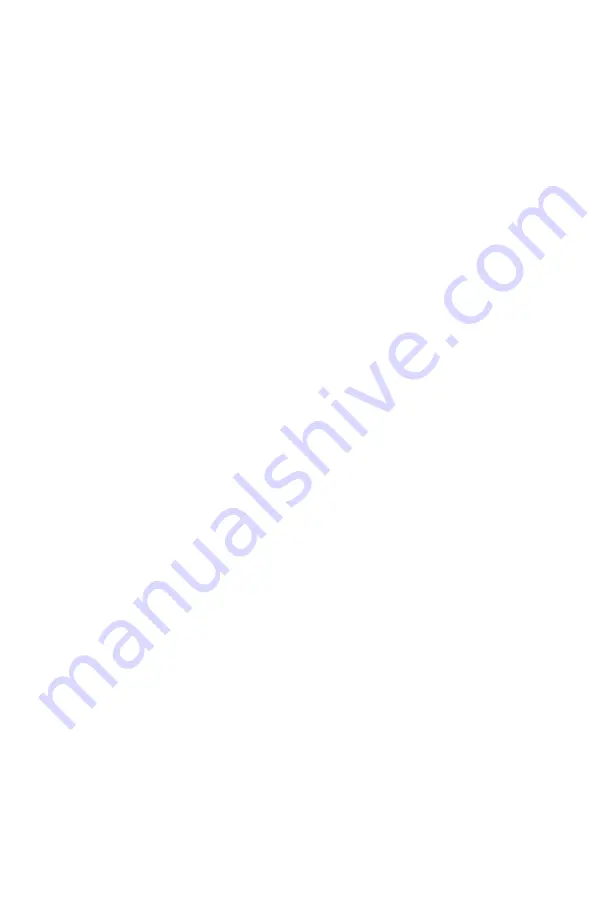
10
SEALED BOX CONSTRUCTION
Building an enclosure for powersports applications requires special care. The material used for enclosure
walls should be solid, dense and free of voids or warps. Your enclosure should be made ¾” or 19mm mate-
rial, Marine Grade Plywood resists warping and rot in harsh water environments. Under no circumstances
it is recommended that particle board be used, it does not hold a screw well and tends to fall apart when
wet.
Corners must be strong and air tight and should not have any air leaks or openings. Joints should be
properly filled with glue that will not crack under high stress or impact. If the integrity of the glue seal
can’t be determined, hot glue or RTV caulking should be used to seal all seams. Fiber reinforced resin may
also be used to form any difficult shapes. However avoid making large panels with resin to eliminate any
chances of box flexing, cracking or ratting under high pressure. Bracing made of 2 x 2” or 2 x 4” should be
liberally applied either inside or outside the cabinet, depending on whether the cabinet is to be permanently
installed or portable.
This principle applies to any walls of the enclosure spanning more than 18” long. Any braces should also
be liberally glued or screwed down on edge. Edge-wise drilled, and countersunk holes through the braces
can be used for #10-2 Flathead wood screws to avoid the use of more expensive lag bolts. The majority
of strength from an enclosure comes from the glue. When using screws be sure to pre-drill holes to avoid
splitting the wood.
WARNING! The use of silicone rubber to seal in a speaker will void the Warranty! If any sealing
is needed in addition to the speaker’s gasket, use caulking cord or vinyl weather strip.