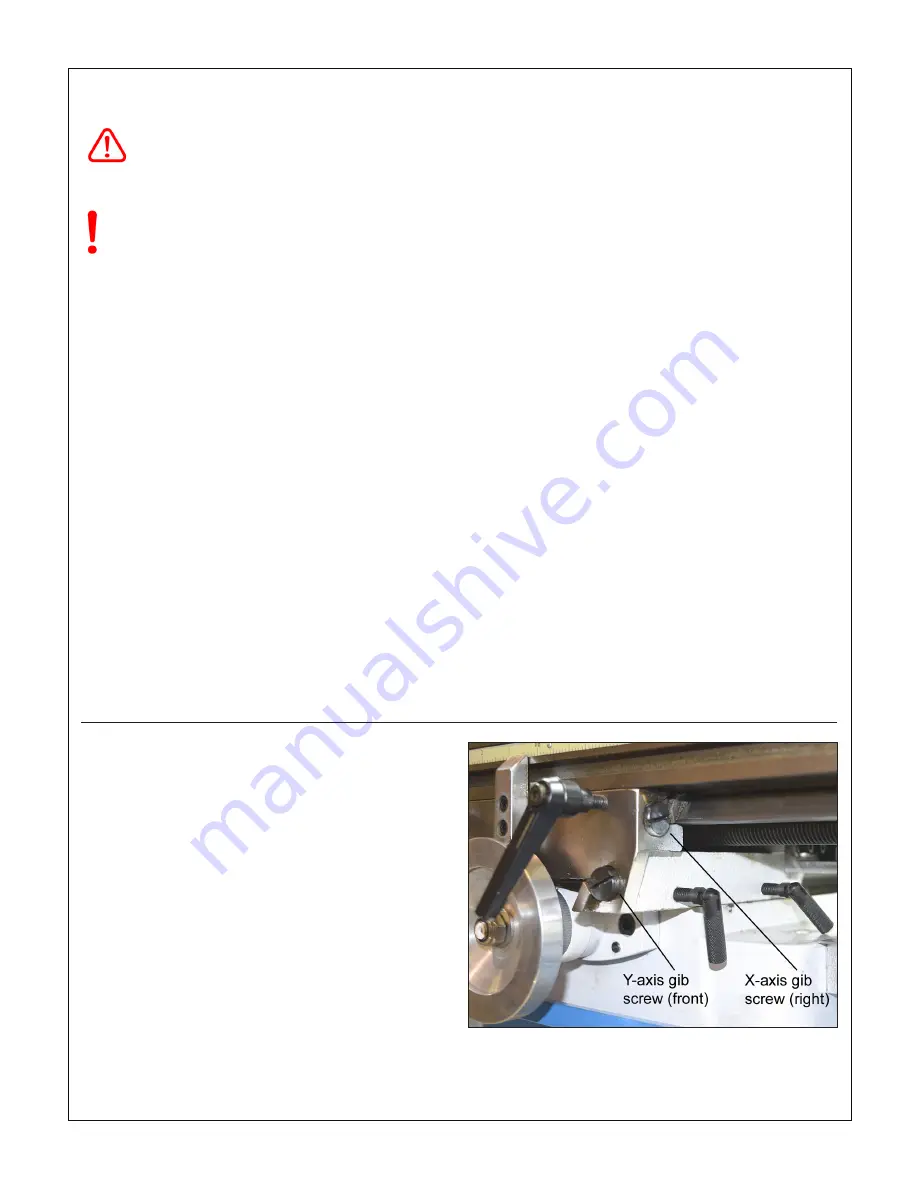
16
PM 25MV v9 2020-10
Copyright © 2020 Quality Machine Tools, LLC
Section 4 MAINTENANCE
Unplug the 120V power cord before
any maintenance operation!
RECOMMENDED LUBRICANTS
Ball oilers
(X and Y leadscrews): ISO 68 oil, such as
Mobil Vactra No. 2, or equivalent
X, Y and Z axis ways
(dovetails): ISO 68 oil, Mobil
Vactra No. 2, or equivalent
Visible gears
such as quill rack and pinion, Z-axis
bevel gears: light general purpose grease, NLGI No. 2,
or equivalent
X and Y leadscrews
: ISO 68 oil, Vactra No. 2, or
equivalent
Z leadscrew
: ISO 68 oil or NLGI No. 2 grease
GENERAL OILING
Assuming a clean environment – no abrasive particles or
machining debris – lack of proper lubrication is the main
cause of premature wear. Rotating parts are easy to lu
-
bricate, sliding parts are not. Gibs are tightened for
the
best compromise between rigidity and slideability, which
Remove all machining debris and foreign
objects before lubricating ANYTHING! If need
be, any oil is better than no oil – but use the
recommended lubricants when you can.
Ball oilers
Use a pump-type oil can with tip large enough to more
than span the oiler’s spring-loaded steel ball. Oil pres
-
sure will displace the ball, allowing oil to flow, provided
the oil can tip is firmly pressed onto the brass seating.
Before oiling check that the ball is not stuck – press it
lightly with a probe.
means practically zero gap between the ways. Take time
to understand exactly which are the bearing surfaces on
the various dovetail surfaces; this is not obvious – some
of the interfaces look like bearing surfaces, but are sim-
ply narrow gaps.
Every few hours of operation: 1. Apply the recommend
-
ed way-oil with a dedicated short-bristle brush such as
the type used for applying flux; 2. Use a similar brush to
apply oil or grease to the leadscrews; 3. Apply oil to the
ball oilers, see below.
Quill rack and pinion
Lower and lock the quill. Using a stiff flux brush, clean
the visible portions of the rack and pinion. Raise and
lower the quill to expose the remainder of the working
surfaces, locking and cleaning at each setting.
Sindle bearings
See Servicing Quill and Spindle, two pages on.
GIB ADJUSTMENT
Gibs on the X, Y and Z axes control the fit of the mating
dovetailed surfaces. They are gently-tapered lengths of
ground cast iron located by opposing screws at each
end. Adjusting them is a trial and error process that
takes time and patience. Aim for the best compromise
of rigidity and reasonably free table movement. Too tight
means accelerated wear on the ways and leadscrews.
Too free means workpiece instability, inaccuracies and
chatter.
Both screw heads
must be tight against the gib ends.
If you loosen one, tighten the other. Remove the way
covers for access to the back of the Y gib and bottom of
the Z gib.
Figure 4-1
Gib adjustment, X and Y axes
The back adjustment screw for the Y axis gib is under the solid rubber
way cover behind the table. The left adjustment screw for the X axis is
in a similar location on the left side of the saddle casting.