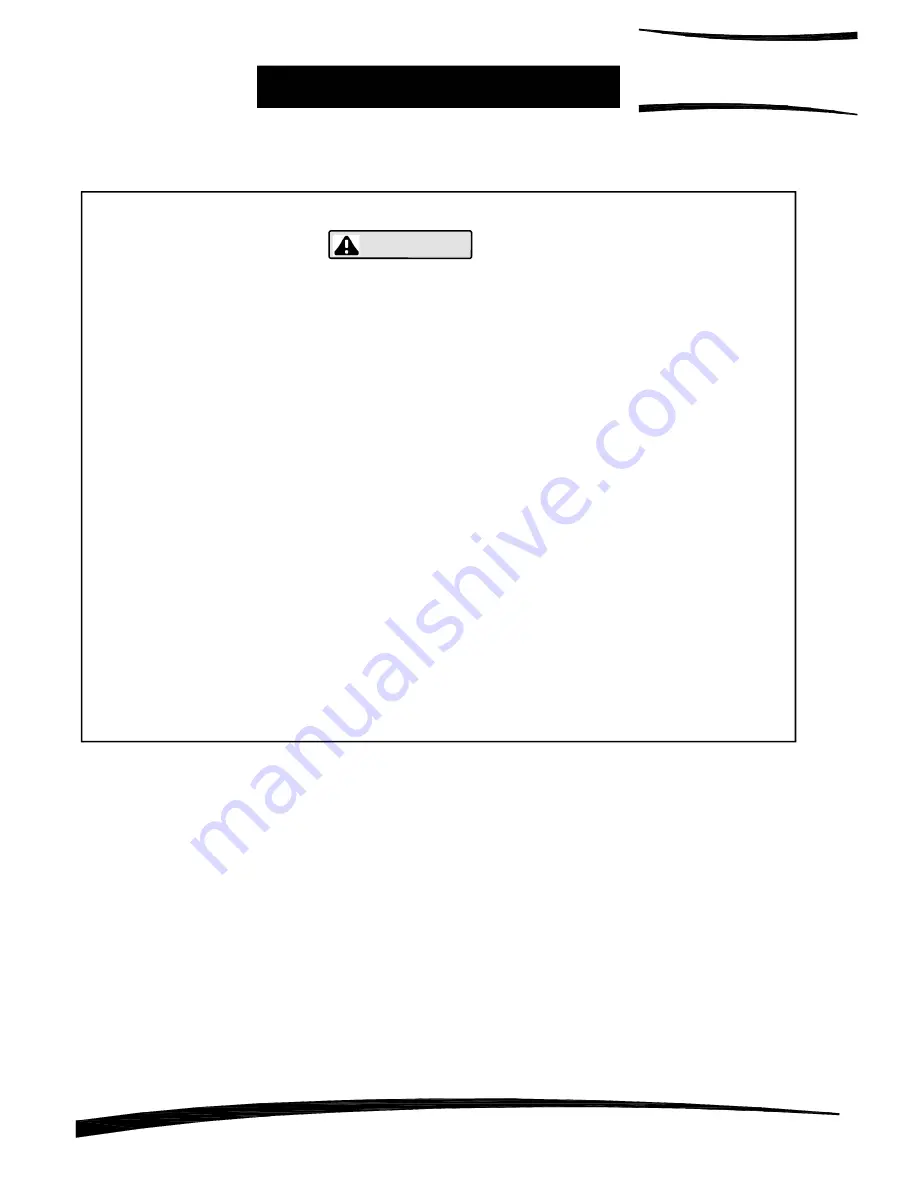
Owner’s Manual
R
PowerBoss, Inc. A Member of the Hako Group ©
2007
PowerBoss
®
CORE 50 Sweeper Scrubber
Page
34
PowerBoss
®
The Power of Clean
SERVICE INSTRUCTIONS (CONTINUED)
FUEL SYSTEM
CHECKING THE LPG FUEL LOCK
1.
Start the engine. Then unplug the wire going to the fuel filter lock. The solenoid
should close, shutting off the fuel supply and stopping the engine.
• If the engine continues to operate, the fuel filter lock should be replaced.
• If the engine stops, the fuel filter lock is operating properly.
2.
With the engine stopped, let the machine stand with the fuel solenoid unplugged.
After 10 minutes, try the starter motor.
• If the engine starts or fires, this indicates a fuel leak has occurred.
Replace the fuel filter lock immediately.
• If the engine simply turns over, this indicates the fuel filter lock is
operating correctly.
1.
Never attempt to perform any service on the equipment or components
until the engine is OFF, the parking brake is LOCKED, and the wheels are
CHOCKED.
2.
Never operate an LPG powered sweeper when any component in the fuel
system is malfunctioning or leaking.
3.
Never bypass safety components.
4.
Replace any defective safety components before operating the sweeper.
5.
During repair or servicing of the fuel system, work in a properly ventilated
area and do not smoke or allow an open flame near the fuel system.
6.
When disconnecting the LPG tank coupling, always wear gloves. LPG fuel
can freeze bare hands.
7.
Under no circumstances should the fuel filter lock be bypassed, except
when testing. After testing, always reconnect lock. Bypassing the fuel
filter lock after testing creates a potential fire hazard.
WARNING