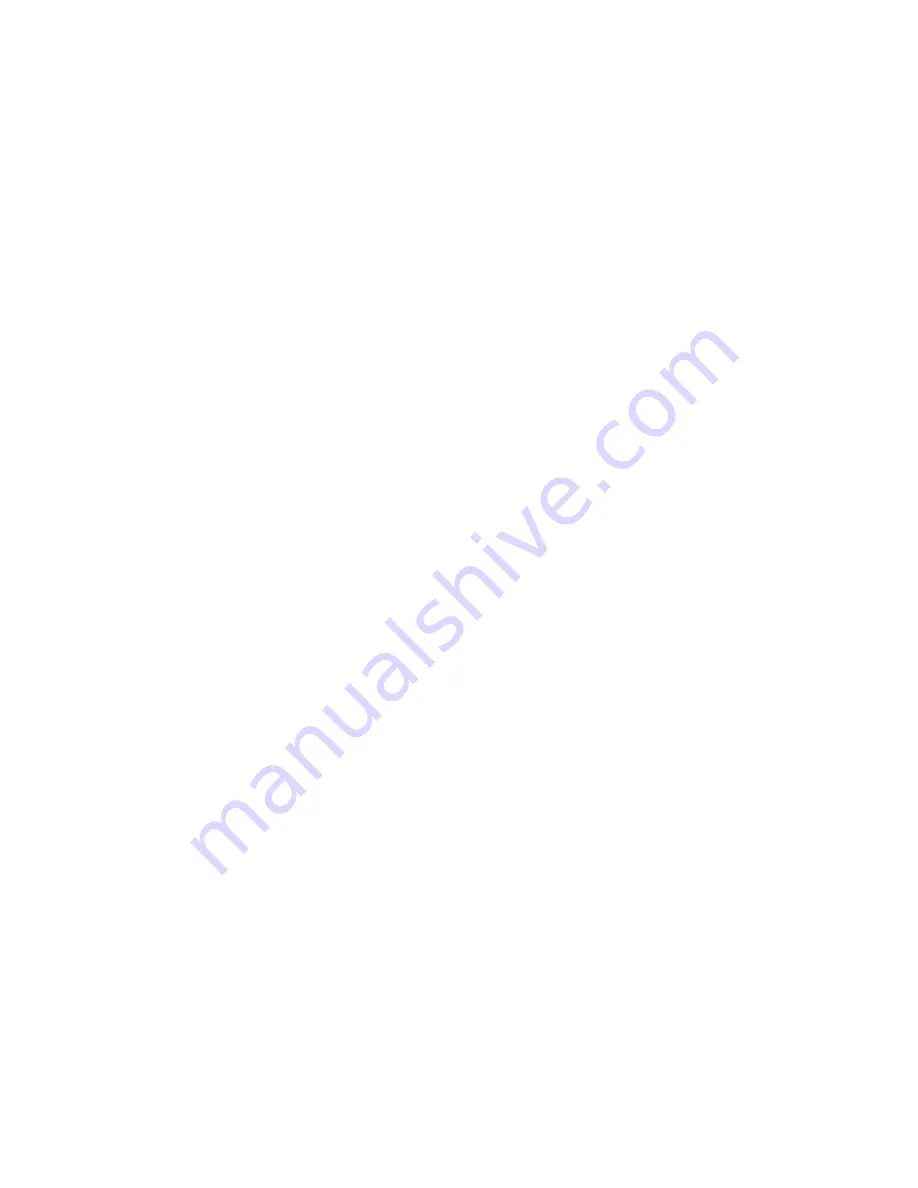
20
PREMIER E SERIES DUAL CAPACITY INSTALLATION AND MAINTENANCE MANUAL
BEFORE POWERING UNIT, CHECK THE FOLLOWING:
❏
High voltage is correct and matches nameplate
❏
Fuses, breakers and wire size correct
❏
Low voltage wiring complete
❏
Piping completed and water system cleaned and flushed
❏
Air is purged from closed loop system
❏
Isolation valves are open, water control valves or loop pumps wired
❏
Condensate line open and correctly pitched
❏
Transformer switched to 208V if applicable
❏
Black/white and gray/white wires in unit control box have been removed if auxiliary heat has been
installed
❏
Dip switches set correctly
❏
DHW pump switch off unless piping is completed and air has been purged
❏
Blower rotates freely - foam shipping support has been removed
❏
Blower speed correct (dip switch set correctly)
❏
Air filter cleaner is clean and in position
❏
Service/access panels are in place
❏
Return air temperature is between 50-80
°
F in heating and 60-95
°
F in cooling
❏
Check air coil cleanliness to insure optimum performance. Clean as needed according to
maintenance guidelines. To obtain maximum performance the air coil should be cleaned before
start-up. A 10 percent solution of dishwasher detergent and water is recommended
for both sides of coil, a thorough water rinse should follow.
START-UP STEPS:
NOTE:
Complete the Equipment Start-Up/Commissioning Check Sheet (WFS147) during this proce-
dure. Refer to thermostat operating instructions and complete the start-up procedure.
1)
Initiate a control signal to energize the blower motor. Check blower operation.
2)
Initiate a control signal to place the unit in the cooling mode. Cooling setpoint must be set
below room temperature.
3
First stage cooling will energize after a time delay.
4)
Be sure that the compressor and water control valve or loop pumps are activated.
5
Verify that the water flow rate is correct by measuring the pressure drop through the heat
exchanger using the P/T plugs and comparing to water pressure drop found on Table 2
on page 21.
6)
Check the temperature of both the supply and discharge water. (Refer to Table 1 on page 21.)
7)
Check for an air temperature drop of 15 to 25 degrees Fahrenheit across the air coil,
depending on the fan speed and entering water temperature.
8)
Decrease the cooling set point several degrees and verify high-speed blower operation.
Verify that the compressor switches to high-capacity operation after a one-minute time delay.
9)
Adjust the cooling setpoint above the room temperature and verify that the compressor and
water valve or loop pumps deactivate.
10) Initiate a control signal to place the unit in the heating mode. Heating setpoint must be set
above room temperature.
11) First stage heating will energize after a time delay.
12) Check the temperature of both the supply and discharge water. (Refer to Table 1 on
page 21.)
13) Check for an air temperature rise of 20 to 35 degrees Fahrenheit across the air coil,
depending on the fan speed and entering water temperature.
14) Increase the heating set point 2-3 degrees above current room temperature and verify that
the compressor switches to high-capacity operation after a one-minute time delay.
Unit Start Up