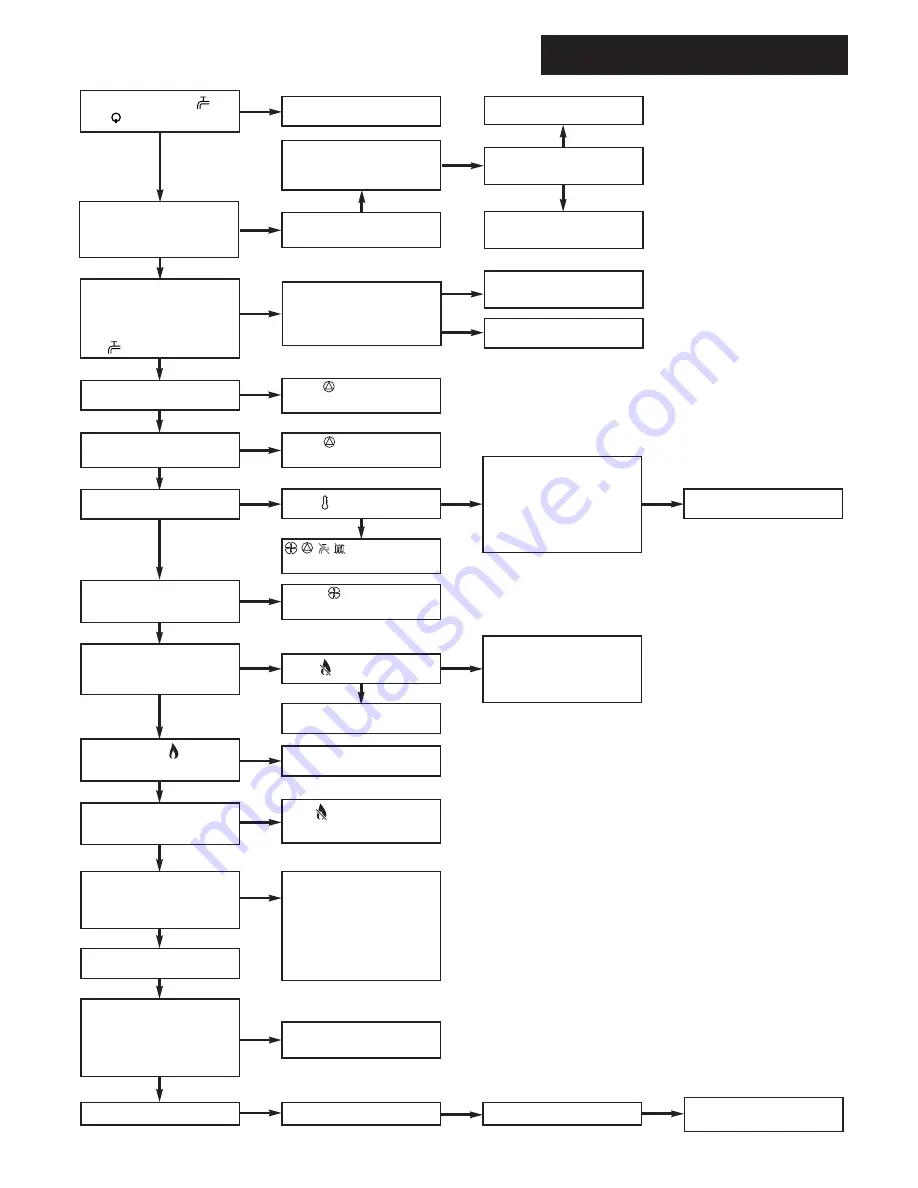
49
© Baxi Heating UK Ltd 2007
16.0
Fault Finding
Domestic Hot Water -
Follow operational sequence
Turn selector to
neon illuminated
Primary flow switch operated
Fan runs at max speed
Pump runs
Turn thermostat to max.
Open DHW tap fully. DHW
flow switch operated
Primary water is diverted
from CH system to DHW
heat exchanger and flow
microswitch operated
neon illuminated
Continuity across DHW flow
microswitch terminals and
PCB - A5 connector
terminals 5 & 6
Air pressure switch proved
neon flashing
Burner on neon
illuminated
Spark at ignition electrodes
for up to 10 seconds
Go to section ‘A’
neon flashing
Go to section ‘B’
neon flashing
Go to section ‘C’
Go to sections ‘J’ & ‘M’
neons flashing
Go to section ‘D’
Replace PCB
Turn the selector to the reset
position. If the light does not
extinguish go to section H &
K
Go to section ‘F’
neon flashing
Go to sections ‘I’ & ‘L’
DHW flow valve
senses no flow.
Primary water diverted to
CH system. DHW flow
switch released off
Close DHW tap
Burner goes out
Diverter valve spindle
assembly faulty
Pump stops
Operation sequence correct
neon flashing
Turn selector to reset
position. If regular resetting is
required or appliance still
does not operate
investigation is necessary
neon flashing
Go to section ‘E’
Burner extinguishes
after 10 seconds
YES
YES
YES
YES
YES
YES
YES
YES
YES
YES
YES
YES
YES
YES
YES
YES
NO
Fan stops
NO
YES
YES
YES
YES
NO
NO
DHW flow rate more than
2.5l/min.
Is mains water
filter and differential
assembly clean?
DHW flow valve diaphragm
damaged
DHW flow valve rod
obstructed
Replace DHW flow
microswitch
Replace PCB
Replace diaphragm
NO
NO
NO
YES
NO
NO
NO
NO
NO
NO
NO
NO
Reduce the DHW flow rate.
If burner does not modulate
clean DHW temperature
sensor and DHW heat
exchanger. If modulation
does not occur go to section
‘G’
Burner output modulates to
maintain temperature set at
thermostat
NO
NO