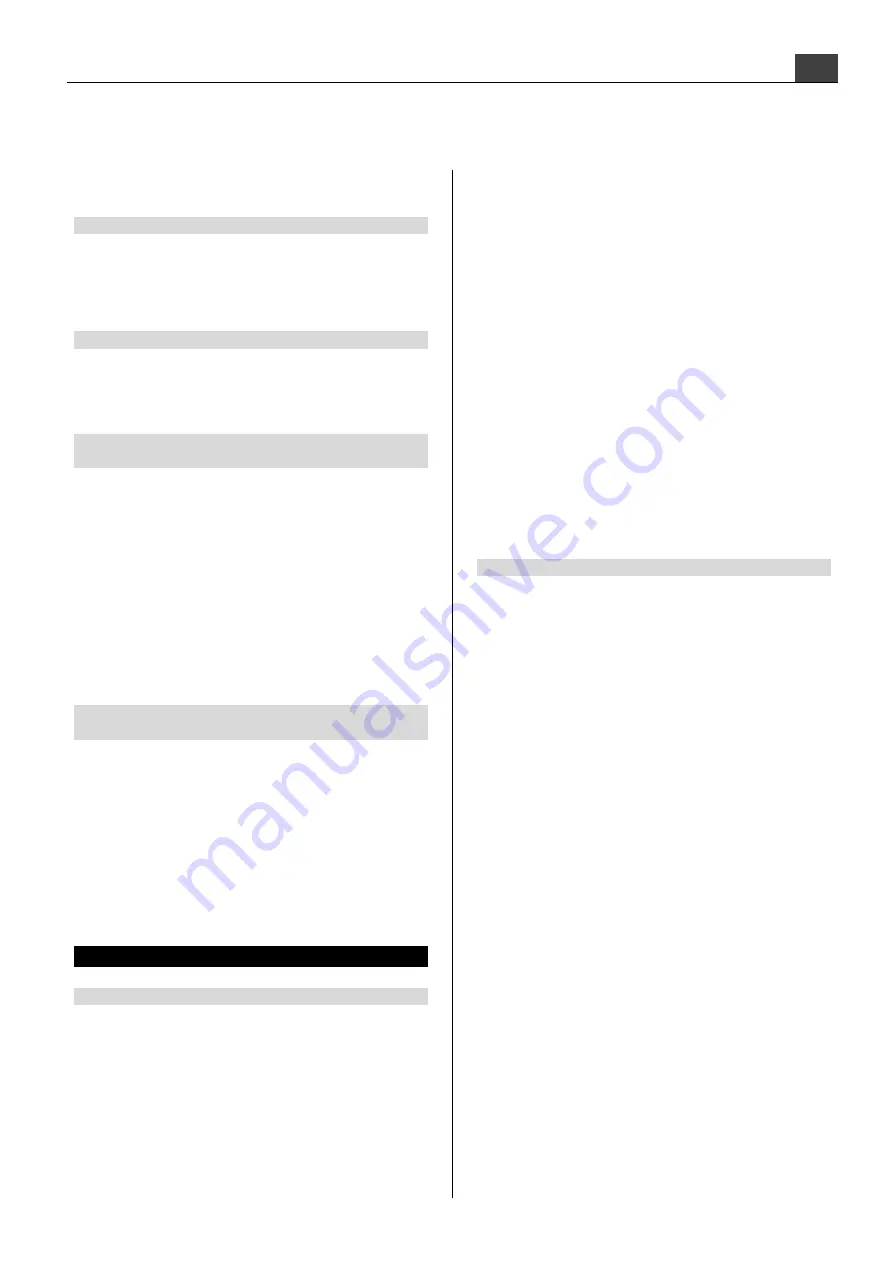
Technical Manual
MT 302-I
8
Make sure that pressure is lower than that for which the valve was
calibrated and the temperature of the gas does not cause malfunctions.
3.2
CONTROL OF THE OUTER SEAL
The leak test of the connections of the valve to the system should be
carried out as prescribed in the installation site.
The outer seal is guaranteed when sprinkling the pressure element with
a foaming agent, no bubbles form.
3.3
CONTROL OF THE INNER SEAL
The inner seal can be checked with the valve in the closed position,
keeping the line pressure at its inlet and checking that downstream of
the valve there is no fluid leakage.
3.4
COMMISSIONING WITH INSTALLATION
DIRECTLY ON LINE (FIG. 4)
When the relief valve is installed directly on the line, namely without
interposing a shut-off valve, proceed as follows:
1) Make sure that the downstream shut-off valve
V2 and the air vent valve 6 are closed.
2) Increase pressure in the upstream segment to the intended triggering
value in one of the following ways:
- if the spring installed on the regulator/pilot allows it, increase
calibration of the pilot regulator until it reaches the desired value;
- connect an auxiliary controlled pressure to the valve 6 and stabilize it
at the desired value;
3) Check triggering of the relief valve and, if needed, adjust it by turning
the adjustment plug 9 appropriately (clockwise to increase the setting
and counterclockwise to decrease it).
3.5
COMMISSIONING WITH SHUT-OFF
VALVE (FIG. 5)
In case of installation with shut-off valve:
Close the shut-off valve 16.
2) Connect an auxiliary controlled pressure to the outlet 17 and slowly
increase it to the intended triggering level
3) Check triggering of the relief valve and, if needed, adjust it by turning
the adjustment plug 9 appropriately (for VS/AM 58) (clockwise to
increase the setting and counterclockwise to decrease it).
4.0
MAINTENANCE
4.1
GENERAL INFORMATION
The inspection and maintenance operations are closely related to the
type of installation. Preventive maintenance is therefore always
recommended, the intervals of which, if not established by regulations,
depend on:
-
The quality of the transported fluid;
-
The state of cleanliness and conservation of the piping
making up the system; in general, after the first start-up of
the plants, they require more frequent maintenance for the
precarious state of cleanliness inside the piping.
It is recommended to periodically check the cut-out value of the valve
following the rules in force in the place of installation and, as
necessary, to provide for a preventive maintenance of the valve and its
pilot.
Regular checks will also affect the status of the external surfaces of the
valve. In particular, one will have to restore the surface protection
(usually paint) in case of their deterioration.
Before carrying out any work, make sure that the section of the system
in which one operates has been cut off upstream and downstream and
that the pressure has been discharged into the affected pipe section.
Also make sure you have a set of recommended spare parts. The
spares must be original Pietro Fiorentini parts.
N.B. The use of non-original spare parts relieves the manufacturer of
any liability.
If your qualified staff takes care of this
maintenance, before disassembly, we recommend applying reference
signs on parts which could pose problems of direction or mutual
positioning when reassembling them.
Also remember that the O-rings and mechanical
sliding parts (rods, etc.) must be lubricated with a thin coat of silicone
grease before reassembling them.
4.2
DISASSEMBLY
With the exception of the OR valve seat (21), where the use of a
special key is required, for the disassembly of all the other components
special keys are not necessary.
Before disassembling, place the reference marks on the
elements to be disassembled.
You should take particular care not to damage the sealing seats and
housings of the sealing rings.
Examine the status of all the rubber parts affected by the seal and
replace damaged ones or those that have been in use for a long time.
Lubricate the surfaces of the moving parts with a thin coat of grease as
described in Chapter 5.
4.2.1 Disassembly and maintenance of the valve
Proceed according to the steps described below for disassembly and
maintenance of the valve, with reference to the parts in the diagram in
Figure 6.
1.
Loosen the ring nut pos
○
8 .
2.
Loosen and remove the adjustment plug pos
○
9 .
3.
Remove the spring pos
○
21
.
4.
Loosen and remove the valve seat pos
○
2
Содержание VS/AM 58
Страница 4: ...Technical Manual MT 302 I 3 Figure 1...
Страница 13: ...Technical Manual MT 226 I 12 Figure 7...