sides of the container idler roller
in the third notch from the drive roller, try putting one side in notch three and the other side
in notch four.
Motor stalling on labels 6" (15.3 cm) or wider.
For label stock 6” (15.3 cm) and wider, it may be necessary to reduce the speed of the Label
Applicator. The AP360/362 includes a half-speed mode that generates more power from
the motors for wider label stock. To activate this mode, hold down the Foot Switch while
switching on the unit. The AP360/362 will revert back to the default mode when switched
on without holding down the Foot Switch.
AP360/362 is running slow.
See Section 6.2. Make sure the foot switch is not depressed at any time during the boot up
sequence.
Small diameter containers.
Small containers such as chap stick containers which are close to the edge of the minimum
allowed diameter specification (0.6") will occasionally get pushed off the rollers by the
oncoming label. To solve this problem add pressure to the arm by hand while applying labels
on extremely small containers. This will prevent the label from pushing the container off the
rollers.
There are bubbles or wrinkles in the label.
Wrinkles or bubbles can appear on the applied label if the container is not completely round,
is not smooth or has bumps or ridges. To minimize bubbling or wrinkling with such bottles
smooth the labels by hand as the container rotates around. For this procedure you must apply
labels with out using the container pressure arm.
16 AP360/362 Label Applicator
Section 6: Troubleshooting and Maintenance
Содержание AP360
Страница 19: ...AP360 362 Label Applicator 19...
Страница 20: ...P N 511218 101609...