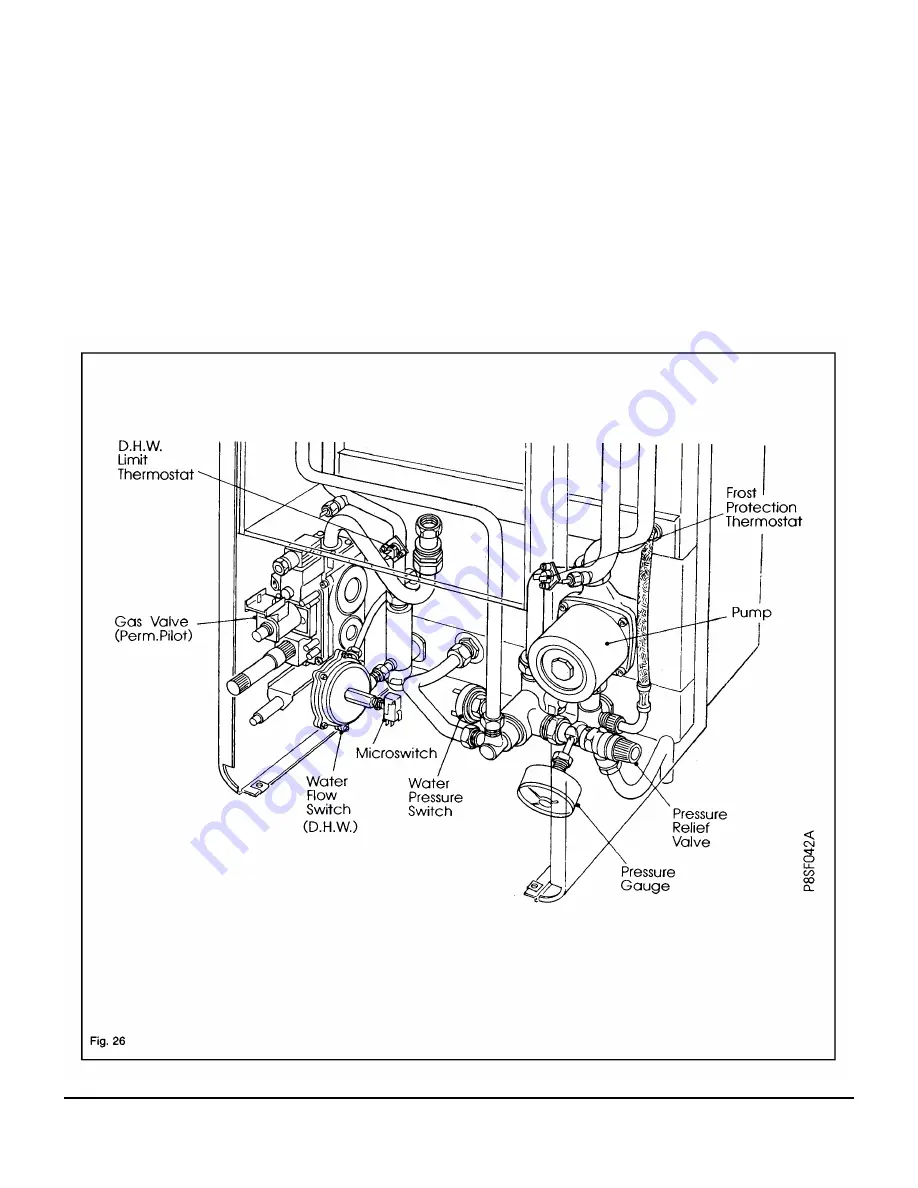
6. Component Replacement - Page 30
WARNING:
Before attempting to remove any component from this appliance, first disconnect the mains electricity supply by
removing the plug from the wall socket or by switching off the appliance at the external isolating switch.
Note:
The appliance
stand-by switch must not be used as the means of isolating, as this switch does leave parts of the appliance electrically live.
IMPORTANT:
After removal or replacement of any gas carrying components a test for gas soundness must be made.
Notes
: The appliance gas supply should be isolated at the boiler gas service cock (one quarter turn of square spindle).
The Central Heating and Domestic Hot Water circuits can similarly be isolated at their respective valves. A drain
point is provided in the appliance heating circuit under the pump manifold and the cold water inlet isolating valve
also incorporates a drain screw. Use a suitable tube when draining to direct water away from the appliance.
When removing any water carrying components suitably protect the control box from accidental spillage.
Before removing any component from the central heating circuit on the appliance, reduce the pressure by closing
the isolating valves and opening the pressure relief valve.
Содержание 80e
Страница 5: ...Optional Extras Page 5 ...
Страница 6: ...Optional Extras Page 6 Installation instructions included as necessary with each kit ...
Страница 7: ...Optional Extras Page 7 Installation instructions included as necessary with each kit ...
Страница 12: ......
Страница 28: ...Routine Maintenance Page 27 ...
Страница 30: ...Routine Maintenance Page 29 ...
Страница 34: ...Component Replacement Page 33 ...
Страница 35: ...Component Replacement Page 34 ...
Страница 43: ...7 1 Control Flow Sequence Permanent Pilot Page 42 ...
Страница 44: ...7 2 Functional Flow Permanent Pilot Page 43 ...
Страница 45: ...7 3 Fault Finding Permanent Pilot Page 44 ...
Страница 46: ...7 4 Electrical Diagram Permanent Pilot Page 45 ...
Страница 47: ...8 1 Control Flow Sequence Electronic Page 46 ...
Страница 48: ...8 2 Functional Flow Electronic Page 47 ...
Страница 49: ...8 3 Fault Finding Electronic Page 48 ...
Страница 50: ...8 4 Electrical Diagram Electronic Page 49 ...
Страница 51: ...9 Short List of Spares Page 50 s ...