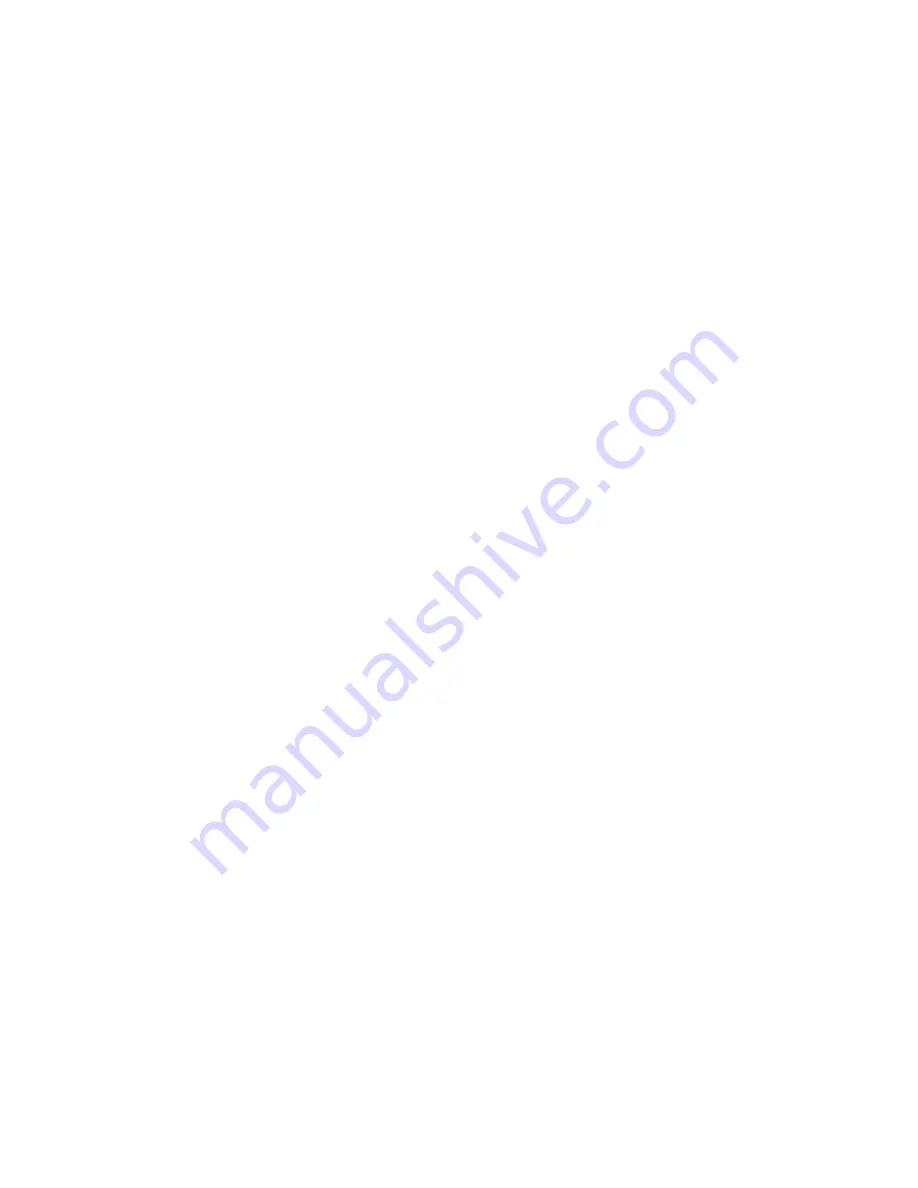
DISCLAIMERS
All information referred to and/or included in this manual is current as of the original issue date of
this manual. Praxair Surface Technologies, Inc. makes no warranty or representation with respect to
the accuracy of the information contained therein nor with respect to the suitability of the use of
such information outside Praxair Surface Technologies, neither does Praxair Surface Technologies
assume responsibility for any injury or damage which may result, directly or indirectly, from the
use of such information.
The information contained herein is offered for use by technically qualified personnel at their
discretion and risk without warranty of any kind. Praxair Surface Technologies is constantly
improving its products, and specifications are subject to change without notice.
This manual could include technical inaccuracies or typographical errors. Changes are made
periodically to the information herein; these changes will be incorporated in subsequent revisions of
the manual. Praxair Surface Technologies reserves the right to make improvements and/or changes
to the product(s) and/or programs described in this manual at any time and without notice.
Illustrations are meant to be representative of, but not exact duplicates of, existing equipment.
BUSINESS CONFIDENTIAL
THIS MANUAL CONTAINS CONFIDENTIAL AND PROPRIETARY INFORMATION
OF PRAXAIR SURFACE TECHNOLOGIES. THIS INFORMATION IS PROVIDED IN
CONFIDENCE SOLELY FOR USE WITH OUR MODEL 1264 POWDER FEEDER. THIS
MANUAL MAY NOT BE REPRODUCED IN ANY FORM OR ITS CONTENTS
DISCLOSED TO THIRD PARTIES WITHOUT THE PRIOR WRITTEN CONSENT OF
PRAXAIR SURFACE TECHNOLOGIES.
TRADEMARK INFORMATION
Praxair
and the
Flowing Airstream
design are trademarks or registered trademarks of Praxair
Technology, Inc. in the United States and other countries.
TAFA and the TAFA Flame design are trademarks or registered trademarks of Praxair S.T.
Technology, Inc. in the United States and other countries.
Other trademarks used herein are trademarks or registered trademarks of their respective owners.
Praxair Surface Technologies, Inc.
Printed in the United States of America. Copyright © 2015
Praxair S.T. Technology, Inc.