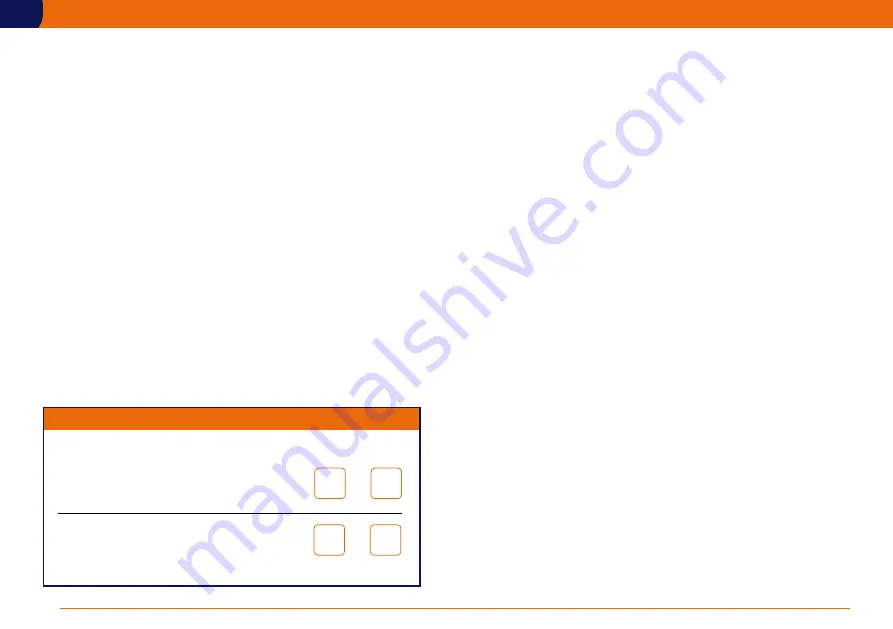
MAINTENANCE PROCEDURES
Six Monthly Checks - LOLER
1. Remove handle cover using suitable security screw tool
and inspect and lubricate gearwheels. Use Omega 73 no. 2 harsh
environment grease or equivalent. Do not use standard gear
grease because it will dry out prematurely and will lead to
premature gear wear. Paint seal screws when refitted.
2. Inspect the drive belt for signs of wear. In order to do this,
remove handle cover as in 1). Stand in the platform and raise
and lower the platform in the normal manner described in
the operating procedures. Whilst the platform is being raised
and lowered, the belt and teeth can be observed through the
inspection panel under the handle cover. Minor scuffing and wear
is acceptable, but there should be no signs of the inner braided
wire or Kevlar cords visible. Paint seal screws when refitted. If
there are any signs of excessive wear, contact the manufacturer or
authorised distributor.
3. The machine should be subjected to the test procedure below.
Note, the dynamic test requirement is achieved by an excess static
load test (190%) which replicates the loads seen during dynamic
movement with 125% SWL due to the necessity to achieve a safe
method of conducting the test.
4. Check the mast interlock is undamaged. Check the casing for signs
of damage and remove the end plate. Check the plunger
is free to move by holding end with long nosed pliers and pulling
outward and then releasing. Ensure plunger springs back freely.
Refit cover and screw. Paint seal screw when refitted.
5. Inspect condition of automatic wheel lock. Look under brush
strip at rear of chassis when platform is elevated so that mast outer
is clear of chassis. Check brake cam plates are undamaged and
that the two attaching screws are tight. With an assistant to lower
the platform, observe the action of the cams and the movement
of the brake pins. Ensure the movement is free and the pins clear
the wheel discs. When the platform is elevated ensure the pins fully
engage the brake discs. Ensure the pockets in the wheels are in
good condition.
6. Check all instruction labels are present and clear. Refer to the key
spare parts.
When replacing components for any reason, only use OEM specification
parts, either supplied from the manufacturer or authorised in writing
by the manufacturer. Warranties and design approvals will be void if
alternative components are fitted.
It is essential to obtain manufacturer’s approval of any alteration
which might affect stability, strength or performance in writing before
proceeding.
When refitting a rear wheel always use a new
cotter pin (4mm
diameter x 32mm A2 stainless steel). NEVER REFIT A USED
COTTER PIN.
10
Test
Procedure
Place machine on test pad.
Dynamic Test EN280 2001 (E) 6.1.4.3
Place 190% SWL (285kg) in platform
when elevated 100mm from rest.
Function Test to full height EN280 2001
(E) 6.1.4.4 with 110% SWL = 165kg.
Whilst lowering release control handle and
ensure lowering stops immediately.
Fail Pass