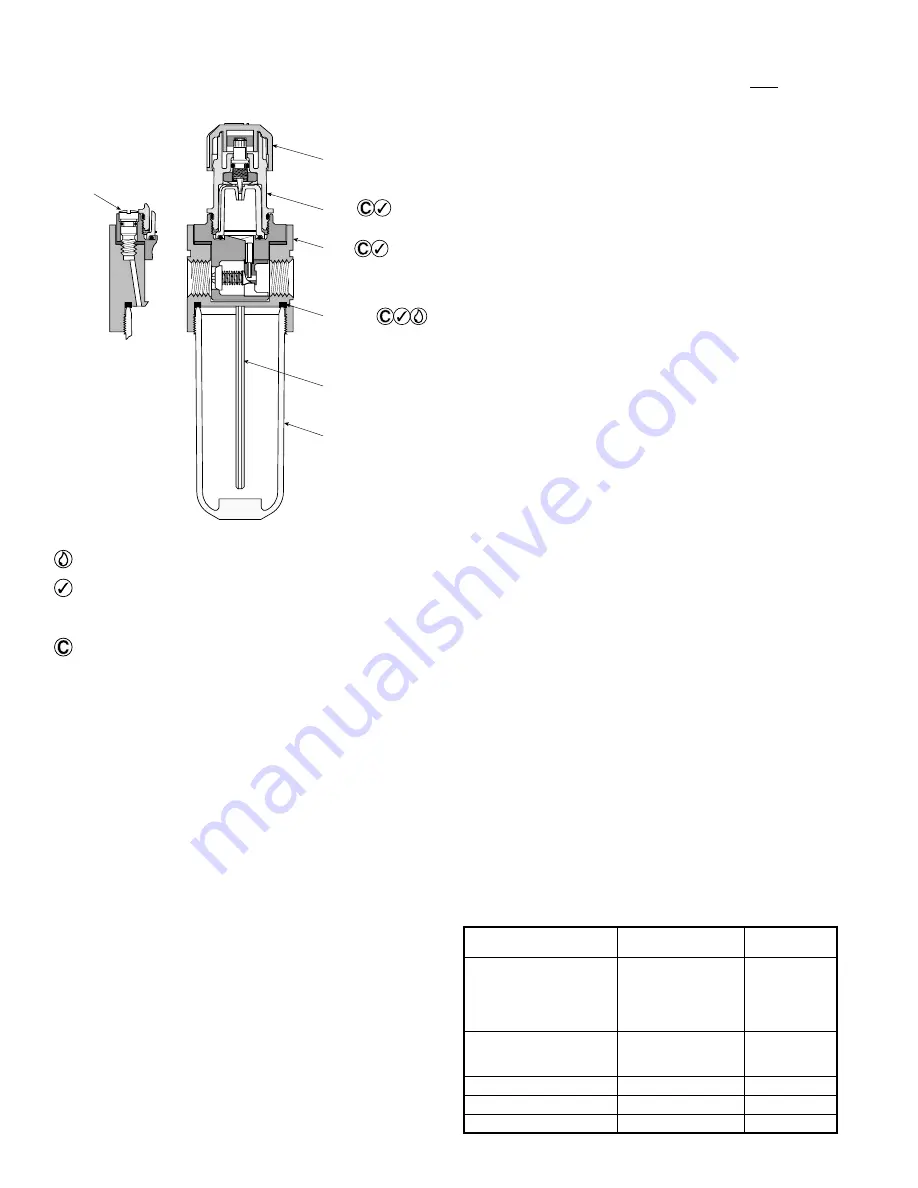
L35 Lubricator
IS-L35
Installation
1. The lubricator should be installed with reasonable
accessibility for service whenever possible – repair service
kits are available. Keep pipe or tubing lengths to a minimum
with inside clean and free of dirt and chips. Pipe joint
compound should be used sparingly and applied only to
the male pipe – never into the female port. Do not use
PTFE tape to seal pipe joints – pieces have a tendency to
break off and lodge inside the unit, possibly causing
malfunction. Also, new pipe or hose should be installed
between the filter and equipment being protected.
2. The upstream pipe work must be clear of accumulated
dirt and liquids.
3. Select a lubricator location as close as possible to the
equipment being protected and upstream of any pressure
regulator.
4. Install lubricator so that air flows in the direction of arrow
on body.
5. Install lubricator vertically with bowl drain mechanism at
the bottom.
Lightly grease with provided lubricant.
Inspect for nicks, scratches, and surface imperfections.
If present, reduced service life is probable and future
replacement should be planned.
Clean with lint-free cloth.
Operation and Service
1. Filling — The inlet pressure of the lubricator must be turned
off and depressurized before the Fill Plug is removed. Turn
counterclockwise to remove. Fill to within 1/4" from top of
bowl or to top of the sight glass on the bowl.
Suggested lubricant: F442
Petroleum based oil of 100 to 200 SSU viscosity at 100°F
and an aniline point greater than 200°F. (Mobil DTE24
and Sun Company Sunvis 932 are good examples). Do
not use oils with adhesives, compound oils containing
solvents, graphite, detergents or synthetic oils.
2. Replace the Fill Plug (by turning clockwise) and seat
firmly. Excessive torque is not required. Turn on air supply,
if leakage occurs,
DO NOT OPERATE
— conduct repairs
again. The lubricator is now ready for setting.
3. Oil delivery adjustment — To adjust oil delivery, turn
Adjustment Knob on top of the lubricator.
Leaner — Clockwise
Richer — Counterclockwise
By counting the number of drops per minute in the Sight
Dome, you can adjust to your requirements. Generally,
one drop per minute downstream for every
10 - 15 SCFM flow is satisfactory. 25 drops per minute
equals one (1) ounce per hour - volume of oil passing
through the Sight Dome.
NOTE:
This is a constant density type lubricator which
delivers a constant ratio of oil air flow. Therefore, if air
flow increases or decreases, oil delivery will be
adjusted propor tionately. ONLY IF A DIFFERENT
RATIO IS DESIRED SHOULD YOUR ADJUSTMENT KNOB
SETTING BE CHANGED AFTER YOUR INITIAL SETTING.
4. Cleaning — Erratic lubricator operation or loss of lubrication
is almost always due to dirt (rust, pipe tape, etc.) in the
needle valve or venturi area. To clean, shut off and vent all
air line pressure to the unit being cleaned. In most cases
cleaning is needed only in the oil metering area. Pull off
Adjusting Knob and remove Sight Dome Assembly. Make
sure hole in Body Seat and Drip Spout is clear. Remove
Bowl. Clean parts with soapy water or denatured alcohol
but do not use denatured alcohol on plastic bowl,
sight dome or sight gauge
. If using compressed air to
blow dry, be sure to wear appropriate eye protection.
5. After servicing, apply system pressure and check for air
leaks. If leakage occurs,
Do Not Operate
— conduct
servicing again.
Dip Tube
Bowl Seal
Bowl
(Hand Tighten)
Body
Adjustment
Knob
Fill Plug
Sight
Dome
Kits Available
Product
Bowl
Description
Number
Type
Bowl
Polyurethane
BKL35A
A
Zinc
BKF35D
D
Zinc with Wrap
Around Sight Gauge
BKL35W
W
Repair Kit
Tamper-resistant
RKL100
A, D, W
Sight Dome Repair Kit
Adjusting Knob
L100-0726P
—
Dip Tube
L30-0741
—
Bowl Seal
GSK-504Z101
A, D, W