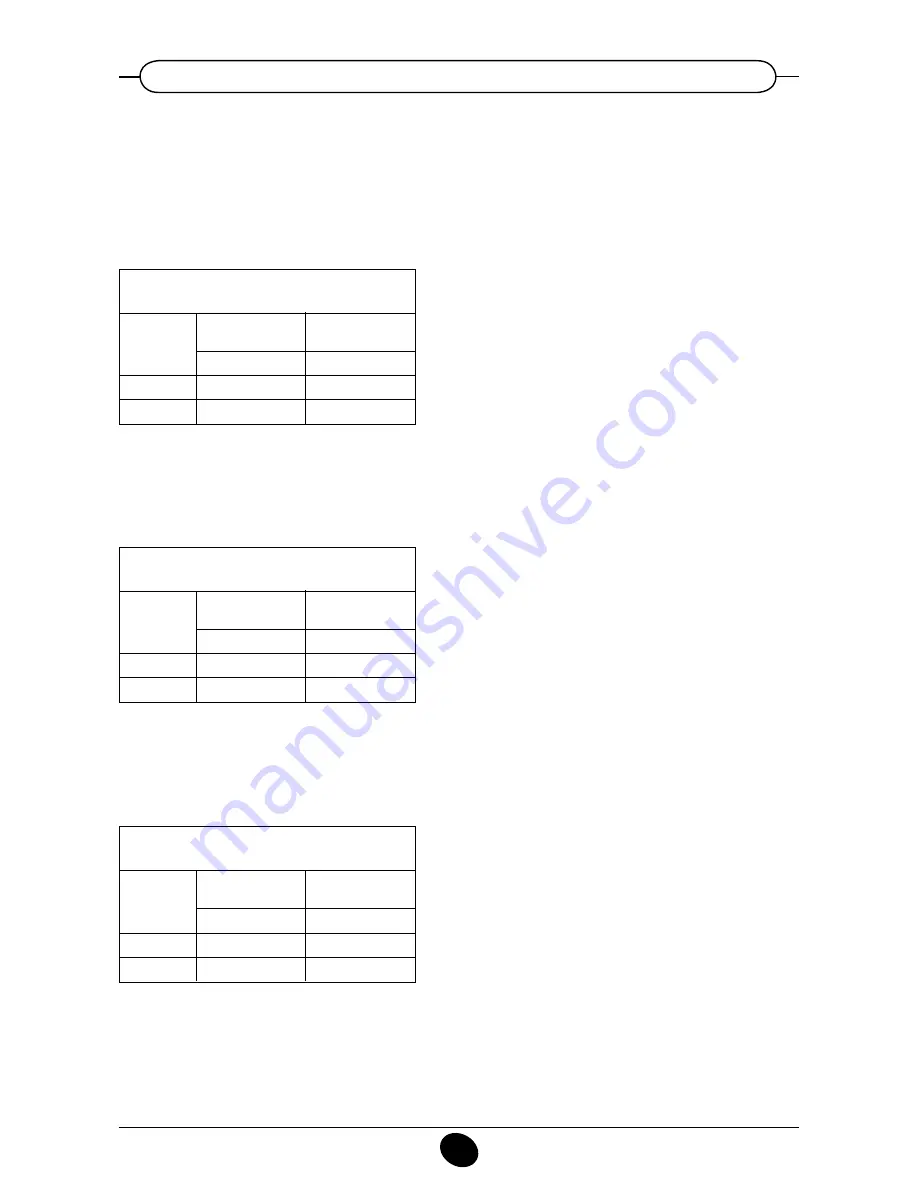
18
91.7.1 - GB/IE
InstructIons pErtaInInG to thE InstaLLEr
To ensure the correct rated heat output to the maximum and minimum heat input, it is necessary to update
the speed (rpm) of the fan, it depends on the length of the flue (par. 12), in accordance with the installation of
flue and air pipes as indicated in the tables below. The factory-set value is referred to the minimum length of
flue pipe (0÷4 m for concentric, 0÷20 m for twin). To carry such updating, changing the speed of the fan (rpm)
at the maximum and minimum heat input, refer to par. 16.
ConCentriC PiPe ø 80/125
(C13-C33-C43)
Pipes length
(m)
(*) 0 - 4
5 - 10
Parametres
H536-H613
Max heat output (rpm)
5500
5900
Parametres
H612
Min heat output (rpm)
1900
2100
wH 50
ConCentriC PiPe ø 80/125
(C13-C33-C43)
Pipes length
(m)
(*) 0 - 4
5 - 10
Parametres
H536-H613
Max heat output (rpm)
5600
6000
Parametres
H612
Min heat output (rpm)
1650
1800
wH 60
ConCentriC PiPe ø 80/125
(C13-C33-C43)
Pipes length
(m)
(*) 0 - 4
5 - 10
Parametres
H536-H613
Max heat output (rpm)
6000
6500
Parametres
H612
Min heat output (rpm)
1850
2100
wH 70
12.5 fan rpm updating depending on flue lengtH (e.g. figure 7)
(*) Default setting parameters
(*) Default setting parameters
(*) Default setting parameters