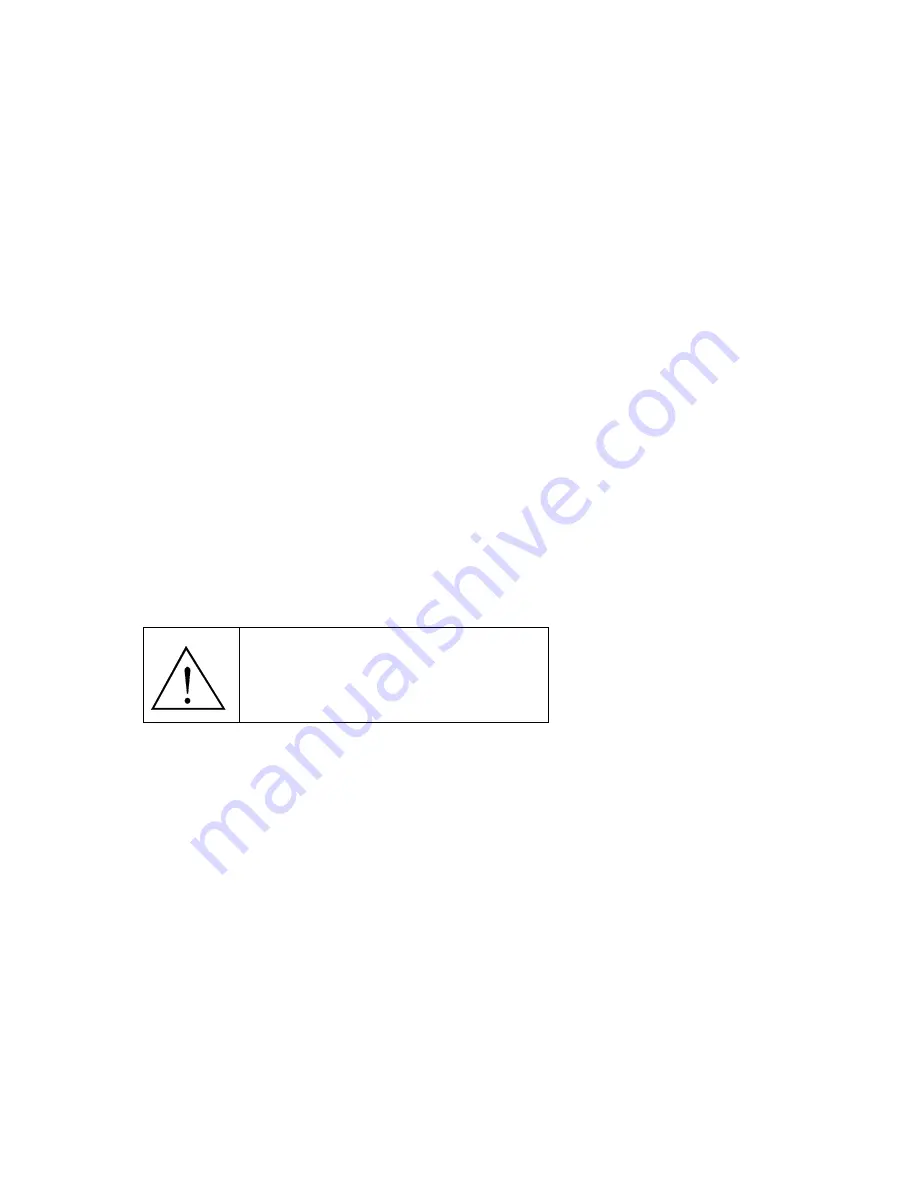
3.2. Power supply connection
The input blocks of the Remote Heat Station should be bolted onto the output of an Induction
Heating power supply. The RHS is rated for up to 40kW at up to 400kHz. Consult the
manufacturer for use beyond those limits.
3.3. Cooling water
Cooling water for the Remote Heat Station is often supplied through the input blocks from an
induction power supply. If this is not the case, remove the hoses from the input blocks and
connect them to a water supply such as a recirculating cooler.
3.4. Control wiring
The Remote Heat Station comes with control wires to light the LED when the heat cycle is on.
These wires connect to a plug on the side of the power supply. It is not necessary to use this
control wiring. For many operations, initiating the heat cycle from the power supply controls is
more convenient.
4. Load station tuning.
WARNING:
Make sure that power
supply is turned off before adjusting
heat station components.
This section describes the procedures for tuning the heat station so that full power will be
obtained at the desired frequency. It is very important to match the resonant frequency of the
Remote Heat Station to that of the power supply. This gives minimum current in the RHS
cable, and highest power delivered to the load.
4.1. Loading capacitors.
Apply thermal grease to both tabs of each capacitor and install as indicated in Figure 2 on
page 7. Insert and tighten the mounting screws (four per capacitor). Capacitors can be
mounted to both sides of the capacitor rails, and optimum current sharing is achieved when
capacitors are directly opposing each other on the capacitor rail. This is particularly important
for the two capacitors closest to the work coil.
6