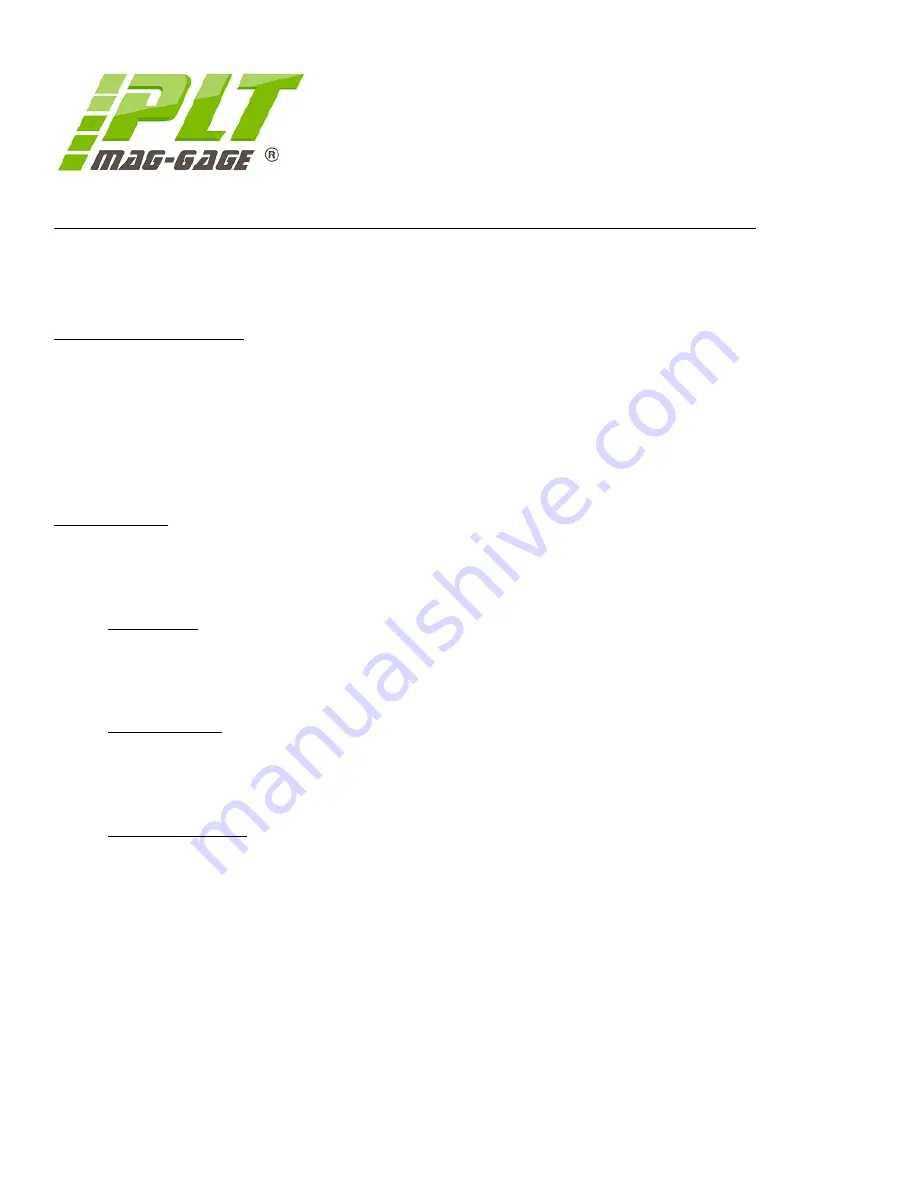
Process Level Technology, Ltd.
MAG-GAGE
®
OPS-001 Revision 6
Page
21
of
30
December 17, 2018
Installation, Operation and Maintenance Instructions
Section 2.10.0. - Terms and Condition of Sale
2.10.1. INTRODUCTION
All orders should be entered to the following address:
Process Level Technology, Ltd.
888 Clear Creek Ave.
League City, Texas 77573
PH# (281) 332-MAG1(6241), Fax# (281) 332-0232
2.10.2. TERMS
The payment terms are
Net 30 days
to approved customers. Sales representatives may assume collection
responsibility for new accounts at their discretion. Late charges will be added at the rate of 1.50% per month.
2.10.3.
SHIPMENT
All shipments will be
F.O.B. factory location, Houston, Texas
, via motorfreight insured. Freight charges are
normally prepaid and added to invoice unless specified otherwise.
2.10.4.
RESTOCKING
Every magnetic level gage is designed and manufactured to exact customer specifications. As a result, there will
be
no restocking option
after shipment is made.
2.10.5.
CANCELLATION
Cancellation charges after order placement will be at the discretion of Process Level Technology, Ltd. and
dependent upon production phase of the product.
Pneumatic Level Control