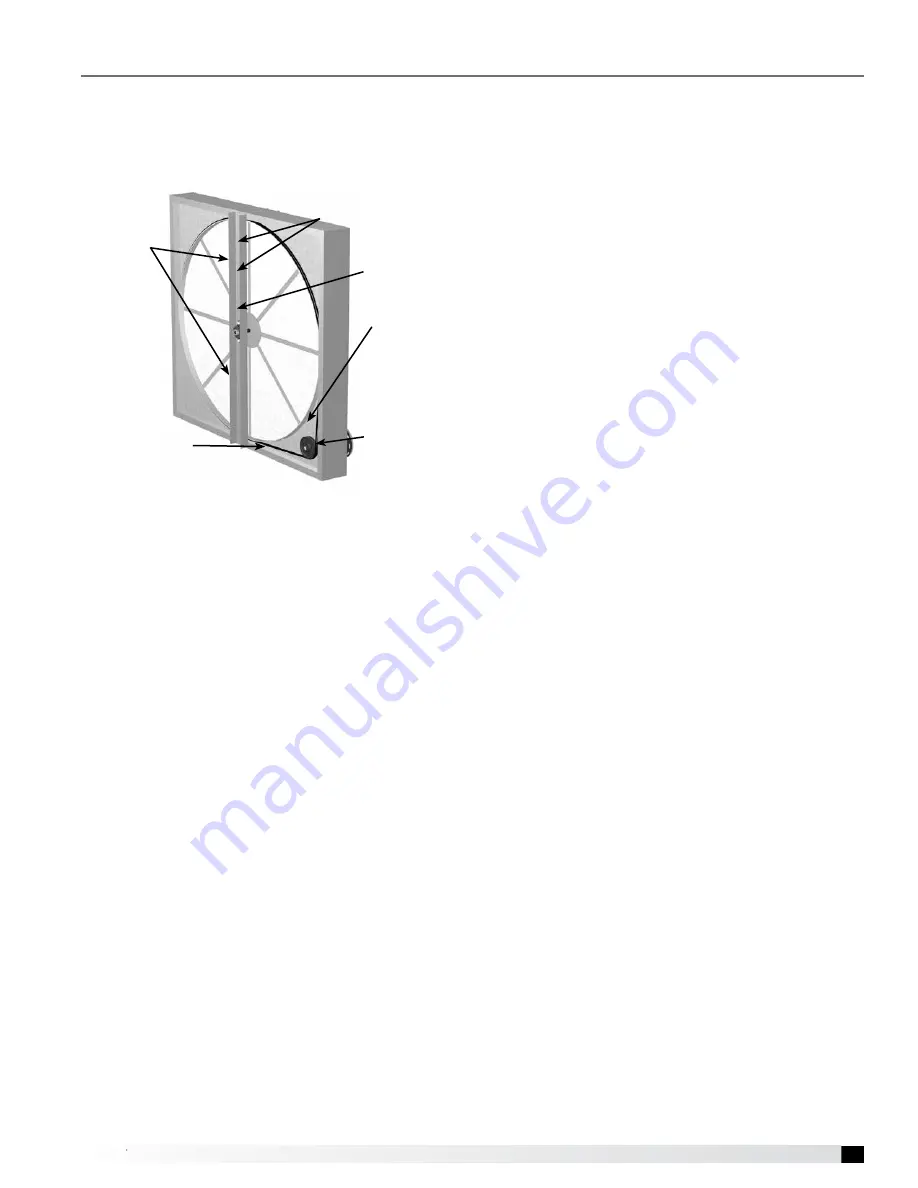
37
Packaged and Split Rooftop Ventilator
© 2021 Mitsubishi Electric US, Inc.
Premi
Sys
Sequence of Operation
Optional Economizer
- The economizer will be locked
out when: the outside air is below economizer lockout;
the unit is operating in dehumidification mode; or there
is a call for heating.
•
Stop Wheel:
When economizer mode is enabled
and there is a signal for cooling, the wheel will stop
rotating to allow free cooling.
•
Modulate Wheel:
When economizer mode is
enabled and there is a signal for cooling, the
wheel VFD modulates wheel speed to maintain the
discharge temperature set point.
Optional Frost Control
-
Polymer Wheel
The microprocessor controller will output a signal
when wheel frosting is occurring which is determined
by a temperature set point (OA <5°F – 2°F hysteresis,
adjustable) and wheel pressure drop increase.
•
Preheat:
When frosting is occurring, the preheater
is energized to defrost the wheel. Once the
pressure drop decreases below the set point, the
preheater is de-energized.
•
Timed Exhaust:
When frosting is occurring, the
supply blower is cycled off. The exhaust blower
shall continue to run, allowing the warm exhaust
air to defrost the wheel. After the 5 minute cycle,
the supply fan is re-energized to continue normal
operation.
•
Modulating Wheel:
When frosting is occurring,
the wheel VFD will reduce wheel speed to prevent
condensation and frosting. If the outdoor air
temperature is greater than the frost threshold
temperature OR the pressure differential is less
than the set point, the wheel will run at full speed.
If the outdoor air temperature is less than the frost
threshold temperature AND the pressure differential
is greater than the set point, the wheel will run at
reduced speed until the pressure differential falls
below the set point. The temperature and pressure
differential set points are set at the factory, but are
field-adjustable. The VFD will be fully programmed
at the factory.
Optional Polymer Energy Wheel
Start-Up
If selected, the energy wheel is installed in the unit with
one half of the wheel in the outdoor airstream and one
half in the exhaust airstream. The energy wheel includes
air seals to minimize leakage between airstreams.
Drive Belt
Inspect the drive belt. Make sure the belt rides smoothly
in the pulley and around the outside of the wheel. Note
the directional arrow and data information shown in the
image.
Adjust the Air Seals
(Polymer wheels only)
The information below only applies to polymer wheels,
which require air seal adjustment at the time of start-up
for proper performance. Aluminum wheel air seals are
factory-set and do not require field adjustment.
Make sure the unit power supply is locked out.
Disconnect the wiring to the wheel module and pull
the wheel cassette out of the cabinet on its tracks.
Large cassettes are not removable. Then slowly rotate
the wheel by hand to make sure there is no binding or
misalignment.
There is a perimeter seal located around the outside of
the wheel and a diameter seal across the face of the
wheel on both sides. Check to make sure that all air
seals are secure and in good condition.
Adjust the air seals by loosening all the air seal retaining
screws on the bearing support. Using a piece of paper
as a feeler gauge, adjust the seals so they almost touch
the face of the wheel while tugging slightly on the paper.
When the wheel is rotated, there should be a slight tug
on the paper. Tighten the screws, repeat the steps on
the other set of seals.
Push the wheel cassette back into the unit and plug
in the power connector. Turn the main power supply
back on and then observe the operation of the wheel by
opening the wheel access door slightly. Remove filters if
necessary to observe the wheel.
Drive Belt
Adjustable
Air Seals
Label
showing
cassette
serial # and
date code
Bearing
Support
Drive Pulley
Retaining
Screws