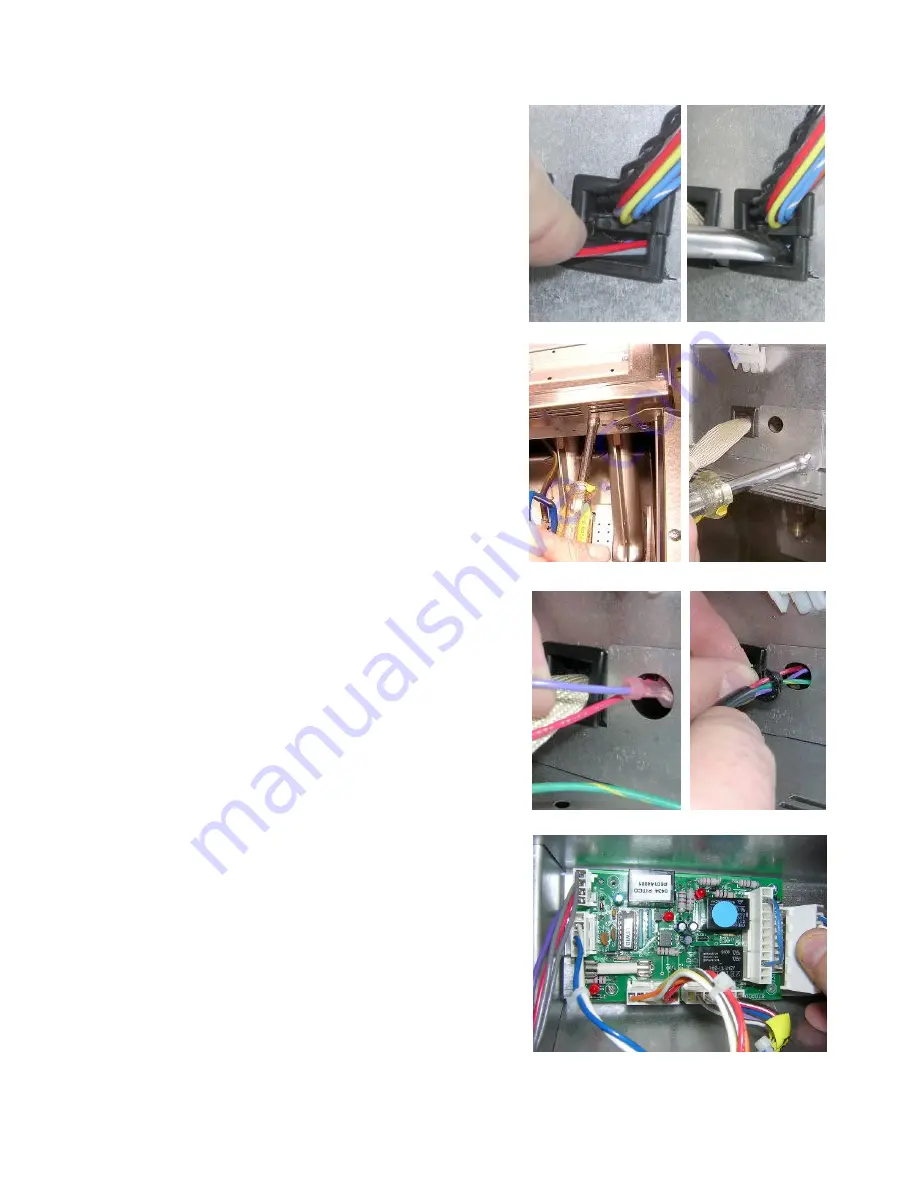
L80-029 Rev 5 10/07 8
e. If the appliance you are upgrading does NOT have a
Solid State Control, proceed to step f in this section.
If the appliance that you are upgrading has a Solid
State Control, feed the other ends of the SCBS
Harness through the unused portion of the strain
relief holding the Solid State Control Harness and
proceed directly to step h in this section.
NOTE:
If needed, you can carefully nudge open the
area in the strain relief with a screwdriver to make
additional room to insert the SCBS harness. Take
care not damage the harness during this procedure.
f.
Using a 5/16 nut driver, remove the two screws on
the underside of the front panel that hold the slotted
bottom on. Remove the slotted front panel bottom;
this will allow easier access to the cable retainer
plate. Remove the two screws holding the cable
retainer plate onto the appliance and remove the
cable retainer plate, leaving the control cable held in
place by the square strain relief. Replace the cable
retainer plate that you removed with the new one
provided in the kit. Cable retainer plate style varies
from model to model; the one that came with your kit
should look exactly like the one that you removed
with an added hole.
g. Feed the SCBS harness through the hole in the cable
retainer plate. Collect and capture all wires in this
harness into the split grommet provided with the kit
and install the grommet into hole in the cable retainer
plate. The installation of the grommet is critical as it
insures that the wires will not chafe and/or short out
against the metal edge of the hole in the cable
retainer bracket.
h. You may now reconnect the main control harness to
the SCBS board exactly as it was connected to the
previous board, re-attach the front panel bottom and
reconnect, remount and close up the front panel
assembly.
Содержание L80-029
Страница 15: ...13 L80 029 Rev 5 10 07 ...
Страница 16: ...L80 029 Rev 5 10 07 14 ...
Страница 17: ...15 L80 029 Rev 5 10 07 ...
Страница 18: ...L80 029 Rev 5 10 07 16 ...
Страница 19: ...17 L80 029 Rev 5 10 07 ...
Страница 20: ...L80 029 Rev 5 10 07 18 ...
Страница 21: ...19 L80 029 Rev 5 10 07 ...
Страница 22: ...L80 029 Rev 5 10 07 20 ...