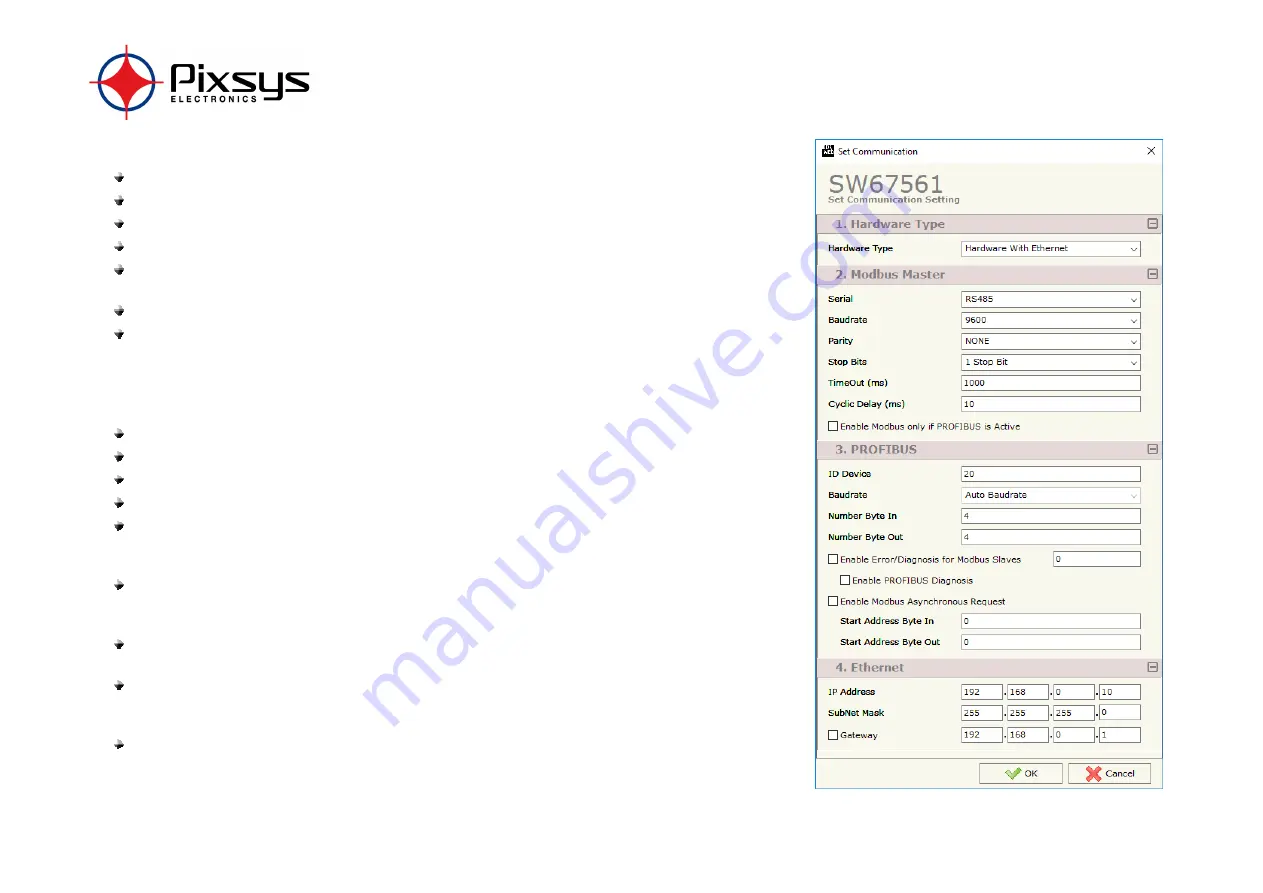
pag. 16
The means of the fields for “Modbus Master” are:
In the field “
Serial
” is possible to select the serial line used for Modbus. Please select “RS485”;
In the field “
Baudrate
” pease define the baudrate for the serial line;
In the field “
Parity
” pease select the parity of the serial line;
In the field “
Stop Bits
” pease select the Stop Bits of the RS485;
In the field “
TimeOut (ms)
” insert the maximum time that the converter attends for the answer from the
slave interrogated (1000mS is the default value);
In the field “
Cyclic Delay (ms)
” insert the delay between two requests (10mS is the default value);
If the field “
Enable Modbus ony if PROFIBUS is Active
” is checked, the converter do the Modbus
requests only if PROFIBUS connection is established; otherwise the requests are made also if PROFIBUS is
not operational. (disabled is is the default value);
The means of the fields for “PROFIBUS” are:
In the field "
ID Device
" insert the address of the PROFIBUS side;
In the field "
Baudrate
" the baudrate for the PROFIBUS is defined, please leave it as AUTO;
In the field "
Number Byte IN
" the number of byte from the slave PROFIBUS to the converter is defined;
In the field "
Number Byte OUT
" the number of byte from the converter to the slave PROFIBUS is defined.
If the field “
Enable Error/Diagnosis for Modbus Slaves
” is checked, the converter can advice a problem
with one or more devices in Modbus network. In the field on right is necessary to insert the start byte
address of array OUT where is saved the Diagnosis;
If the field “
Enable PROFIBUS Diagosis
” is checked, the converter use the Diagnosis to show an error of
one or more Modbus device. (The “Enable Error/Diagnosis for Modbus Slaves” must be selected for enable
this option);
If the field “
Enable Modbus Asynchronous Requests
” is checked, is possible to send a Modbus Request
using some bytes of the PROFIBUS to controll the requests;
In the field “
Start Address Byte IN
” the starting address where the gateway send to the PROFIBUS master
the state of Modbus request (for more info see the chapter “Async Remote Request”). Remember, there are
4 bytes of state of the modbus request;
In the field “
Start Address Byte OUT
” the starting address where the PROFIBUS master send to the
gateway the parameters of the Modbus Request (for more info see the chapter “Async Remote Request”).
Remember, there are 8 bytes of parameters for the modbus request.
Содержание CNV510-PBUS-RTU-A
Страница 1: ...pag 1 CNV510 PBUS RTU A Software version SW67561 Profibus Slave Modbus Master Converter User Manual...
Страница 4: ...pag 4 MECHANICAL DIMENSIONS...
Страница 5: ...pag 5 EXAMPLE OF CONNECTION...
Страница 6: ...pag 6 CONNECTION SCHEME...
Страница 7: ...pag 7 POWER SUPPLY...
Страница 29: ...pag 29 5 Load the configuration into the PLC...