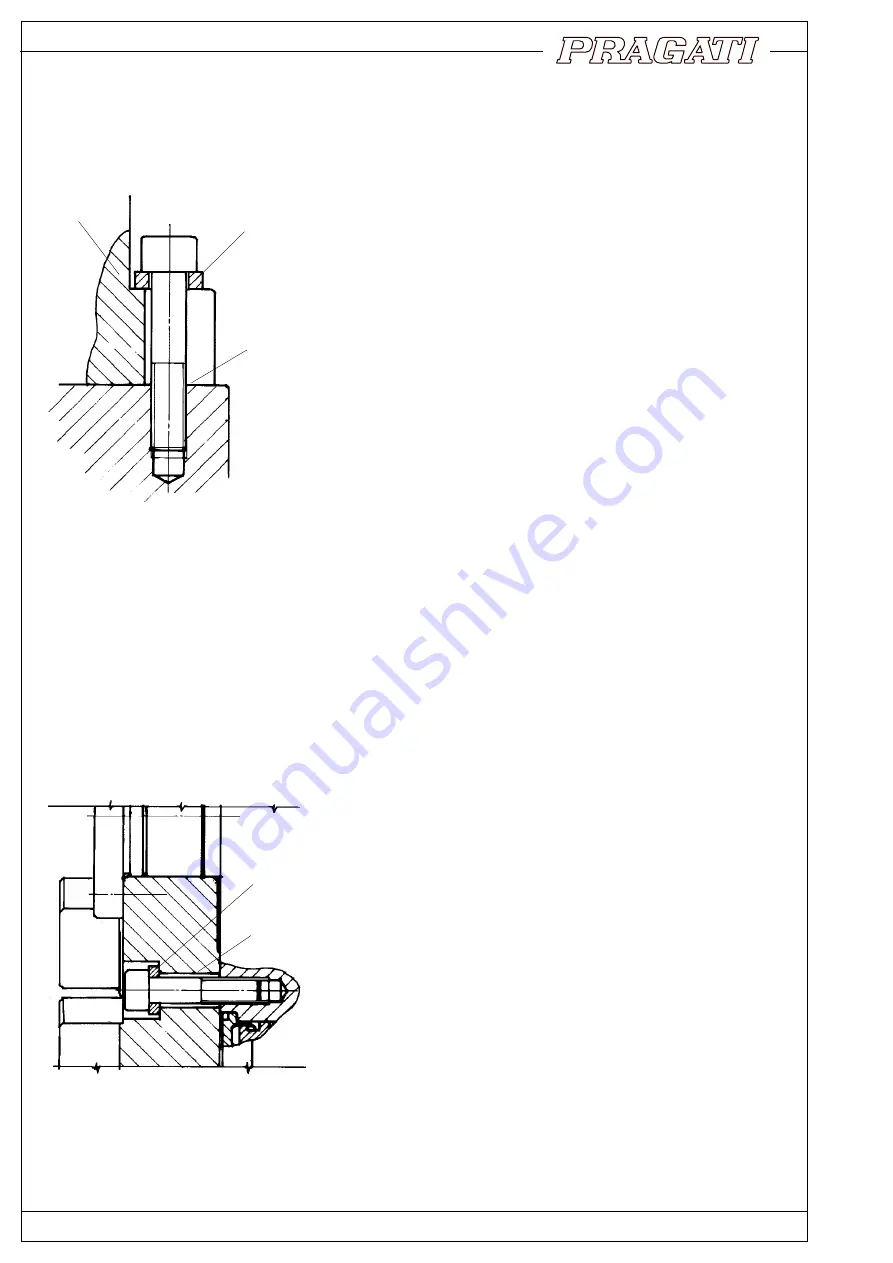
6
BI-DIRECTIONAL TOOL TURRETS
2. Fitment on the machine :
Seating surface of the machine should be flat to ensure proper
contact with the turret base. Machine surface should be either
scraped or surface-ground.
Turret should be aligned by dialing surface of the indexing
flange. Clamping bolts should be tightened after aligning the
seating surface, square to the lathe axis.
Clamping bolts should use machine washers of extra thickness
(min.5 mm) to ensure proper clamping.
Dowel Pins are not recommended for ensuring the alignment
of turret. It is preferable to allow the turret to slip in the event
of an accidental shock or overload. This slipping absorbs
some of the energy of the shock and reduces the possible
damage. Turret can again be brought back to alignment by
dialing a reference surface on the tool disc.
There is one more reason for avoiding the dowel pin. Acci-
dental collisions are not un-common in the field of CNC lathes.
In the event of a collision, dowel pins can get sheared or
damaged. It is a difficult task to remove such dowel pins, and
to fit new ones. New dowels may involve enlarging the
damaged hole by drilling and reaming. This is difficult to do at
the customer's place. This is a difficult operation to be done on site, and is most likely to be less than perfect.
On the other hand, it is perfectly possible to use the turret and tool disc without the use of dowels. The friction
joint can easily take up normal cutting loads, including occasional over loads.
Pragati turrets, therefore, do not have a provision of dowelling the body to the base.
TOOL
DISK
3. Fitment of Tool Disc on Turret Flange :
Tool disc is to be fitted on the indexing flange with the help of
clamping bolts, and machine washers. Disc should be angularly
adjusted within the clearance of the bolt holes, to get the correct
centre height of the tool. It should then be firmly clamped by
tightening the bolts. Dowel pins for ensuring the position are not
recommended for the reasons explained earlier.
However, dowel pin can be used for the purpose of alignment, but
it is recommended to remove the pin after clamping the tool disc
in position. There is a provision of soft areas on the indexing flange
to facilitate drilling and reaming for dowel pins.
Bolt holes in the tool disc should be of extra large size to allow for
angular adjustment. Extra thick machine washers should be used
to ensure proper clamping.
TURRET
BODY
FLAT
SEATING
SURFACE
(SCRAPED OR
GROUND)
EXTRA THICK
WASHERS
OVERSIZE
BOLT HOLE
EXTRA
THICK
WASHERS
FIG 3.1
FIG 2.1
Содержание BTP-100
Страница 16: ...FIG 15 3 MAIN SPINDLE ASSEMBLY BI DIRECTIONAL TOOL TURRETS 17...
Страница 17: ...18 BI DIRECTIONAL TOOL TURRETS FIG 15 4B INDEXING DRIVE BTP 125 BTP 100 FIG 15 4A INDEXING DRIVE BTP 80 BTP 63...
Страница 18: ...BI DIRECTIONAL TOOL TURRETS 19 FIG 15 6 MOTOR ASSEMBLY FIG 15 5 COOLANT VALVE ASSEMBLY...