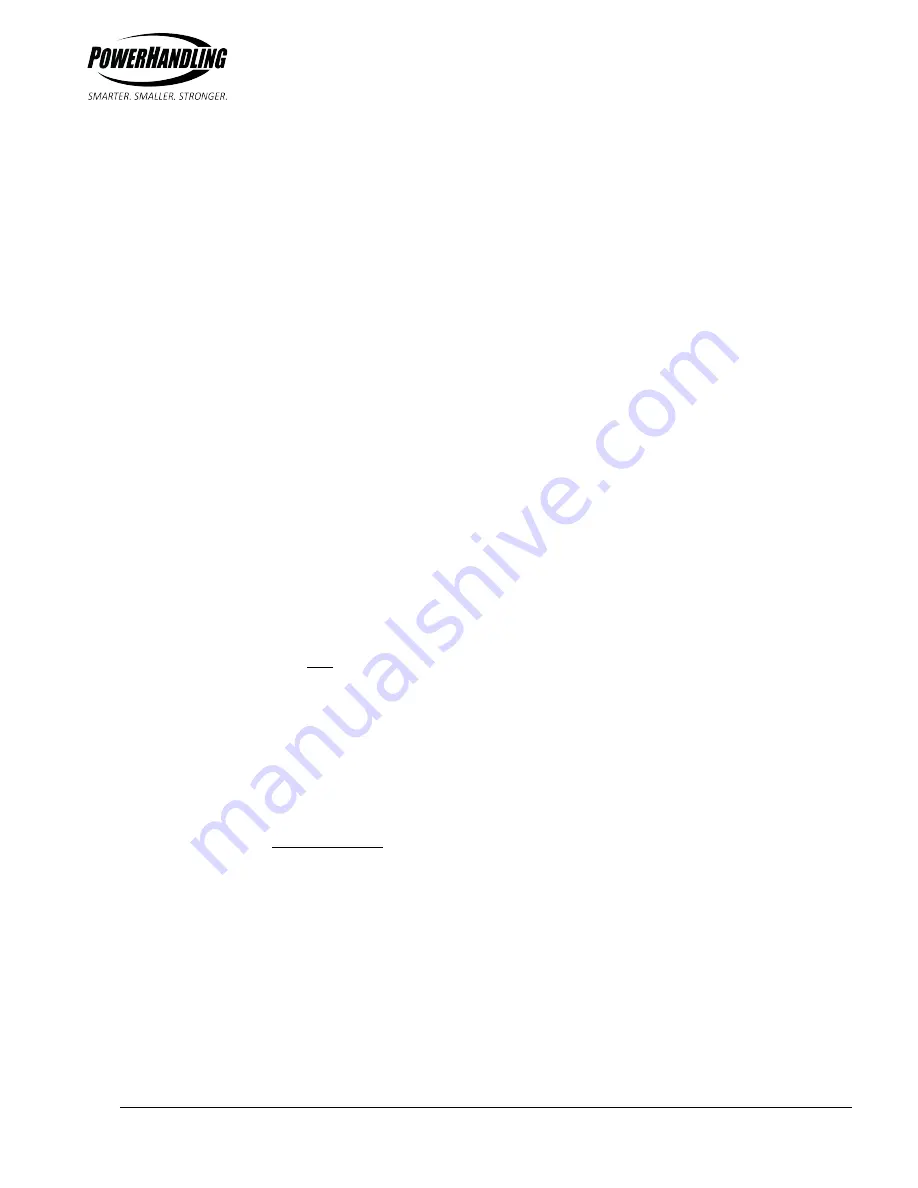
T
T
H
H
E
E
W
W
O
O
R
R
L
L
D
D
L
L
E
E
A
A
D
D
E
E
R
R
I
I
N
N
C
C
O
O
M
M
P
P
A
A
C
C
T
T
M
M
A
A
T
T
E
E
R
R
I
I
A
A
L
L
H
H
A
A
N
N
D
D
L
L
I
I
N
N
G
G
S
S
O
O
L
L
U
U
T
T
I
I
O
O
N
N
S
S
14 of 21
Sept/20
6. The muffler/exhaust is not clear, which causes back-pressure. Look for dry oil deposits
or debris in the muffler material that may be inhibiting the exhausting of air. This may
require cleaning and/or if necessary, replacement of the muffler material
7. The sprockets & chains (if applicable) are in poor condition. There’s too much slack in
the chain (stretched chain) or worn/broken sprocket teeth. If parts are damaged,
replace all sprockets & chains together. Do not replace parts separately.
8. The shaft of the motor-gearbox has been damaged (failed key or keyway).
9. There is another mechanical failure or blockage, such as the drive roller is jammed, the
drive chain has broken, a bearing has seized or failed, etc.
B) GRIP - The drive roller spins against the load instead of moving it
This is typically because of insufficient traction between the drive roller and the load being moved and
can occur for a number of reasons, including:
On a brand new machine, there can be a problem with initial grip until the drive roller
becomes “worn in”. This is a temporary condition that can be remedied quickly. The best
way to “wear in” the drive roller is to use it – on loads that do not slip (e.g. larger diameter).
Using it on rolls or other product that does slip will shine up the urethane surface, delaying
the roller wearing in.
The geometry may be accentuating an existing traction problem. Reference the explanation
in the ‘General Overview’ section describing how too small of a diameter load results in less
of the inertial resistance of the load pushing downward (vertical) instead of backward
(horizontal). A small diameter can be moved if there is sufficient friction contact and a large
diameter load can be moved even with very little friction contact, but the combination of a
small diameter
and
low friction greatly increases the likelihood of slipping. Generally, the
load’s diameter should be > 1000mm (40”).
The drive roller has oil, grease or other low viscosity material embedded into or otherwise
making contact with it, reducing its ability to achieve a friction contact. As the drive roller
makes pressure contact with the support roller while the machine is operating, oil and/or
grease may be picked up from the floor and deposited onto the drive roller in which case the
rollers will need to be cleaned with an appropriate oil dissolving solvent or detergent.
To address low friction issues and reduce the impact of lubricants that end up interfering
with the rollers, the application of Borax (Hydrated Sodium borate – an inexpensive cleaning
agent, ref www.borax.com) to the drive roller can help. All new PowerHandlers and
replacement drive rollers are sent out with Borax already applied.
PowerHandling also offers special low durometer / high grip polyurethane drive rollers for
special applications. These softer rollers will typically not wear as well and so not last as long
at the higher durometer (i.e. harder) polyurethane rollers that PowerHandling provides as
standard.
For more information on servicing your PowerHandler please check the Mechanical
Maintenance Procedures Section.