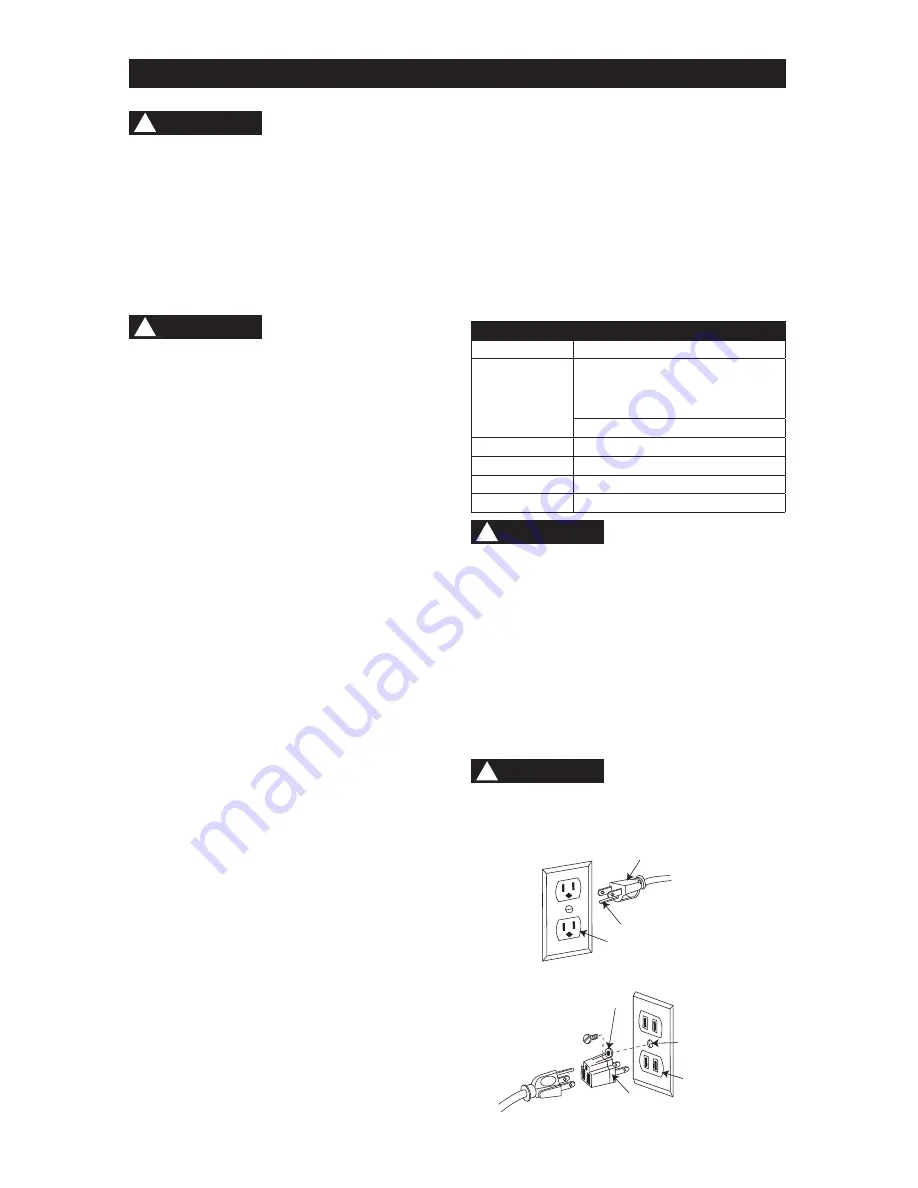
6
ELECTRICAL REQUIREMENTS AND SAFETY
POWER SUPPLY AND MOTOR SPECIFICATIONS
To avoid electrical hazards, fire hazards,
or damage to the tool, use proper circuit
protection. Use a seperate electrical circuit for
your tool. Your saw is wired at the factory for
120 V operation. Connect to a 120 V, 10 Amp
circuit and use a 10 Amp time delay fuse or
circuit breaker. To avoid shock or fire, if power
cord is worn, cut, or damaged in any way, have it
replaced immediately.
GROUNDING INSTRUCTIONS
This tool must be grounded while in use to
protect the operator from electrical shock.
IN THE EVENT OF A MALFUNCTION OR
BREAKDOWN,
grounding provides a path of least
resistance for electric currents and reduces the
risk of electric shock. This tool is equipped with an
electrical cord that has an equipment-grounding
conductor and a grounding plug. The plug must be
plugged into a matching receptacle that is properly
installed and grounded in accordance with all local
codes and ordinances.
DO NOT MODIFY THE PLUG PROVIDED.
If it will
not fit the receptacle, have the proper receptacle
installed by a qualified electrician.
IMPROPER CONNECTION
of the equipment
grounding conductor can result in risk of electric
shock. The conductor with the green insulation
(with or without yellow stripes) is the equipment
grounding conductor. If repair or replacement of
the electrical cord or plug is necessary, do not
connect the equipment grounding conductor to a
live terminal.
CHECK
with a qualified electrician or service person
if you do not completely understand the grounding
instructions, or if you are not certain the tool is
properly grounded.
USE only 3-wire extension cords that have
three-pronged grounding plugs with three-pole
receptacles that accept the tool’s plug. Repair or
replace damaged or worn cords immediately.
Use a separate electrical circuit for your tool. This
circuit must not be less than #16 wire and should
be protected with a 10 Amp time lag fuse. Before
connecting the motor to the power line, make sure
the switch is in the off position and the electric
current is rated the same as the current stamped on
the motor nameplate. Running at a lower voltage will
damage the motor.
GUIDELINES FOR EXTENSION CORDS
USE THE PROPER EXTENSION CORD.
Make
sure your extension cord is in good condition. Use
an extension cord heavy enough to carry the
WARNING
!
WARNING
!
current your product will draw. An undersized cord
will cause a drop in line voltage resulting in loss of
power, overheating and burning out of the motor.
The table below shows the correct size to use
depending on cord length and nameplate ampere
rating. If in doubt, use the next heavier gauge. The
smaller the gauge number, the heavier the cord.
Make sure your extension cord is properly wired
and in good condition. Always replace a damaged
extension cord or have it repaired by a qualified
technician before using it. Protect your extension
cords from sharp objects, excessive heat and damp
or wet areas.
This tool is for indoor use only. Do not expose to
rain or use in damp locations.
This tool is intended for use on a circuit that has
a receptacle like the one illustrated in Fig. 1.
Fig. 1 shows a three-pronged electrical plug and
receptacle that has a grounding conductor. If a
properly grounded receptacle is not available, an
adapter (Fig. 2) can be used to temporarily connect
this plug to a two-contact grounded receptacle. The
adapter (Fig. 2) has a rigid lug extending from it that
MUST be connected to a permanent earth ground,
such as a properly grounded receptacle box.
In all cases, make certain the receptacle is
properly grounded. If you are not sure, have a
qualified electrician check the receptacle.
MINIMUM GAUGE FOR EXTENSION CORDS (AWG)
Ampere Rating
Total Length of Cord
More
Than
Not More
Than
120 V 25 50 100 150 ft.
(7.62 15.24 30.48 45.72 m)
240 V 50 100 200 300 ft.
(15.24 30.48 60.96 91.44 m)
AWG - American Wire Gauge
0
6
18 16 16 14
6
10
18 16 14 12
10
12
16 16 14 12
12
16
14 12
Not Recommended
WARNING
!
CAUTION
!
Fig. 1
Fig. 2
Three-Pronged Plug
Grounding Prong
Properly Grounded
Three-Pronged Receptacle
Grounding Lug
Make sure this
is connected to
a known ground.
Two-Pronged
Receptacle
Adapter