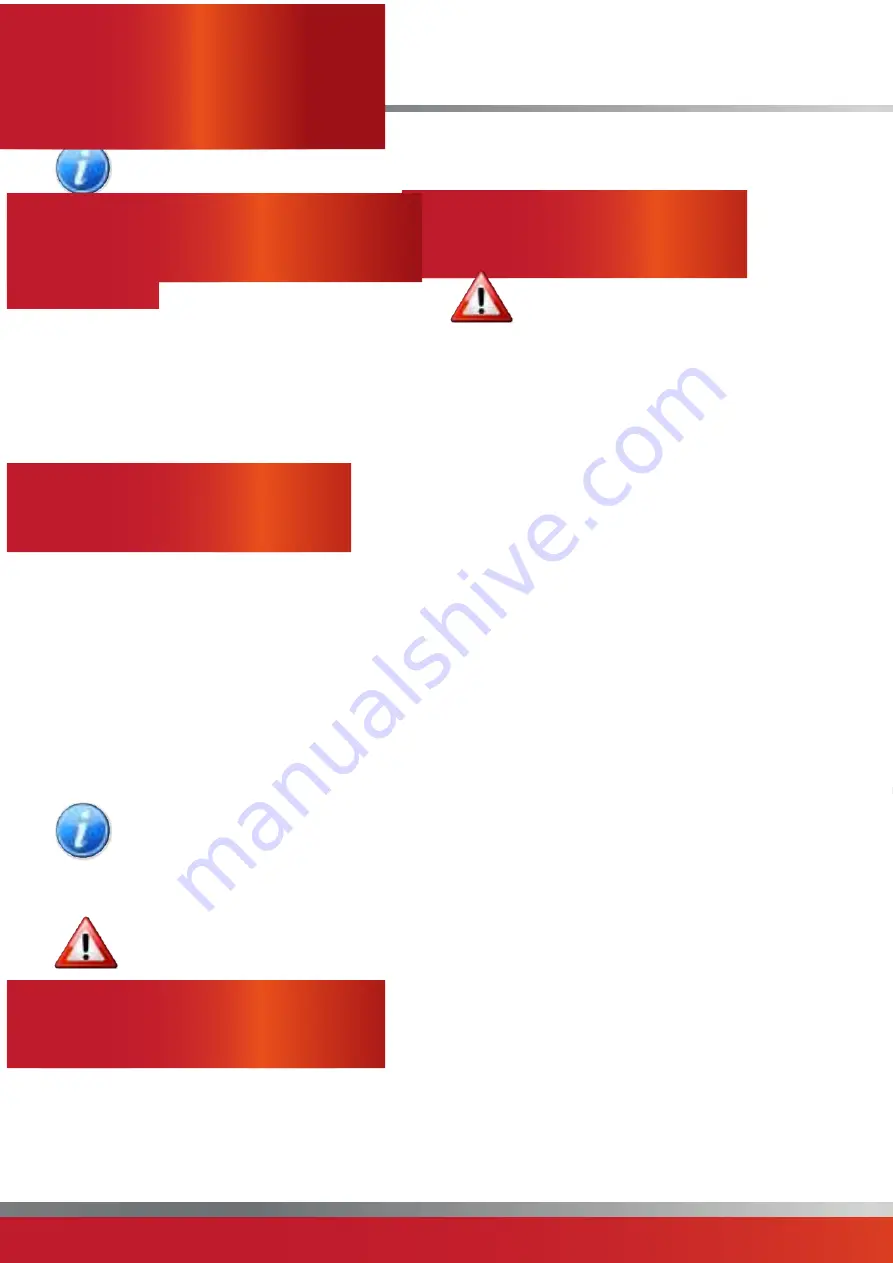
page no. 4 of 36
OUH
Range Users, Installation & Servicing Instructions Doc Ref M105 issue 5.8 Apr 2020.
Complete step 1 above.. Wait approximately 4-5 minutes
for the main air fan of the heater to stop running and the
turn off the oil supplies and electric supplies to the heater.
Important: The heater must NOT be
controlled by switching ON and OFF the
main electrical supply to it.
1) Standard Units
The burner start up sequence will commence when the
controls e.g. Timeclock, room thermostat etc. call for
heat. The burner air fan will run and after a pre purge
period the burner will light.
The heat output will then be
controlled either to high fire or low fire depending on the
requirements of the space being heated and the external
controls fitted.
Approximately 2/3 minutes after the burner lights the
heater fan will automatically start. When the external
controls are satisfied the burner will be turned off and
approximately 4/5 minutes later the heater fan will
automatically stop.
2) Modulating Units
When the burners are alight, the heat output will be
controlled to any point between high and low fire;
depending on the requirements of the space being heated
and the external controls fitted.
3) Summer / Winter Modes
Certain types of external controls will provide for two
modes of operation i.e:
Summer: The heater fan alone will run at the dictate of
the external controls to provide air movement.
Winter: The heater will operate normally.
4) Fan/Limit Stat
The fan and limit controls are mounted on the top of the
air heater.
i) Main Air Fan MAN/Auto
When the white button is pushed to MAN the fan will run
continuously i.e not controlled by any external controls
e.g. Timeclock. When the white button is pulled out the
fan will start and stop automatically in conjunction with
the burner.
ii) Limit Thermostat
This operates if high temperatures within the heater are
detected, the burner is turned off and a red indicator
light on the front of the heater is illuminated. The fault
condition must be identified and rectified and the
thermostat manually reset.
If the heater has not been left operational
proceed as follows.
The following preliminary checks should be made before
lighting the heater(s)
a) Ensure that the ELECTRICAL supply to the heater is
switched OFF.
b) Check that any warm air delivery outlets are open.
c) Check that the thermostat is set.
d) Check that the clock control is set to an ON period.
e) Check that any other controls are calling for heat.
1. Switch on the electrical supply at the isolator.
2. If the Limit indicator light comes on press the reset
switch the electrical box on top of the heater.
3. The burner air fan will run and after a pre purge period
of approximately 30 seconds the ignition spark will be
generated and the oil valve opened. The main burner will
then start.
4. If the main burner fails to light the burner will go to
lockout and the lockout indicator / reset button on the
burner control box will be illuminated. To restart the
burner push the lockout reset button.
NOTE: If the burner fails to light it will go to
lockout and the lockout indicator / reset
button on the burner control box will be
illuminated. To restart the burner push the
reset button.
If the unit will not light after two to three
attempts then shutdown the unit and call in
a service engineer.
1) For Short Periods:
Turn the room thermostat to the OFF, or set to 'Summer
Mode'.
2) For Long Periods: