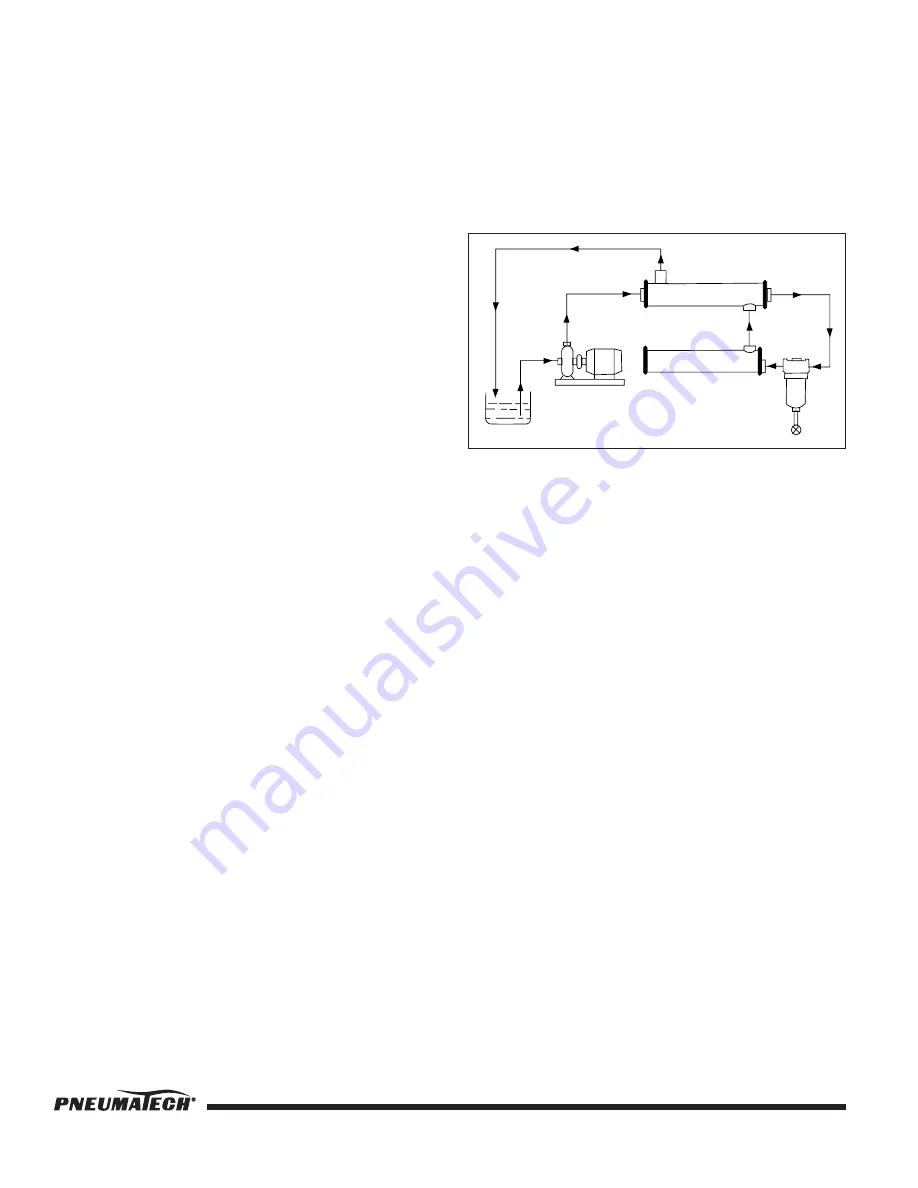
10
Pub. No. OM-A-75 REV. 4 — March 2006
MAINTENANCE
AIR DRYER MAINTENANCE
The dryer is factory tested before shipping. All controls are
calibrated for automatic operation. If the dryer is installed
in clean surroundings, within the temperature limits of the
specified ambient, the dryer will run trouble-free for a very
long time. Routine maintenance procedures recommended
are the following:
1.
Checking the fan motor(s) for proper operation to
maintain the cooling air to be drawn through the
condenser and blown over the refrigerant
compressor. If the dryer is equipped with condenser
ambient filters, check, clean or replace as needed to
maintain the proper air flow through the condenser.
Dirty ambient filters will reduce the air flow through
the condenser, and trip the compressor “off” at the
overload control.
2.
For dryers without ambient filters, clean the
condenser periodically to maintain the proper heat
transfer on the condenser coil. Dirty condenser will
raise the head pressure of the refrigeration system
and trip the compressor “off” at the overload control.
Running the compressor on high head pressures may
cause premature failures. Check the ambient
temperature limits to be maintained at the
installation.
3.
Check and clean water-cooled condensers for dirt,
scale and sludge buildup every year or as needed.
Cooling tower water condensers may need cleaning
more often if the water is not properly treated.
4.
Check the suction pressure gauge. Reading should
be within the specified range after a few minutes of
start-up. Suction pressure below the range will cause
freeze-up inside the air system, increasing the
pressure drop across the air dryer. Suction pressure
above the range will reduce the refrigeration cooling
capacity.
5.
Check the pressure drop across the air dryer at full
capacity flow. If it is higher than specified value
(normally 5 PSI or less), consult factory. If pressure
drop increases over years of operation, it may be
due to particulate buildup from air compressor
intake. In that event, back-flush the dryer with any
MILD DETERGENT
. See Figure 2.
To back-flush, disconnect air dryer, plug the drain line and
fill the air system with the detergent water solution. Hold it
for 4-6 hours. Circulate the detergent from air outlet to air
inlet with a pump. Flush the system with warm water. If
pressure-drop still exists, contact factory.
FIGURE 2 — BACK FLUSH FLOW DIAGRAM
AUTOMATIC DRAINS
The recommended settings for the drain time is determined
by the moisture load. The cycle time should be adjusted to
approximately 3 to 4 minutes. The drain time should be set
so the drain expels all of the liquid and then a short burst
of air.
Periodically check the automatic drains for proper
drainage. If the drains are not functioning, the condensed
moisture will be re-entrained downstream of the air dryer.
Float operated automatic drains need periodic cleaning
with soap and water to remove solids from the valve seat.
If the valve is stuck open, clean with soap and water and
then use compressed air to clean the valve seat. Electronic
solenoid operated drains may be manually tested
periodically for proper operation.
AIR OUTLET
AIR INLET
A/A HEAT EXCHANGER
A/R HEAT EXCHANGER
SEPARATOR
MILD DETERGENT
CIRCULATING
PUMP
PLUG